之前,机加工车间多按照操作流程进行设置:设立单独的部门,分别负责车削、铣削以及磨削等工作。这样做是为了将同一类型的专业人员聚集在一起。然而,今天多功能设备在车间中的应用越来越多,各类型人才的交叉培训也越来越丰富。虽然功能相近的设备仍会被安置的一起,但是整个车间的机器却变得越来越多样化,而员工的价值也更多的体现在能够更加自如的操作这些多样化的机器。
但是,Spirit AeroSystems公司正在小范围内尝试不同的运作方式。
在参观该公司设立于堪萨斯州威奇托市的制造园区时,我们还参观了刚开放的五轴加工卓越技术中心。另一家类似的三轴和四轴加工中心位于俄克拉荷马州。这些工厂将类似的机加工能力和专门负责此类工作的人员汇聚在一起。这是退步吗?
事实上,不是。这是加工技术发展所带来的进步。甚至让我们看到了未来加工车间的日常运作方式。
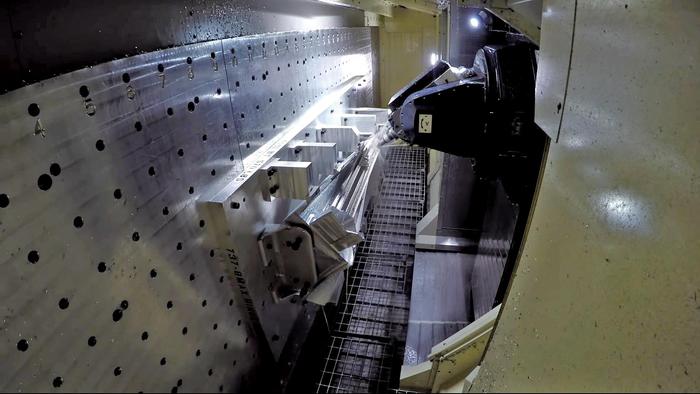
新建卓越技术中心的五轴加工设备
鲜明的对比说明了该中心的价值所在。威奇托工厂正在扩大规模。Spirit主要生产商用飞机的机身(以及其他飞机系统)。尽管2020年某主要飞机型号的订单出现意外下降,但总体趋势仍是增产和人手两方面增加所带来的挑战。该公司的目标是今年增加1000名新员工(不知最近发生的事件会否影响该计划)。但是,相比之下,新的五轴中心对人员的需求比较少。工厂内有各种类型的五轴机床,但是部分机加工作业是在两台由6个Makino Mag 3机加工中心拼凑起来的一体化托盘单元上完成的。每个单元每个班次只需要一名操作员,总共需要6名操作员。另外三名担任后补操作员。因此,九名操作员足以为两个单元的12台机器提供全天候服务。可以说,新增的1000名新员工中,几乎不需要调拨人手到这些单元中。
卓越中心的概念最主要是充分利用车间面积提高产量。与分散式分布相比,将五轴功能的设备集拢到同一个位置,可以节省更多空间。五轴专家在组装时,协调起来也相对更为简单,可以合力解决所有问题。因此,这种做法也能够提高产能。此外,专家们还可以将注意力放在其他机器上。除了负责托盘单元的人手外,工厂内还有很多工人。团队虽然少,但是很强大。Spirit AeroSystems已做好准备,充分利用这种能力,将它的优势发挥到极致。产能增加的原因之一是该公司希望单单是合同加工这一项业务就可以增加到10亿美元。
事实上,很少有制造商能够按照该卓越技术中心设计布局的顺序来购买设备,更不用说一次性配置6台设备单元。但不可否认的是,几乎所有正在进行技术升级的工厂都在持续不断的增加自动化系统的应用。随着自动化程度的增加,车间也面临不同以往的挑战,即一名经验丰富的操作员能够同时监管多少台机加工设备,通过怎样的安排能够更好的应对这一挑战。
因此,将产能集中起来的模式能够起到奋起直追的效果,然而原因并不是将所有人聚集起来做相同的工作。这只是其中的一部分。现在是将所有设备和产能以人为中心进行布局后,才实现了更大的改善,达到了意想不到的效果。
评论 0
正在获取数据......