汽车行业正在经历一个转型时期,新型零部件以及新型制造方法对于生产规划人员也变得越来越重要。电动汽车需求的增加也同样保证了生产能力的提高。但由此也产生以下问题:如何才能优化生产,尽可能高效地规划生产。
电动汽车的一个核心部件当然是电动机本身。对于电动机的主要组成部分,也就是采用叠片组结构的转子轴,埃马克已研发出一套在速度和质量方面几乎达到绝对领先的高效加工工艺。
在过去一段时间里,一些项目通常采用车削代替磨削来生产有叠片组的转子轴。由于倒立式车床和磨床同属于埃马克公司的产品范围,因此除了考虑客户偏好之外,还会根据客户对工件表面质量的要求来决定是采用磨削技术还是采用车削技术。车削可针对叠片组进行干加工。如果对于表面光洁度的要求低于Rz6.3μm,那么传统的纵向车削就需要相应较长的加工时间。正是出于这个原因,埃马克开始尝试使用无纹路车削技术。早在很久之前,埃马克就已经开始应用并持续不断地努力创新和发展无纹路车削技术,因此非常了解这项技术的潜力所在,特别是在与高性能立式车床相结合后,这项技术更能发挥出巨大的潜力。
无纹路表面和快速进给率 进行无纹路车削时,倾斜的刀刃在旋转的工件旁回转。在无纹路车削过程中,刀刃切入点沿着刀刃不断移动。这样,切削使用的就是整个刀刃,从而可以达到更长的刀具使用寿命。这项工艺技术的优势在于节拍时间非常短(比磨削或纵向车削快10倍)。
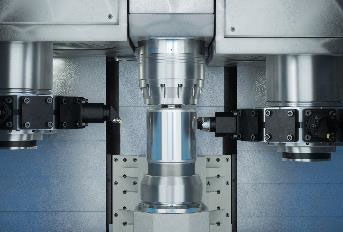
无纹路车削的优势在于节拍时间非常短(比磨削或纵向车削快10倍)
无纹路车削能为用户提供多项优势:
· 在硬加工过程中生产出无纹路表面
· 每转的进给更高,因此可以实现极短的节拍时间
· 车削时使用整个刀刃,从而能够延长刀具使用寿命
现在要做的就是要将这些优势转移到转子轴加工或叠片组加工中,而事实上,埃马克也成功地做到了这一点。实践也已证明,使用这种加工技术,可以在最高进给达到1mm/转时,实现Rz<6.3μm的表面质量。由于叠片组是分层结构,因此,取决于叠片厚度和进给值,切屑会在旋转1到1.5转之后断裂。这样就可以避免形成切屑团;而在进给速度较低的传统车削加工中,长条状的切屑不断 卷绕便会形成切屑团。
降低转子轴加工成本
毫无疑问,无纹路车削也能降低单件成本。更短的节拍时间可以降低机床成本,更长的刀具使用寿命(因为整个刀刃上各个区域的切入时间都相应缩短)也可以降低刀具成本和换刀成本。然而,无纹路车削是非常复杂的制造工艺,需要相应的机座和必要的专业技术知识。埃马克提供的整体解决方案正是在此方面独具优势。
转子轴的4轴加工
VT系列的倒立式4轴轴类件车床加工转子轴的理想选择。在加工最大长度630mm、最大直径200mm的工件时,该机床能充分发挥其质量优势:
· 同步:加工过程采用四轴,并同时从两面进行。机床为此配备两个刀塔,每个刀塔各有十二个刀位,其中 11个刀位装备车刀或动力刀具,剩余一个刀位则装备工件机械手。
· 自动化:工件机械手可保证同时为机床上下料。在一个机械手将新毛坯件放入装夹位置的同时,另一个机械手会将成品件运送到工件输送带上。为此,在VT系列机床两侧都配备有循环运行的工件存储器,毛坯件和成品件均可存储在工件存储器中。通过TrackMotion工件输送系统可将多台VT机床简单、经济地相互连接在一起。
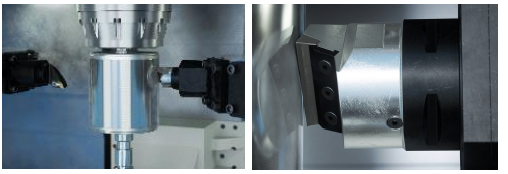
进行无纹路车削时,倾斜的刀刃在旋转的工件旁回转。在无纹路车削过程中,刀刃切入点沿着刀刃不断移动。这样,切削使用的就是整个刀刃,从而可以达到更长的刀具使用寿命
在VT机床上进行无纹路车削
得益于埃马克多年的丰富经验,无纹路车削技术已在批量生产中使用。所使用的机床亦是如此,埃马克运用其通过多项应用和试验中获得的经验和成果,根据这项技术的要求对机床进行最完美的配置。例如,VT系列的旋转刀塔已经根据无纹路车削的特殊要求进行调整。这不仅适用于机械部件,还适用于回转轴参数设置及控制旋转轴的设置。从软件方面来看,在倒立式轴类件车床上使用无纹路车削技术完全没有任何问题。利用控制系统中的相应程序,机床的调整设置工作与传统车削加工中一样容易。
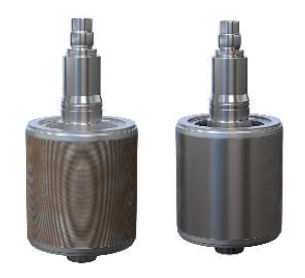
无纹路车削是加工采用叠片组结构的转子轴的理想选择(如图所示:叠片组加工前和加工后)
评论
加载更多