在传统结构中,冷却通道在工件中铣削,然后在多个工作步骤中再次关闭。如果想要制造一台结构复杂的发动机,意味着整个工作至少要持续半年,因此成本也非常高。此外,航空航天工业的规格要求极高,整个制造过程需要轻质结构,材料还必须能够承受极高的应力。
选择性激光熔化技术(SLM)为组件的金属增材制造提供了许多可能性。例如,可以直接使用内部结构和一致的轻质结构来进行制造。另一个优点是将许多部件集成到一个组件中。这种功能集成和后续处理需求的减少使得制造过程的成本大大降低。以火箭发动机为例,Cellcore公司展示了如何在航空航天领域最大地发挥SLM工艺的优势。Cellcore与SLM Solutions公司合作采用材料IN718制造了一台整体式发动机。
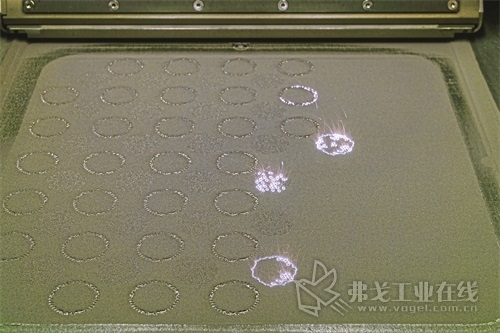
Cellcore对发动机进行增材制造的建造室为SLM Solutions公司的SLM 280
Cellcore和SLM Solutions公司制造的发动机由一个推力室(液体燃料发动机的核心元件,带有燃烧室壁、燃料入口)和一个带有氧化器入口的注射头组成。在燃烧室中,发生化学反应并释放气体。由于产生了热量,这种气体膨胀并以巨大的力量喷射出来。这种反向反应提供了驱动火箭所必需的推力。在燃烧过程中,燃烧室内会产生很高的温度,因此必须冷却壁面以防止烧毁。为此,液体燃料、煤油或氢,通过燃烧室壁内的冷却通道向上引导,然后通过注射头进入燃烧室。在那里燃料与氧化器混合并在火花塞的助力下燃烧。
金银丝工艺结构冷却系统,效率更高
使用SLM Solutions的增材制造工艺可以将制造时间缩短到5个工作日,从而大大节省了时间和成本。采用这种SLM技术生产的整体式火箭发动机由喷射器和推力腔组成,融合了整体设计,即将多个独立部件组合成一个组件,具有多功能轻质结构。
核心元件为Cellcore开发的结构,只有借助SLM技术才能进行生产。既确保了足够的强度,又非常适合散热。这种结构冷却系统的特性大大超过了传统方法,例如直角、同心运行的冷却通道。结构冷却系统提供了强度与所用质量之间的最佳比率,并且可以降低流动阻力,增加有效表面。因此,不仅更高效,而且还集成了其他功能。与传统制造的组件相比,这种晶格结构还能进一步减少重量。
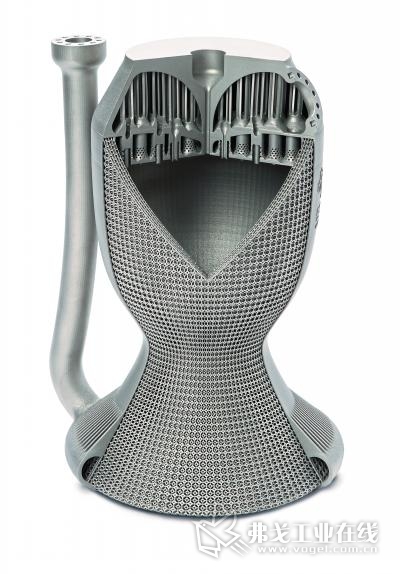
Cellcore开发的结构冷却系统保证了强度和使用质量之间的最佳比例
SLM Solutions公司支持Cellcore设置复杂组件,从而为SLM工艺做好最佳准备。为部件几何结构开发特定参数作为其中一部分,包括组件优化和在机器空间中的最佳组件定位。此外,还确定了建造的关键区域,以便排除错误,保证建造工作的顺利开展。
为了满足航空航天工业对材料的高要求,发动机采用镍铬合金IN718制成。IN718是一种可沉淀硬化的工作材料,具有优异的拉伸、疲劳、蠕变和断裂强度,最高温度可达700℃。这使得IN718成为飞机和燃气轮机部件以及各种高温应用(如火箭发动机)的重要合金。在传统加工中,这种材料难以加工并且会导致严重的工具磨损。
发动机采用SLM Solutions的SLM 280机器进行打印。该机器的外形尺寸为280mm×280mm×365mm,采用专利多主题技术。使用PSV电源装置处理粉末,无需从粉末瓶中手动填充粉末。利用集成在PSV中的超声波筛,加工之前对可用粉末进行筛分,以防止过大的颗粒或异物进入加工过程。PSV与SLM机器之间的粉末输送完全由气流输送自动完成。
加工完成后,首先要拆开组件并将其从底板上取出。然后,移除支撑结构并对部件开展后续工作。Cellcore首席执行官Andreas Krüger确信:“这项概念研究显示了增材制造的巨大潜力,无论是在航空航天还是其他领域。SLM Solutions这种技术的可能性给我们留下了深刻的印象。特别值得一提的是,这种极其精细的多功能冷却结构对细节的忠实度和质量都非常有说服力。”利用SLM技术,可以节省昂贵且耗时的制造步骤并简化发动机结构,从而大大降低成本。在传统制造中,注射元件是单独生产的,经过后续处理后分别用螺栓固定。
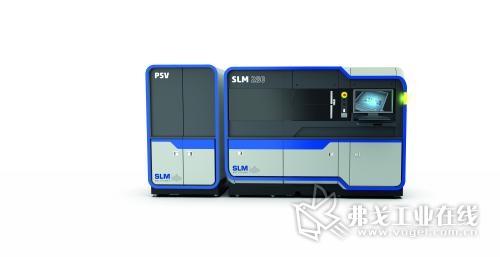
SLM Solutions的SLM 280生产系列配有粉末供应装置,节省了用户手工填充工作材料的时间
结构复杂但后续工作简单
另外,在壳体中铣削氧气凹槽,用盖子封住,以免气体逸出。螺栓安装的下一步依次在洁净室中进行。
许多需要开展后续工作的工作步骤,或者至少是装配步骤,可以在增材制造中进行组合,从而减少步骤。尽管部件结构复杂,但增材制造将后续工作最小化,同时避免了严重的工具磨损。
制造该发动机后,Cellcore的工作尚未全部结束。Andreas Krüger说:“我们目前正在研究如何将这一原则应用到其他项目中。例如,在发动机和涡轮部件,或回火工具上可以获得巨大的附加值。”
评论 0
正在获取数据......