切削条件的影响
当切削加工时,最希望达到的是加工时间短,刀具寿命长,加工精度高。为此应很好地考虑工件材料的材质、硬度、形状、状态及机床的性能。由此选定刀具,选择高效率的切削条件。
切削速度
切削速度对刀具寿命有很大的影响。提高切削速度时,切削温度就上升,而使刀具寿命大大缩短。加工不同种类、硬度的工件,切削速度会有相应的变化,而选择适合的刀具材料是非常必要的。
切削速度的影响
切削速度提高20%,刀具耐用度降低1/2;切削速度提高50%,刀具耐用度将降至原来的1/5。
低速(20—40m/min)切削易产生振动,刀具寿命缩短。
切削深度
车削时,工件回转一转车刀向前的移动量即为进给量。铣削时指铣刀回转一圈机床工作台移动量除以刃数之值,即每刃进给量。加工表面粗 糙度与进给量有很大关系。通常由表面粗糙度要求决定进给量。
进给量的影响
进给量小,后刀面磨损大,刀具寿命大幅降低。
进给量大,切削温度升高,后刀面磨损也增大,但较之切削速度对刀具寿命的影响要小。
进给量大,加工效率高。
切削深度
切削深度是由工件的加工余量、形状、机床功率、刚性及刀具的刚性而确定的。
切削深度的影响
切削深度变化对刀具寿命影响不大。
切削深度较小或微小时,会造成刮擦、只切削到工件表面的硬化层,缩短刀具寿命。
切削铸铁表面和氧化皮表面层时,应在机床功率极限范围内,尽量加大切削深度。否则刀刃尖端只切削工件表皮硬质层及杂物,会造成刀尖破损或产生异常磨损。
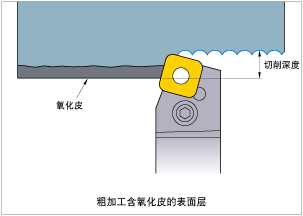
评论 0
没有更多评论了