金属3D打印在汽车设计开发领域具有举足轻重的地位,尤其在发动机进排气侧部件的验证上,优势十分突出。传统的汽车开发设计的金属部件,往往都需要模具,周期长、效率低且费用高,无法快速实现金属原型实物的生产与验证。
采用金属3D打印技术之后,设计人员不但可以把模型设计得更轻量化、更复杂、性能更优异,而且设计好的模型只需要以很低的成本、更短的流程,通过金属3D打印机在几小时或几十小时内的打印和简单的后处理,就可以拿到实物模型。实物模型在试装完成后进行1:1考核实验。如果发现设计不合理,可以马上修改模型,再次进行打印和验证工作,最终模型确定无误后可以批量生产。这种方式加快了汽车设计更新的迭代周期,为汽车行业的技术创新提供了有利条件。
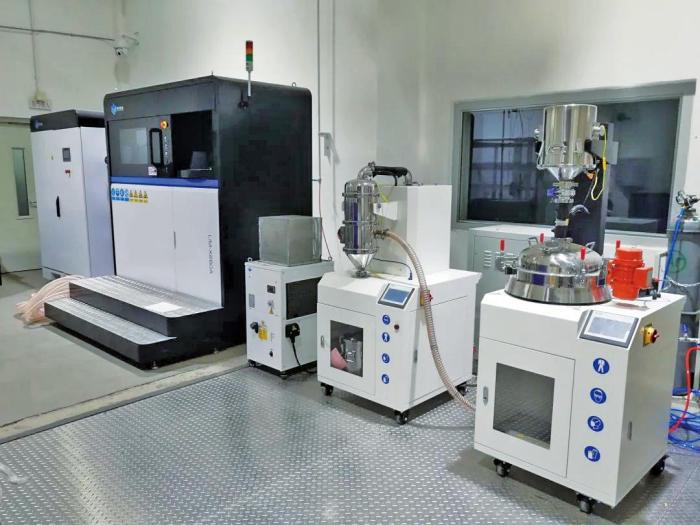
图 福田康明斯所购镭明激光3D打印设备LiM-X260A
北京福田康明斯发动机有限公司(以下简称“福田康明斯”)成立于2008年,是全球领先的动力解决方案提供者,康明斯公司与中国商用车企业北汽福田汽车股份有限公司合资组建,是全球先进的柴油发动机生产基地,主要生产轻型、中型和重型柴油发动机。工厂拥有按照世界领先的技术标准和质量控制标准设计的发动机制造系统,生产设备自动化程度较高的产品主要包括F系列、X系列各种不同排量的发动机,年产能可达52万台。
2019年前后,福田康明斯开始采用金属3D打印技术进行发动机进排气侧部件的研发验证工作。在此过程中,天津镭明激光科技有限公司(以下简称:镭明激光)为福田康明斯提供了良好的技术支持。2020年7月,福田康明斯从镭明激光采购了第一台LiM-X260A型金属激光选区熔化设备,用于发动机零件的升级创新和技术的升级创新试验,为双方合作打下了深厚的合作基础。
据福田康明斯检测中心高级工程师张波介绍,福田康明斯在中国有十多家企业,他们在进行产品开发时发现,目前很多零件在升级创新过程中,原有的模型没办法使用,在对其中某一个尺寸或局部进行改进时,可能会做几个不同尺寸的同一个零件,开模具的话成本会非常高,周期也会很长。要想快速实现这一理念,来做一些验证,他们考虑到运用金属3D打印技术。
“在开发X12N天然气版重型发动机的过程中,我们需要对该型发动机所用的气管进行改造。对零件尺寸和结构做出修改,需要用各种不同尺寸的零件分别来做验证,我们使用了镭明激光的LiM-X260A型金属激光选区熔化设备来进行3D打印,打印出的零件在约750℃的极端条件下,经受住了严苛的测试,大大节省了开发成本,提高了验证效率,进一步缩短整个产品的验证周期。”张波表示。
镭明激光与福田康明斯的合作过程中,做到了快速响应需求,及时提供支持,有效保证了各个项目的时间节点。
“我们对镭明激光的技术支持和售后响应速度十分满意”,张波表示,镭明激光的售后服务非常到位,保证24 h在线服务。设备已经稳定运行18个月,使用频率也很高。在疫情的影响下,出差非常不方便,金属3D打印的快速制造,减少了很多不必要的麻烦,帮助他们解决了很多切实的问题。
随着3D打印技术的不断发展,原型制作、轻量化和量产方面都将在未来得到进一步的深化使用,3D打印技术将会得到更广阔的应用。镭明激光期待与福田康明斯进一步合作,为汽车行业用户提供更加深化的解决方案,助力汽车行业更高效的创新发展。
评论
加载更多