Deutsche Edelstahlwerke Specialty Steel(DEW)公司总部位于德国克雷菲尔德。每天,公司的测试工程师都会通过拉伸和缺口冲击试验来确认公司生产的钢材是否合格。标准测试样品长55 mm,方形横截面为10×10 mm,从机械加工的角度来看,这样一个标准样品不足为奇。但是在生产过程中,每位操作人员每月需要手动装载约2500个样品。
DEW的材料测试团队协调员Christian Richter解释道:“完成工作设置后,Doosan DNM 400 VMC只需15 min左右便可完成一套三个样品的生产操作。加工每个部件时,需分别对两种加工操作(操作10和操作20)进行设置。虽然手动将部件从操作10切换至操作20并完成固定只需约1 min的时间,对于操作人员而言,这也是一种时间的浪费。”
因此,Richter先生对各种自动化解决方案进行了研究,希望可以提高灵活性和机器利用率。引入新技术的目的不是减少员工人数,而是让员工将更多的时间和精力投入到其他增值任务中。但是有趣的是,公司选择的解决方案并不涉及机器人。
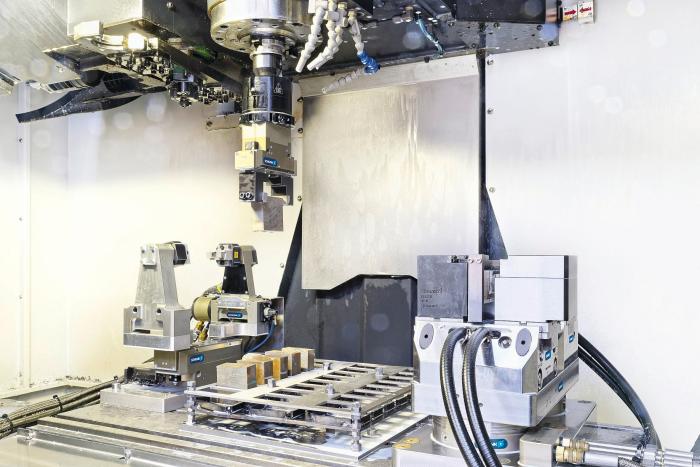
图1 Schunk公司的精益自动化解决方案采用主轴行程、刀架、压缩空气或冷却剂供应、ATC和工件(不是机器人)等机床要素实现部件的自动化处理
让机器自动装载
在初步考虑让机器人来管理机器后,车间咨询了工件夹具设备制造商Schunk的代表,对方提出了精益自动化解决方案。该解决方案经过设计,可以在脱离机器人的前提下实现机床自动化操作,不仅简单、快速,而且经济。这个解决方案的基本原理很简单:不需要购买外围设备,完全利用机器中已有的要素自动处理部件。此类要素包括主轴行程、刀架、压缩空气或冷却剂供应、ATC和工件。
将必要的附加处理和清洁模块通过刀柄接口固定在刀架上,然后放入ATC中,在需要时调出。Schunk公司的精益自动化解决方案的夹持器采用冷却剂或压缩空气作为动力,冷却剂或压缩空气通过连接模块的轴接口内部供应。
“我们喜欢这个内部机器装载的方案。这个方案不仅经济,而且安全、节省空间。所有操作都是在机器里面发生;关上门,机器自己会工作,”Richter先生说道。
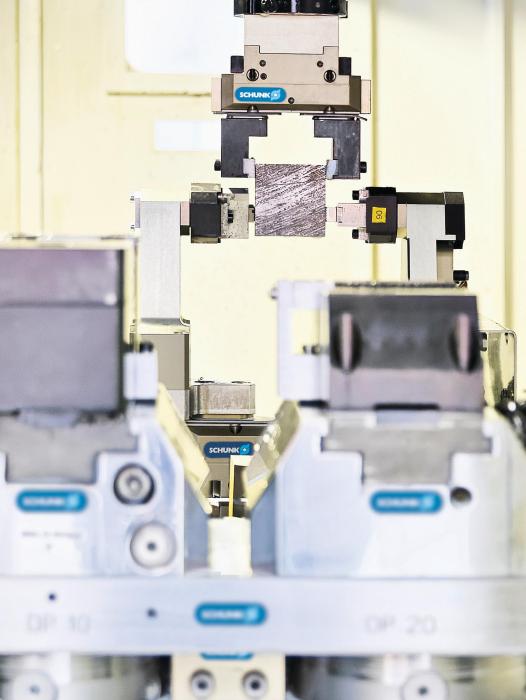
图2 装载时,Schunk通用夹具通过传统刀架固定在机床主轴上,然后移动到工件库,同时拾取一个水刀切割毛坯,然后将其放入夹紧块中
工作原理
进行操作10的装载工作时,将带有GSW-B接口的Schunk夹具通过传统刀架固定在机床主轴上,然后移动到工件库,同时移出一个水射流切割坯料,将其放入Schunk Tandem KSP-LH plus 160- IN气动双钳口夹紧块中。然后,ATC将抓手换成切刀,开始加工。
加工结束后,VMC更换夹具,将加工后的零部件移至工作站,进行180°旋转。进行操作20时,夹具将零部件放到第二个双钳口夹紧块中,再将新的毛坯放入操作10的夹紧块中,继续加工。夹紧块可以对钳口位置进行感应监控,确保自动化安全。
操作10和操作20包括两个后续的加工操作,将坯料切成三个样品。最后,在操作20结束时,三个样品被分开,然后一起打包,再被夹具取走送至工件库的指定位置。
为了防止零部件装载期间,施加在机器主轴上的作用力过大,主轴夹具采用Schunk SW-B轴接口和补偿单元,以适应不准确的工件公差以及6个自由度内的定位错误。在每个加工循环开始之前,使用清洁设备清洁夹紧装置、部件分拣台和坯料上的碎屑和污垢。
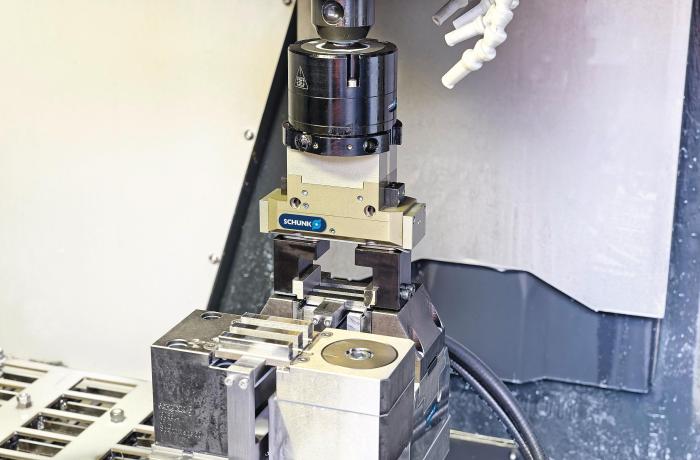
图3 在完成最后一个加工操作后,三个样品被分开,然后一起打包,再被夹具取走送至工件库指定的位置
提高生产力和灵活性
“通过夹固系统、分拣装置以及ATC和工件库使机器实现自动化运行,最大程度提高工作台的效率和可用空间,”Richter先生说道,“过去,每个测试样品都是单独制造的,而现在我们可以同时加工三个样品,减少了非生产处理和安装时间。
尽管采用了集成自动化解决方案,但为了尽可能保持最大的灵活性,一次完成零部件生产作业,Richter先生还购买了Schunk Vero-S NSL plus 200夹紧站。这种模块化的快速更换托盘系统允许在机器外部精确完成工件、夹紧装置或其他设备的重置操作。
对于Richter先生和他的团队而言,这种精益自动化解决方案的最大好处是,操作人员可在无人值守的情况下执行其他任务,增加了灵活性和附加值。此外,他们还认识到该系统不需要任何特殊的机器人技术知识。“只要操作人员会编程即可运行机器;我们不需要任何特殊的自动化知识,便可对过程进行管理并在必要时作出灵活反应。”
此外,精益自动化系统可以从一台机床转移到另一台机床。“总的来说,这套系统就等于一个夹具、一个固定系统和一个刀架,”Richter先生说道。
公司接下来的工作重心是,在员工完全熟悉新系统并且一切工作顺利进行后,进入自动化的下一阶段,在无人值守模式下生产多个样品。
评论
加载更多