新能源汽车是我们国家的产业政策所激励的。针对电动汽车零部件的加工,MAPAL 现今已经提供有多种多样的创新型加工解决方案。
电机壳的主孔直径比较大(D280左右),多个台阶,直径跨度大(轴承孔到电机孔)。要实现精密加工,对刀具和机床都提出了尖锐的挑战。
电机壳体的所有其他加工工序都可在 HSK-A63 主轴的机床上完成。在过去,主孔的加工则必须在带有 HSK-A100 主轴的机床上进行。究其原因,一方面是需要高达 500Nm 的切削力矩,另一方面是受到最大允许的刀具重量和转动惯量的限制。为了能够实现高节拍的经济型加工,要求找到一种能够在带有很小接口的一台机床上完成全部工序的解决方案。这种机器要求以高转速、低购置成本和低运营成本,以及低能耗为标志。
电机孔的精度对电机的性能有很大的影响。目前欧洲对电机孔的精度要求多为IT6. 而我们国内的主流制造厂能够达到的精度为IT7,差了一个等级。
生产效率在该零件的加工中也至关重要。制造业希望有这种轻型、复合结构的刀具。这样,在一次换刀的情况下能够完成全部主孔的加工。
为此,MAPAL推出了图示刀具:
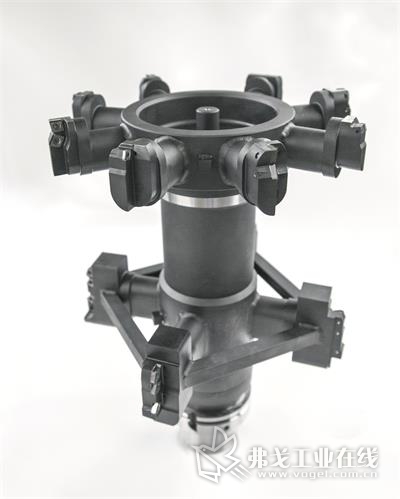
这是一种一种超轻结构的精镗刀具。采用中空结构,为了进一步减轻重量,冷却液通道也进行了特殊处理。在刀体的外围焊接切削功能模块。将多个台阶集合到一把刀具上。
这把刀具仅有大约 10 千克的极低重量,为在配置小主轴的机器上使用创造了先决条件。
除重量之外,MAPAL 也对冷却通道进行了优化。一个专门的反面冲洗保证了明显高效的排屑。由此也保证了切屑不会划伤加工表面。
由于采用了MAPAL传统的导条刀具结构,它制造出来的产品精度可以达到IT5的等级。
经过和客户的反复沟通,我们在中国市场上收到了很好的效果。例如在广州地区,由于采用此刀具,客户减少了机床的使用量,加工精度也满足了IT6的要求。客户决定以后在新产品的加工中都采用此种结构。
评论
加载更多