底盘是汽车结构中不可或缺的重要部分,科技含量高且具有支撑并安装不同类型零部件的功能,其质量关乎汽车的整体性能及乘客的出行安全。
汽车底盘系统的机械结构非常复杂,涵盖众多关键的尺寸,任何一个部件尺寸和位置度的偏差都会直接影响整个系统的正常运转。目前我国新能源汽车行业发展迅猛,新能源汽车的底盘系统需要适应于车载能源的多样性以及高度集成的系统模块,对其稳定性和安全性要求更高。
如何高效且稳定地控制底盘系统质量成为汽车制造商面临的挑战。而光学3D扫描仪凭借其高效、高精度与灵活性,对底盘部件测量提供全面的扫描解决方案。本文通过车架纵梁与电池底盘两个案例,重点展示Atlascan多模式多功能3D扫描仪的高性能表现。
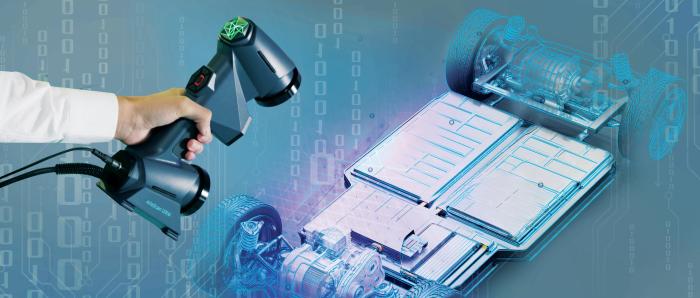
Atlascan多模式多功能3D扫描仪
车架纵梁的典型应用
一款长度为7 m,板料厚度为12 mm的车架纵梁,需要测量安装孔的位置及大小,模拟安装时两端变形量。作为汽车底盘中最长的零件,如果采用盒尺、卡尺等工具对照二维图逐一测量,存在效率低和精度低等问题。
AtlaScan 多模式、多功能3D扫描仪的扫描幅面最大可达600×550 mm,测量速率高达每秒210万次测量,能轻松应对车架纵梁大尺寸检测需求。简单设定程序在工件上来回扫动,即可轻松获取车架表面数据信息,专门的孔位闪测技术,7 min之内提取车架上300~500个孔位数据,再通过专业点云检测软件将采集数据与设计CAD模型进行测量分析,一份图文并茂的检测报告就可以轻松完成了。
该方案只需简单几步就能快速实现孔位、直径及型面的高精度检测,确保后续车架装配质量及其他部件装配位置精度。同时,型面检测结果能够更加精准地反映出模具加工精度和材料变形量,这些数据对前期加工分析提供很大的帮助。
电池底板的典型应用
电池包的安装孔位有着严格要求,目前检测电池包的外形尺寸及安装孔位依靠人工卡尺测量、效率和精度不理想,产品合格率偏低,需要快速精确检测。
同样还是使用AtlaScan 多模式、多功能3D扫描仪获取表面数据信息,测孔模块快速提取电池底板安装孔位,实现电池底板孔位及外型尺寸检测,最后完成数据检测,快速生成一目了然的孔位及外型尺寸报告。该方案扫描耗时5 min,报告耗时10 min,和传统检测相比,三维扫描更加高效、精准且方便。
综上,AtlaScan多模式、多功能3D扫描仪除了具备同类产品的优势特点之外,其新一代设备在软硬件性能的大幅升级后,拥有超大的扫描范围、超快的扫描速度、超高的精度与分辨率和更广泛的材质适应性等诸多优势,适用于各种复杂扫描场景的应用,其中的孔位闪测功能可高效提取零件关键数据,快速检测出孔位尺寸,为企业在新能源赛道上跑出加速度提供更大助力。
评论
加载更多