钢轨是轨道交通行业的重要组成部分,列车风驰电掣的背后需要钢轨提供连续、平顺和阻力最小的滚动表面作用。
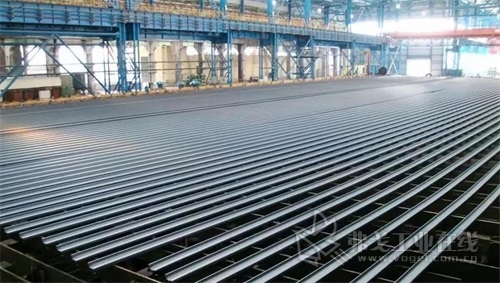
钢轨长材制造难题
列车钢轨动辄长达百米,长度大,轧制时间长,终轧温降大,在质量检测方面容易造成尺寸公差不一致的情况,而复杂断面型材的尺寸和表面缺陷热态检测更是非常困难。
面对钢轨轮廓几何尺寸、表面缺陷(凸起和凹陷)、平直度/扭转等检测项目,传统测量方式只能进行定性测量,等钢材冷却后再通过肉眼检查,或者立项通过检测设备进行非破坏性检查,准确度与效率都达不到需求。
长材智能制造解决方案
海克斯康集团NEXTSENSE团队基于OSIRIS Hot/Cold设备,结合RCx和FMG系统推出的适用于钢轨等长材智能制造解决方案。集成先进的激光光切技术,以专业的测量设备和权威的测量软件为平台,提供高温环境下的针对表面质量、尺寸轮廓和平直度等的全自动在线检测方案,配合工件设计与工程设计、计量检测和智能数据监控与分析等丰富的选项,打造贯穿产品全制造周期的综合性解决方案。
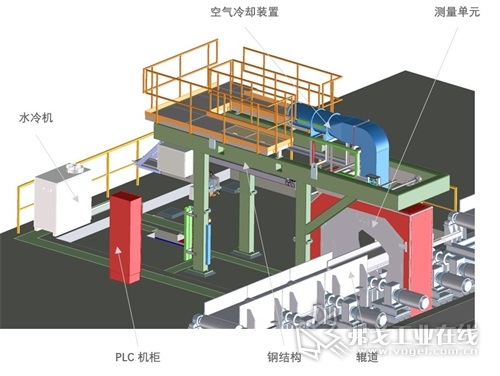
系统实现了与智能信息管理系统实施通讯,提供测量设备、料线、冷却系统等的实时状态,实现整套系统的任务管理。其中专业的检测系统为长材制造提供了全方位的质量保障。
更全面的测量解决方案
测量解决方案主要由在线自动检测专机和便携式手动测量系统两部分组成。
轮廓尺寸与表面质量综合检测专机
采用固定式光学测量系统,用于生产线上连续检测热轧或冷轧产品的表面和尺寸精度,可以在高达1200℃的温度下进行测量。同时实现长材尺寸轮廓和表面质量的精准检测,并且在长材热成型阶段就反馈其表面质量和轮廓尺寸数据,将质量控制前移,极大降低不合格品的生产。
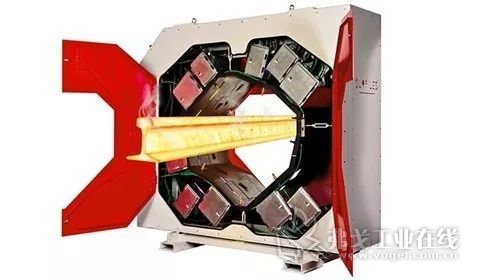
此外,还可配合移动便携式轮廓检测,灵活地对中间料料型进行抽检,全面掌握轧件的变形量,对轧机调整、孔型状态监控、产品开发提供有力帮助。
平直度检测专机
采用先进的激光光切技术和专利算法,将平直度参考点放在面的维度进行测算。既可对固定状态的工件进行扫描,也可对运动中的长材进行实时测量,并通过激光传感器实时补偿路径。即使更换成不同尺寸规格的工件,也能确保整个工件全长度的平直度测量,而无需调整测量系统。
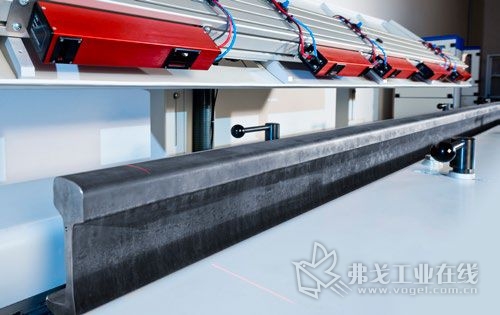
便携式轮廓尺寸检测专机
针对长材热轧过程中机架料形的轮廓检测。独创的旋转式全轮廓测量,三条激光线误差校正技术,以及高效的软件算法,确保了快速精确的测量结果。钛合金C型测量框架和防水防尘的传感器封装,可适用于恶劣工况下“红”钢的移动式在线轮廓检测。
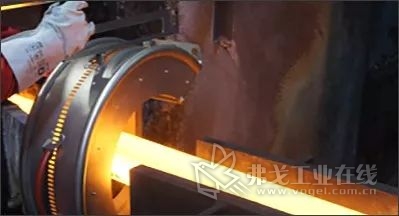
各轧线、机架、道次的测量数据可以在平板电脑实时查看,并上传至全厂L2,达到全线轧制监控。
轧辊孔型检测专机
应用手持式轮廓测量仪,准确便捷地实现对轧辊型的数字化非接触检测,测量数据可以自动与用户CAD图纸模型进行对比并显示尺寸偏差。
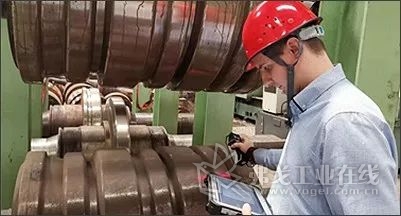
用户可根据模型组的参数定义自动创建多种轧辊凹槽的参考模型(目标轮廓)。针对每个轧辊可创建相应的测量计划,适用于不同类型的轧辊孔型,并且检测结果在平板电脑上即刻显示。
更专业的检测系统组合
智能识别系统
采用光学字符识别技术(OCR)可对工件编码自动识别,记录工件的身份信息和测量结果,可识别不同类型和不同尺寸的长材。
自动测量控制系统
检测系统的测量由光栅系统触发控制,通过将光栅固定在辊道的纵向实现。当长材经过进料光栅时,触发测量程序。而当轧件离开测量系统,安装在出料侧的光栅将发送信号示意测量结束。
一键自动校准系统
通过集成在系统中的校准板来实现自动校准。仅需一个按钮,校准装置即自动旋转并进行测量,数秒内完成校准,即使处于测量位置。
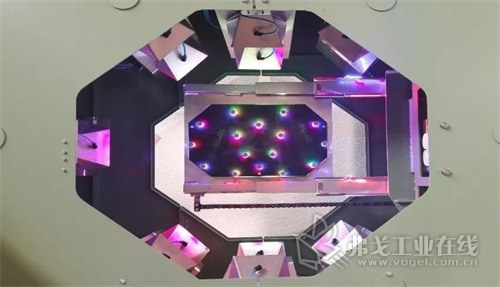
自动吹扫系统
吹扫单元可以将检测件表面的水和氧化铁皮清理干净,避免异物对激光路径的干扰,保证检测结果精度。
冷却系统
冷却系统通过水冷保护层、传感器箱体内部的压缩空气循环散热系统、每一个传感器单元(摄像机/传感器)的水冷系统完成冷却任务。
目前,已有多家行业制造商选用海克斯康的长材解决方案。针对不同客户的定制化方案,助力其达到制造行业内的领先地位。未来,海克斯康将继续以绿色发展、低碳发展、提升产品质量、智能制造为原则,助力我国钢铁工业的高质量发展。
评论 0
正在获取数据......