一辆普通汽车,其独立零部件数量在2万之多。大到车体框架、箱体结构,小到螺母、销钉,每个零部件的质量都直接影响着汽车的可靠性。
本期,让我们以转向器、皮带轮、转向节几个典型解决方案,解锁海克斯康贯穿设计工程、生产制造、计量检测完善的解决方案能力,了解汽车零部件从多体动力学仿真到复杂形状检测的智能制造之路。
一键式检测方案:复杂形状零部件
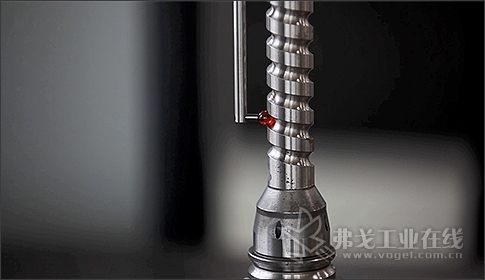
针对汽车复杂零部件尺寸多、编程难等特点,海克斯康提供一系列专用软件测量模块,可以完成零部件的一键式测量。同时可以定制化检测界面与检测报告,为复杂零部件加工提供可靠保证。
典型方案:转向器全尺寸智能检测
· 适用零部件:转向螺杆、转向螺母、摇臂
· 检测项目:转向螺杆:滚动形状、导程变化等;转向螺母:滚动形状、导程变化、齿条参数等;摇臂:渐开线轮廓等
循环球式转向器作为常见的转向器类型,具有传动效率高,操纵轻便舒适等特点。海克斯康推出的汽车转向器解决方案,利用独特的超高速四轴联动和3D自定心扫描技术,实现了多种规格转向螺杆、转向螺母和摇臂的全尺寸一键式测量。参数化检测界面,全封装的软件编程,行业领先的专业算法和定制化图形报告,为转向器部件的加工、修正提供了更加可靠的质量依据。
自动化集成方案:连通加工中心料线
智能制造意味着人机料法环的连通,在汽车零部件制造方面,海克斯康将专业的检测中心与加工中心、车铣中心、清洗中心等连通,打造全自动加工、检测一体化生产线,并通过智能化数据存储分析,反馈至每一生产环节,形成完善的智能制造循环系统。
典型方案:转向节自动化集成方案
转向节自动化智能检测方案,在生产线上采用行架机器人上下料,自动识别、自动检测的方式,实现多种转向节测量过程的自动化、智能化,是目前业内唯一的转向节智能制造解决方案。
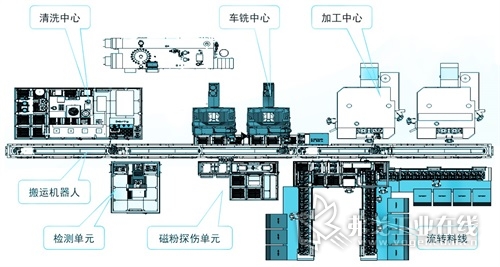
· 系统功能:自动周转、自动上下料、自动识别、自动装夹、自动测量、自动分拣、数据自动存储及统计分析、智能显示设备状态及报告展示
· 方案优势:从无到有、高柔性、自动识别工件信息、高检测节拍,提高检测效率与设备利用率、定制化报告与UI、智能信息管理
整套系统的自动化,完全替代以往的人工操作,原人工检测+三坐标测量1件的时间约为10分钟,采用本方案后,自动在线测量1件的时间约为3分钟,测量10件的时间约为25分钟,检测效率提高到4倍。
动力学仿真方案:优化设计参数
海克斯康拥有经过行业认可的车辆动力学模拟仿真解决方案,全球25大汽车主机厂中,有24家选择了我们进行汽车动力学研究。小到零部件动力分析,大到性能路面试验和道路载荷测试。通过海克斯康Adams Car Studio建立的功能化数字样车的建立,用户就可以利用虚拟的试验台架或试验场地进行子系统或整车的功能仿真并对其设计参数进行优化。
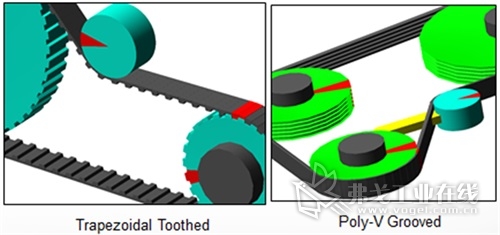
典型方案:皮带轮带传动评估分析
皮带轮属于盘毂类零件,一般相对尺寸比较大。海克斯康Adams/Machinery软件为设计人员和工程师提供了一套定制的工具套件,其中Adams Machinery Belt是一个高效的带传动专用工具,可对多种类型的皮带轮进行建模及评估,包括一般平面带、V型带、楔形带等,研究传动带系统传动比、张紧器变化、带的动力学行为等对系统性能的影响。
所有品质的源头,都来自高标准制造流程的反复打磨。除去智能检测、自动化系统、系统仿真外,海克斯康在汽车行业还提供生产制造CAD/CAM加工、大数据分析和管理等解决方案,全流程赋能汽车制造。
评论 0
没有更多评论了