多年来,许多公司一直在使用聚合物3D打印来制造固定装置和夹具,为采用常规制造方法的生产制造起到一定的辅助作用。有些公司甚至使用聚合物3D打印的部件制作软模。然而,金属增材制造工艺的出现让公司可以制造注塑的硬模。
为什么使用增材制造工艺制造硬模?答案很简单:增材制造工艺实现了设计自由,这也是我们使用增材制造工艺制造复杂而盘错交叉的各类零部件的原因所在。对于硬模也是如此。设计自由可以用于制造采用机加工等常规方式成本过高或无法实现的制造特征。不过,更大的好处是在模具内形成了保形冷却通道,帮助管理生产过程中的热循环。
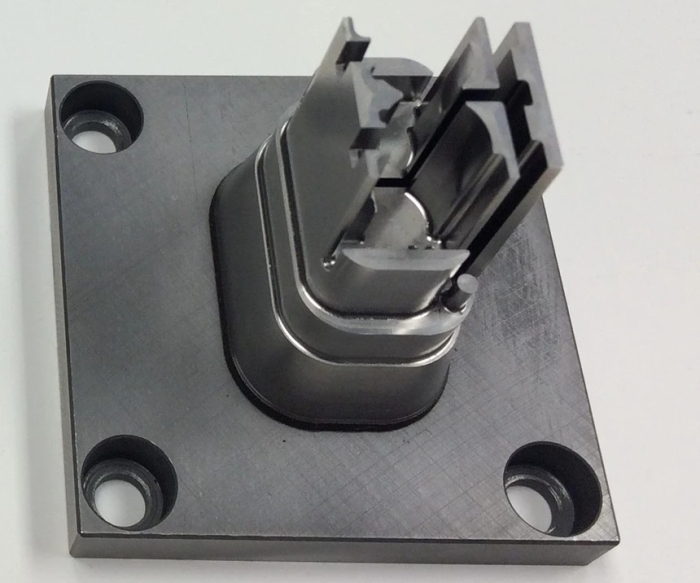
如果只是使用增材制造工艺是无法获得如此光滑的精加工表面的,还需要进行加工
限制注塑过程速度的因素之一是模具温度。根据我此前读过的研究资料描述,如果可以加快模具的散热速度,循环时间则可以缩短10%、20%甚至40%。
更重要的是,更精确地控制模具温度,并利用其与注射到模具中的塑料熔体温度的相互作用,可以减少缺陷,改善性能,提高零部件性能。谁都希望通过提高工艺,获得更高质量的零部件。
然而,这个过程并不简单。此前我曾讨论过使用增材制造工艺会遇到的表面粗糙度问题。这些问题在这里同样存在。水平和垂直表面的表面光洁度差异将导致保形冷却通道不光滑,甚至会因为设计和定向原因而出现内部支撑结构。当今的增材制造工艺无法达到我们所需要的接近于硬加工的表面光洁度。激光粉体熔化成型(PBF)在极少数情况下可实现这一目标。但是,无论热能来自何处,我们都无法进行定向能量沉积(DED)。
幸运的是,我此前提到的一个混合制造系统,可以解决这个问题。实际上,Matsuura和Sodick公司推出的混合粉体熔化成型(PBF)和减材系统可以在一台机器上制造出成品模具。现在DMG MORI也正在向这一领域进军。
几年前,我与Matsuura实验室的团队有过一面之缘。当时他们向我展示的项目令人印象深刻。如图所示,仅通过粉体熔化成型(PBF)是无法获得如此光滑且干净的表面的。必须进行加工,而这正是这几家公司研发的混合制造系统的优势所在。首先,是将材料一层层堆叠在部件(在本例中为模具)表面,然后对表面进行机加工和精加工,添加几层材料,再进行加工。重复这个过程,直至模具制造完成。这项技术让人眼前一亮。此外,我还没遇到一位机械加工专家,可以告诉我如何加工弯曲的内部共形冷却通道。
同时,如果您是一家专业的硬模制造商,我建议您考虑这种增材制造的混合使用方法。到目前为止,这项技术适用的模具范围还相对较小,但是这种情况会有所改变。各大公司正在积极研究大型粉体熔化成型(PBF)系统。随着混合机器的进一步发展,人们很快将开始通过定向能量沉积(DED)制造目标模具和模型,充分利用该项技术带来的成本和交付时间优势。
评论
加载更多