历史上,表面处理一直是一个在工具室、机械车间和生产部门有争议的话题。多年来,表面质量是机器操作员的唯一责任。工匠们不断地协商,经常激烈地争论,决定一个成品是“好”还是“坏”。
即使在整个行业中出现并广泛实施了质量控制程序,但人的判断仍然是评价表面质量的一个重要因素。如今,大多数机械加工和研磨零件的高精度以及它们的高制造成本使得表面测量的主观方法不再适用。
几乎每个制造商都应该关心他们生产的零件或产品的表面质量,无论他们谈论的是否是通过铸造工艺、轧机、电火花加工、表面研磨或超精加工操作(如珩磨或研磨)产生的表面质量。然而,许多车间并没有尽可能地使用表面散射量测仪器。
在许多情况下,重要的是重新审视表面处理方法和表面质量标准,然后关注真正需要的平滑度。在当今严峻的经济形势下,在每一个表面处理操作中都要确立一个明确的目标,并在达到目标后立即停止,这是值得的。
在过去,如果一个零件仅仅是出于美观或外观的原因需要进行光泽处理,那么在图纸规格中声明“光洁度达到高光泽”是很常见的。这为“高光泽”究竟意味着什么留下了猜测的空间。这是一个主观的术语,而今天需要客观性。符合个人理想的表面处理不再具有商业实用性或盈利性。对于化妆品的表面处理,制造商必须特别要求表面光洁度的参数和值。
有了便携式表面检测仪,就可以在制造时对零件进行测量和分析(如图)。如有必要,可削减加工操作,直到表面符合表面加工规范。通过这种方式,制造商可以避免对零件进行过度加工,而在大批量生产中,这样做可以节省大量成本。因此,在完成时严格遵守规范是值得的。如果图纸要求20 μin,那就不要加工到10 μin。在连续、长期和大批量生产中,一个超细、光滑的表面可能不值得花费时间、材料和工时来实现它。
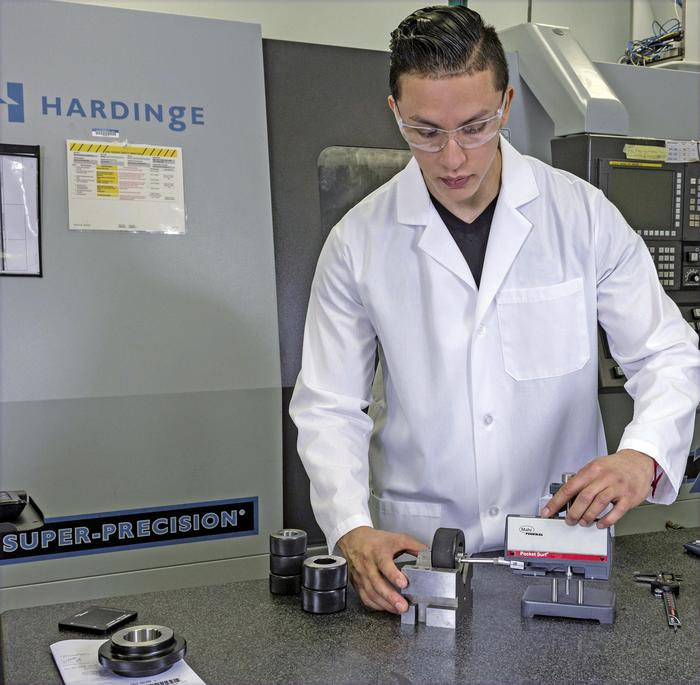
在制造时验证表面光洁度可以消除操作员的影响
有时,超光滑的表面可能会阻碍后续的加工步骤,为了涂上防护涂层或油漆,必须“粗糙化”。在机械上,它可能会造成运动部件的滑动。在这种情况下,过度加工的成本就得再加上返工的成本。过度加工也会影响产量。为了获得更好的表面,修整轮子或磨刀的时间会更长。将粗砂磨轮变为细砂磨轮会减慢工作台进给速度或刀架速度。折衷方案是减少金属去除和降低生产率。
通常,拥有指定的表面处理可以消除二次操作。如果拉削、镗孔、铰孔或钻孔能起作用,就不再需要磨刀。此外,如果铣削或表面磨削就足够了,就不需要研磨。不管什么工件,如果在高产量的情况下加工或研磨一个工件,即使是额外的、不必要的5 min,那也意味着要花费大量的制造成本。
当然,如果机械师在尺寸公差为0.010 in或以上且非临界间隙的情况下工作,则目视检查过程可能是足够的。然而,高精度的金属加工操作需要对表面粗糙度进行更加敏感和定量的评估,而对此该项技术是现成的。今天的仪器允许在制造过程中对表面光洁度进行高度精确的测量。对于正在进行精细加工的制造商来说,投资于示踪式表面测量仪器是更为有效的方法,这种仪器可以更准确地描绘出他们将要生产的表面纹理的不规则性。
此外,配合件表面的所有不平整都会对磨损和性能产生重要和长期的影响。有些影响比其他的更隐蔽。例如,当轴在轴承中旋转时,或活塞杆在往复运动时,“粗糙”的表面会在一段时间内造成不必要的磨损,轴充当铰刀,活塞杆充当拉刀。但是,除非能够量化需求并对其进行度量,否则无法保证产品能够满足其设计需求和性能。
评论
加载更多