增材制造技术的发展迄今已经超过30年,过去该技术更多被用于产品试制阶段的原型制造,因此从未得到广泛关注。但是在最近五年中,对增材制造技术的关注度快速提高,我认为主要原因包括以下几点:
第一,产品设计趋势的变化提升了对增材制造技术的需求。近年来,随着制造业的整体产能发生全球性的过剩,市场竞争日渐加剧。为了在细分市场中取得竞争优势,制造企业开始改变传统的“设计-制造-销售”模式,转而采用“用户参与设计”与“制造服务化”相结合的方式。竞争的关键从价格变为用户的“总拥有成本(TCO)”。为了降低总拥有成本, 诸如轻量化、功能集成化和可定制化的产品设计开始流行,而增材制造技术恰好是实现这类设计的最佳工艺之一。
第二,技术的成熟度提升促使企业的接受度提升。2018年10月,GE庆祝其使用增材制造工艺生产的LEAP发动机燃油喷嘴正式交付第30 000件。几乎同时,西门子也宣布其一台SGT700燃气轮机上采用增材制造生产的燃油喷嘴无故障运行超过8000 h。而在汽车行业,BMW也于2018年底正式宣布其i8 Roadster的顶棚支架(图1)的量产将完全采用增材制造工艺。这些经典案例充分证明了增材制造工艺的成熟度已经达到了量产级别。
第三,成本的持续下降进一步激活了市场需求。随着越来越多的材料供应商进入市场,竞争日趋激烈。在过去的五年间,金属增材制造所用材料的市场价格平均下降了超过40%,个别铁基材料的市场价格更是下降超过70%。与此同时,设备和工艺稳定性的提升也使得服务商可以开发一些量产工艺,减少材料和惰性气体的浪费,并充分利用设备产能。在这些因素的作用下,增材制造的综合成本也在显著下降。成本的下降开始吸引更多的工业企业思考增材制造的商业价值。
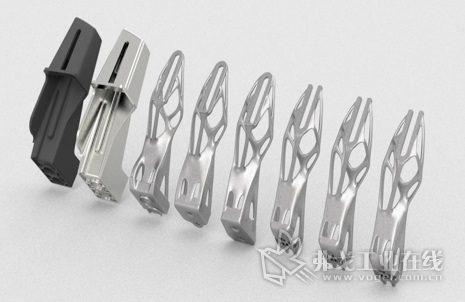
增材制造技术优势明显
从字面意义上来讲,增材制造的加工过程中材料是通过各种手段逐层堆积出来的,这与传统制造中先形成坯料再采用减材方式去除材料的过程是不同的。这种方式最大的优势,同时也是终端用户关注的重点在于:
第一,实现了对设计自由度的释放。受传统工艺的限制,过去的产品设计往往不得不牺牲一些使用性能或者不得不提高装配复杂度。而使用增材制造逐层堆积的方式,一些非常复杂的结构也具备了一次性制造的可行性。从而带来了巨大的潜力。
第二,支持按需定制。传统开模具后批量制造的模式无疑仍然是成本最优的方式,然而随着“多品种小批量”的趋势日益明显,能够支持按需定制的免模具制造方式变得越来越有吸引力。比较典型的案例包括极致盛放的定制化礼品、MINI的定制款车辆内外饰件、还有各种定制化的医疗用植入物等。而对于模具本身这种很典型的按需定制化产品,增材制造无疑是非常有优势的,从制作铸造用的砂型或腊模,到为注塑或者压铸模具制造随形水路,增材制造方式已经证明了其巨大的商业价值。
第三,降低供应链总成本。增材制造正在改变产品的MRO(Maintenance Repair Operating)方式。在传统制造方式下,为了提升对售后服务需求的响应速度,供应链中的企业不得不背负巨大的备件库存。而利用增材制造技术,可以快速实现零件的修复甚至重新制造,从而帮助制造企业缩短备件交期,从而降低库存成本。在当前国际贸易保护主义抬头的大环境下,部分跨国企业甚至开始探讨利用增材制造的来规避实物进出口的关税成本。
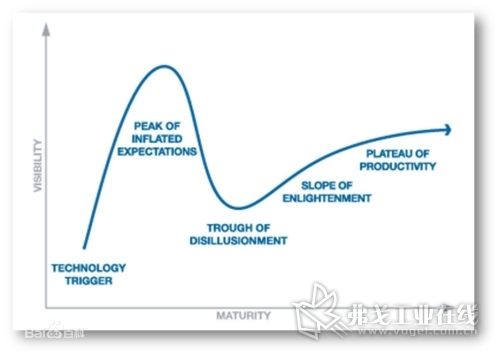
增材制造技术在中国市场的应用现状
按照Gartner技术成熟度曲线的定义(图2),我认为增材制造在中国正在经历第三个阶段,即泡沫化的谷底期。在这个阶段,许多加工服务厂商在早期资本推动下投入的产能正处于艰难的发展过程中,其来源在于多数订单仍然是试制件,而不是稳定而持续的量产件。这说明制造业总体上对金属增材制造仍处于观望的状态。这种观望是可以理解的,一方面现有的金属材料增材制造技术,包括选区激光熔化(SLM)、电子束选区熔化(EBM)、激光近净成型(LENS)和电弧增材制造(WAAM)等在内的技术,在成型尺寸、材料、加工精度、加工效率和成本上各自存在局限性,而且如多射流熔融(MJF)等这样的新技术也在不断涌现。另一方面,中国制造企业的创新研发能力尚有不足,如果产品在设计阶段没有突破,增材制造工艺的价值将无法显现出来。
当然,机会也正在蕴育中,在技术方面,新材料、新设备和工艺正在不断出现;在商业方面,一些领先的设备和服务厂商正在通过资本进行资源整合。经历过这个阶段后,预计中国的增材制造应用将在3~5年内进入稳步上升的光明期,尤其是在航空航天和医疗领域。
金属增材制造技术的发展前景
对于金属材料的增材制造来讲,材料、设备和工艺是影响最终产品质量的三个基本要素,未来所有的技术发展都将围绕这些基本要素。相关领域的研发重点包括:
第一,更多样化的材料以及现有材料的改性。相对于传统金属材料上千个牌号,目前适用于金属增材制造的材料牌号仅有数十种,这也从某种程度上限制了增材制造的应用。近年来随着市场关注度的提高,材料供应商和解决方案供应商开始联合进行新材料以及针对性工艺的开发,例如近年来出现的针对纯铜材料或者钨合金材料的开发。
此外,通过对现有材料进行改性,可以帮助提高加工质量或者降低成本,例如经过改性的钛合金材料可以减少对热等静压处理的依赖,而如果新的采用传统粉末冶金材料的增材工艺通过验证,预计可以将材料成本降低10倍以上。
第二,更广的成型尺寸范围。现有的金属材料增材制造工艺已经可以覆盖比较大的零件尺寸范围。然而针对一些微小尺寸或者是超大尺寸的结构时仍然存在较大的局限性。面对微小尺寸结构,由于后续加工的难度较大,用户往往希望利用增材制造工艺一次完成,这对加工精度和表面质量提出了很高的要求。而面对超大尺寸结构时,结构的热变形往往较大,导致合格率显著下降。为解决这样的问题,需要从产品设计、材料、设备和工艺多角度入手来解决。
第三,替代工艺和/或工艺优化。以双激光的SLM工艺为例,其加工效率在2017年就已经可以超过100 cm3/h,但是这个效率仍然无法满足部分工业企业的需求。在设备厂商采取了各种手段后——例如增加到四激光、提高激光功率并增加铺粉层厚、加快铺粉速度等,加工效率已经接近理论极限了。为了进一步提升加工效率,替代工艺——例如多射流熔融(MJF)——将会是热门的选项之一。
针对现有工艺的优化也是现阶段技术发展的重点之一,其中就包括基于虚拟仿真的工艺优化设计。利用虚拟仿真软件,工程师可以在制造前优化摆放方向、合理设计支撑结构、尝试不同的能量源扫描路径等,从而提高加工质量、提高效率且降低成本。
评论
加载更多