德勤 (Deloitte) 公司的一项最新研究调查结果表明,从2032年起,在乘用车市场中,将首次出现替代动力汽车的新增销售量超过纯内燃机汽车的情况。不难想象,这样一种发展趋势对于汽车行业会有什么样的影响:内燃机组件的增值份额持续下降,而“电动”驱动组件的份额却急剧上升,其中就包括多种旋转对称的部件,机械制造专业公司埃马克目前正在研发的就是专为这类部件量身定制的生产解决方案。最近,埃马克为一个供应商集团研发出一套全自动、高效的完整解决方案,专用于转子轴制造以及用于转子铁芯叠片的高精度外径车削。利用这套灵活的系统,客户可以实现多种加工组合。客户方负责人对于这套系统所能达到的部件品质和可重复性非常满意。
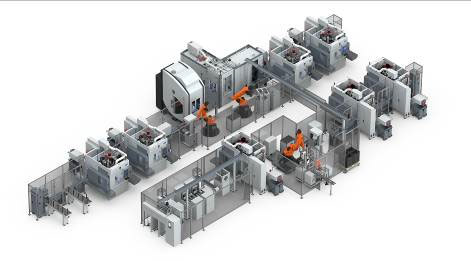
通过十二道主要工序以及其他不同的辅助工序完整加工转子轴。各台机床与工位的自动化和连接通过机械手、桁架机械手系统以及由埃马克自行研发的 TrackMotion 系统实现
不断增长的电动机产量需求向生产规划者提出重大挑战:在许多应用领域内,他们必须建立起新的整体化解决方案,从而更快、更高效地生产电动机驱动轴等部件。去年年底,埃马克向一家专门生产电动汽车零部件的德国供应商提供了一套全新的解决方案。这个令人印象深刻的最新案例,为我们展示了这类解决方案的具体内容。双方如何达成合作?“这名客户当时正在寻找一种智能自动化解决方案和物联网集成的高度灵活的系统,以实现与转子轴相关的各种加工组合。在这类问题方面,这名客户在过去多年中一直非常信赖埃马克的技术,因为我们不仅能提供出自一手的解决方案,而且从整个埃马克集团范围来看,我们掌握了几乎所有加工技术”,埃马克大客户经理Andreas Bucher解释说。
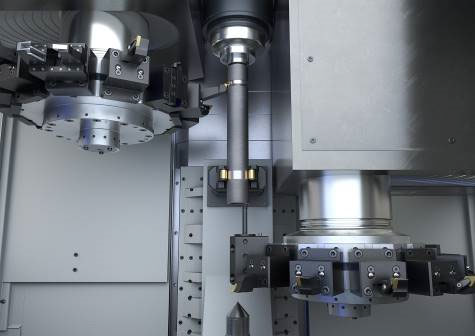
OP 10 / 20——在两台埃马VTC 200上进行粗车削——这是一种可缩短主加工时间的4轴式轴类件加工解决方案
双方的合作在很早期的阶段就已经开始:客户甚至提前与埃马克讨论工件的设计图纸,以简化后续的机械制造工作,并实现精益和可靠的生产工艺。整条生产线的研发工作在密切的交流与合作中顺利完成。EMAG Systems 公司的 Michael Ihring对此评价说:“在埃马克,我们始终遵循‘面向客户’的原则。一位经验丰富的员工会与客户讨论整套生产解决方案的各种要求,其中甚至包括比如并非由埃马克提供的机床(本案例中的OP 30)。换句话说,我们负责整套生产解决方案并定义其技术规格。这种方法的优势非常明显:各部门之间的沟通和确认工作量明显减少、供货时间缩短,同时也可以实现一套更加经济和高效的整体解决方案。”
十二道工序便可达成目标
最终,我们为客户呈现出一套令人印象深刻的转子轴加工系统——包括十二道主要工序以及其他不同的辅助工序。各台机床与工位的自动化和连接通过机械手、桁架机械手系统以及由埃马克自行研发的TrackMotion系统实现。整个工艺流程具体如下:
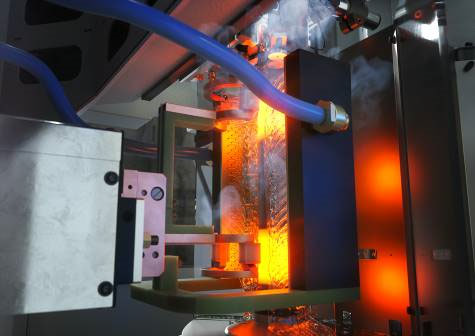
OP 40——在 EMAG eldec 的 MIND L 1000 上进行轴承座的感应加热
· 操作人员将毛坯件放到缓冲输送带上之后,在两台埃马克VTC 200机床上开始粗车削——这是一种可缩短主加工时间 (OP 10/20)的4轴式轴类件加工解决方案。接着执行吹扫和测量过程。测量设备向车床发送反馈,并由车床自动进行补偿。
· 完成内齿磨削(OP 30,成型)之后,便会转移到EMAG eldec的MIND L 1000上执行OP 40工序:转子轴的轴承座的感应加热和淬火。
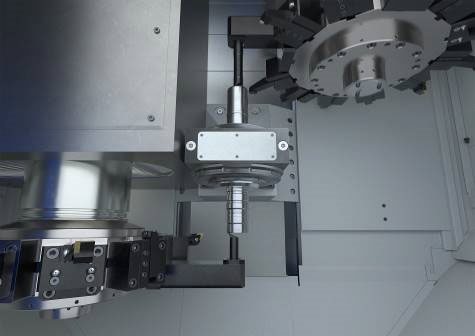
OP 50——在配备中心驱动的 VTC 200 上完成转子轴的内车削
· 分别在两台埃马克VTC 200 CD(OP 50,内车)或两台埃马克VTC 200(OP 60,钻孔加工)机床上进行的后续工序也非常重要。这两道工序在两台机床上同时进行,以提高产量。接着对转子轴再次进行吹扫、测量,并在合格工件上执行DMC打标操作。
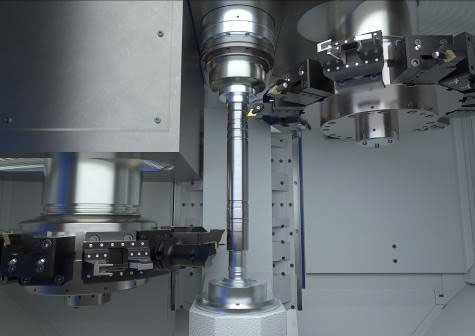
OP 60——在 VTC 200 上使用动力刀具完成精车削和钻孔。
· 工序OP 70包含两个装配过程,在此会通过热套装配一个套筒和一个盖板。
· 最后的车削工序 (OP80) 在VTC 200机床上进行,此时可对转子轴的轴环和轴座进行精加工。吹扫、测量和堆垛三道工序标志生产线的结束。
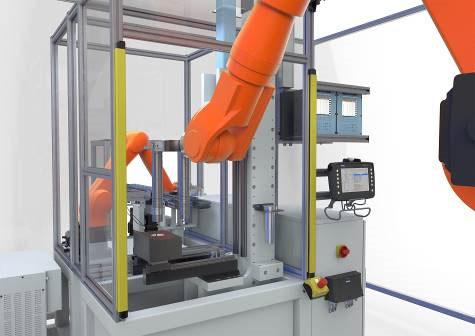
OP 70——装配套筒和盖板
“我们的规划得以证实,”Michael Ihring 总结说,“所有工艺都非常稳定,得到的部件品质因此也非常高。同时,客户也能从灵活的生产单元解决方案获益,这种解决方案可随着产量要求的提高而随时扩展。这种灵活性体现在包含工件输送系统在内的每一个细节中。此外,各种不同的智能模块的更换策略可确保只有极短的停机时间。”
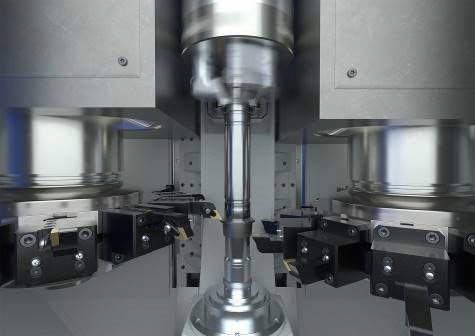
OP 80——精车削转子轴的轴环和轴座
无纹路切削保证完美的叠片组表面
埃马克为这名客户提供的“电动汽车整体项目”远不止如此,因为机床制造商埃马克还额外利用VTC 200机床设计出一种用于转子铁芯叠片高精度外径车削的解决方案。这里使用所谓的无纹路切削工艺:刀具在工件上作滚轧运动,也就是说倾斜的CBN刀刃会在旋转的工件上方运动。刀刃切入点持续不断地移动。整个过程比传统硬车削快五到六倍,比磨削快三倍。并且同时可以实现卓越的无纹路表面质量。换句话说:以前必须采用磨削加工的表面,未来可以使用无纹路切削技术完成。对于围绕轴的叠片组来说,这正是最理想的解决方案。
为不断增长的电动汽车市场带来优势
“总的来说,无论是加工转子轴还是叠片铁芯的外径车削,客户都可以从具有高度稳定性和工艺可靠性、经过完美协调的整体系统中受益。这些都是我们希望在未来几年内为不断增长的电动汽车市场所带来的巨大优势。”Andreas Bucher说,“电动机制造行业的需求明显越来越大。同时,我们的技术已在此行业的多个应用领域内得到广泛应用。”
评论
加载更多