随着液压行业市场规模的不断扩大,液压元件也正向智能化、高端化方向迈进。高效、高标准、高可靠性系统集成发展已成为液压元件的发展趋势。
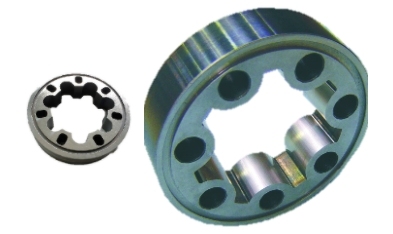
在液压元件加工中,如何做到既能保障精度和质量,又能提升效率、降低成本,联合磨削平面成型磨削给出了答案!
高效便捷
双主轴立式液压定子磨削解决方案
根据几十年液压定子磨削工艺经验,以及不断的测试验证,德国保宁推出了最新的双主轴立式液压定子磨削解决方案。该方案在德国保宁最新开发的PLANOMAT XT 408型磨床上,采用立式磨削主轴以及垂直夹紧定子的专用工装。相较于卧式主轴的磨削方式,能获得更好的磨削精度和一致性,同时可以保证极高的生产效率。
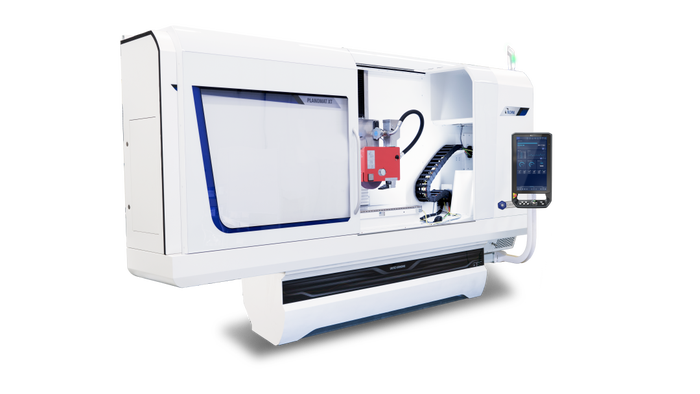
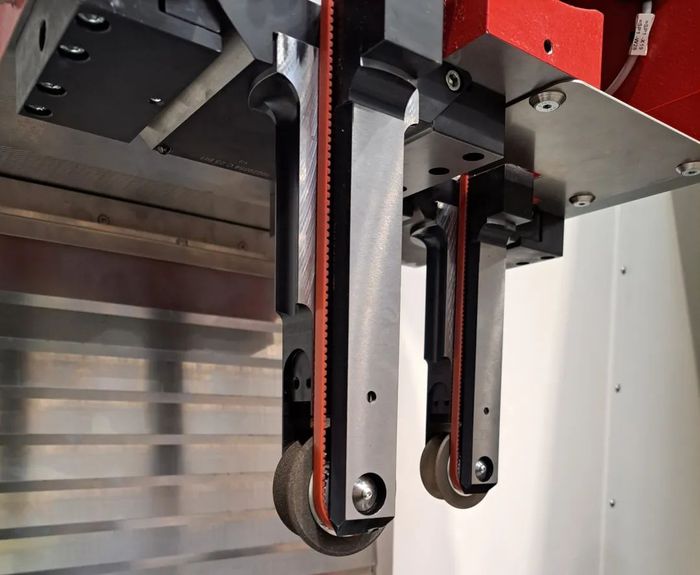
德国保宁采用经过优化的磨削工艺,不是简单的垂直进给磨削方式,从而保证整串夹紧工件内腔型面的磨削精度和一致性。同时可以根据客户需求,配备单个或者两个磨削主轴,从而轻松满足不同客户的工艺要求。
那么,这套解决方案的亮点在哪里?能为客户生产带来哪些优势?我们接着往下看。
1. 更可靠配置——带有定心芯轴的夹紧系统
立式液压定子磨削解决方案能否保证加工精度,关键在于这套垂直夹紧系统。德国保宁设计的垂直夹紧工装,包括压紧顶板、夹紧芯轴、夹紧销、基板等。夹紧高度最大可达135mm,非常适用于高效生产。
操作时,通过旋转压紧顶板的卡扣,即可夹紧或者松开整串定子工件。夹紧芯轴插入到成串定子工件内,通过端齿装置锁定位置,这样就会在工装内部将所有工件中心定位。以便操作人员在很短的时间内,就能完成整串定子工件的夹紧工作。并且夹紧精度和中心定位精度极高。非常适合液压定子的大规模加工生产。
2. 更强劲设计——模块化双主轴方案
联合磨削集团还为这套解决方案,配备双主轴选项,分别用于工件的粗磨和精磨,更加满足国内液压定子的生产要求。
磨削功率约为7kW,最大切削速度80m/s。两个磨杆均配备快换接口,半小时内即可完成更换磨杆,大大降低了生产换型时间;采用高质量的主轴+电机,非特制产品,可以提供更快的转速。
3. 更优化组合——保证高精度、高效率生产
在磨床加工区域内,除配备有高精密立式分度单元(04)、莱曼液压夹紧装置(05)以及EROWA零点中心夹紧系统。还配有修整单元(07)和SAMSOMATIK空气测量系统(08)。
修整单元带有震动传感器(11),当砂轮接近修整单元时,降低进给速度以便进行修整,从而大大提高效率。
空气测量系统(08),通过喷嘴喷出压缩空气,磨杆缓慢移向喷嘴位置,当空气阻力升高时,磨杆停止移动并且确定位置变化量。用于热膨胀测量和自动位置补偿,从而保证了最佳磨削精度。
砂轮暂存装置(12),在不需要停止主轴转动的情况下,安全放置砂轮。例如操作人员临时打开机床门时,不需要停止主轴转动,减少了非加工时间,提高了生产效率。
4. 更灵活便捷——自动化单元
PLANOMAT XT定子磨床,除了能进行手动或者机器人上下料外,还可以配备UNIversal autoMATion自动化单元(UNIMAT)实现真正意义的自动化生产。
在没有人员照料的情况下,可以自动生产一小时。自动化单元布置于机床右侧,通过自动门连接。在自动化单元内通过输送道和托盘自动运输工装,托盘由传感器监控,因此没有碰撞风险。托盘带有防错功能,不会以错误的方式进入输送道。
PLANOMAT XT 408型磨床采用了最新的C.O.R.E.操作面板,加之本身具有的更高刚性、更大行程、更佳冷却回路设计等优势,确保了连续精密加工能力。
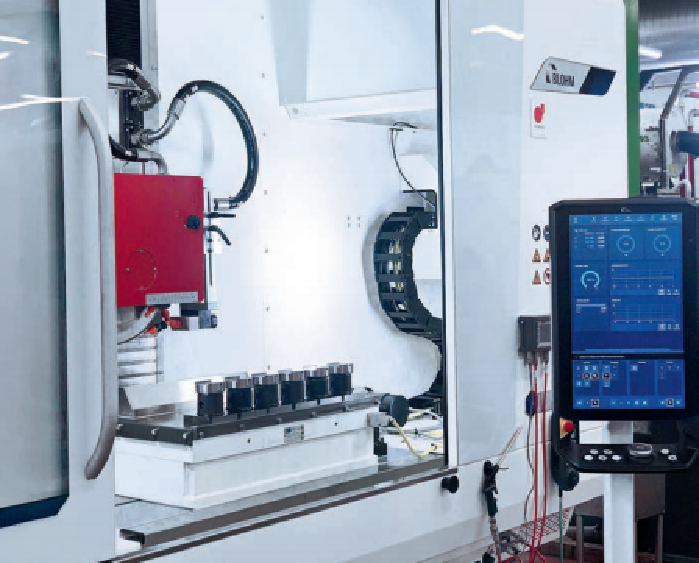
总之,通过立式磨削加工液压定子,可以快速实现重复装卸,特别对于高精密工件,易于换型和维护;在机床外安装、调试,减少停机时间;单主轴和双主轴,对应粗磨和精磨,可以单独设定,满足不同客户需求;自动化系统可以降低节拍时间,减少错误源。根据解决方案的不同,可实现长达一小时的无人操作,提高生产效率。
简言之,带给客户的是兼具可靠性与性价比的选择。
5. 更贴心扩展——独立开发分体式砂轮方案
除此之外,针对Geroler定子,德国保宁还独立开发了分体式砂轮方案。通过分体式砂轮磨削GEROLER工件,砂轮型面可以被修整的更尖锐。由于避免磨削陡峭的侧面,从而显著减少去除量。
在相同去除量条件下,进给速率可以提高到5倍,同时降低砂轮和金刚石滚轮的磨损、降低节拍时间。在加工过程中,可以加工侧面高于圆心位置的型面,用于解决内齿两边出现毛边尖角的问题。
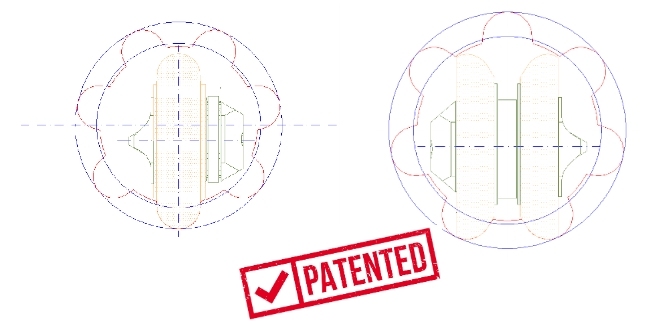
作为平面与成型磨削的好“搭子”,联合磨削以更精准的质量、更可靠的工艺,为液压、透平、航空航天、半导体等多个行业,提供更多可能。
文章来源:United Grinding 优耐特磨削机械
图片来源:United Grinding 优耐特磨削机械
转载平台:微信公众号
责任编辑:朱晓裔
审 核 人:李峥
评论 0
没有更多评论了