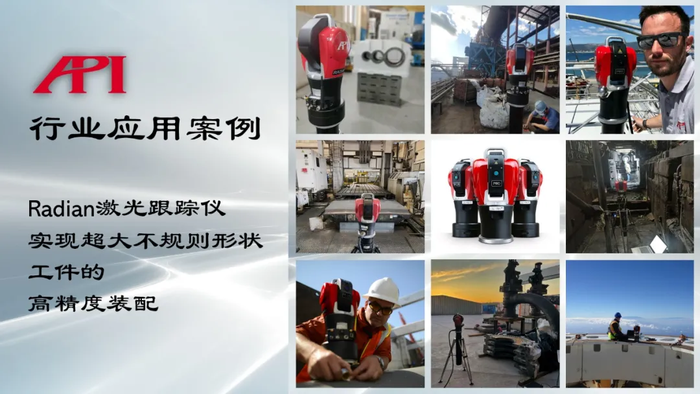
关于超大型工件的高精度装配
在某些领域的工业生产中,涉及到使用超大型工件。超大型工件往往具备体积庞大、以及重量巨大的特点,且基于生产对于质量的要求,工件的制造和装配公差都有着严格的限定,故而工件整体的装配精度较难通过使用传统的方式得以保障。
经生产实践总结,使用激光跟踪仪对这类体积重量超大、且装配公差要求严苛的工件进行精度检测,是效率最高、效果最佳、且经济效益最为突出的方案。
激光跟踪仪(Laser Tracker),可用于大尺寸高精度的3D测量检测,测量半径往往可以达到数十米,综合测量精度在微米级别(μm,1/1000mm),且使用较为灵活,只需将仪器架设在待测工件旁合适的位置,使用内置棱镜的靶球碰触待测位置,跟踪仪会射出激光至靶球中心并锁定、跟踪、读取碰触位置点的空间坐标并记录在软件,通过这些采集到的点的空间坐标,即可构建各类线、面、体,从而对相应的形位公差进行精准分析,达到测量检测的效果。
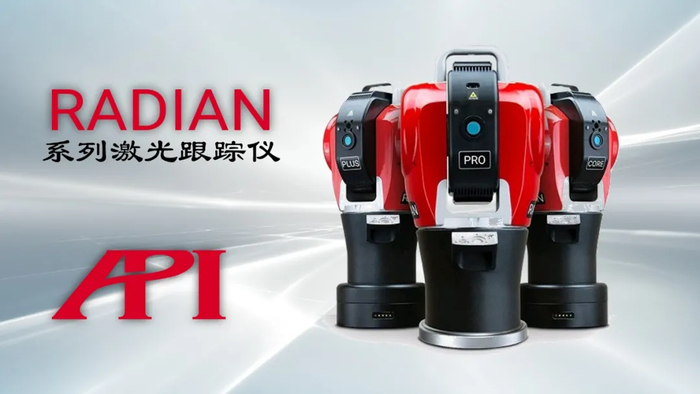
图1:API品牌Radian系列激光跟踪仪(RadianPro/Plus/Core)
值得关注的要点
虽然激光跟踪仪精度高、覆盖范围广,但是在针对一些数十米及百米以上超大型工件的装配作业时,仍然有一些要点值得关注和总结,以便更好地发挥激光跟踪仪的特性,进一步提升装配精度和质量:
1.精度标准的统一
虽在激光跟踪仪的有效工作范围内,都可以实现和达到装配精度标准,但近端测量精度高于远端测量精度这一现象,是基于激光跟踪仪本身工作原理及特性客观存在的。
这种现象的产生,是因为激光跟踪仪测量时存在角度误差,同样角度的偏差,在远端造成的测量不确定度范围会远大于其近端的测量不确定度。
如图2所示,激光跟踪仪在测量近端平面P1和远端平面P2时,其激光在平面上的投射点理论上应分别为圆心A和圆心B;但由于激光跟踪仪角度误差α的存在,激光就有可能被投射在圆C和圆F面积范围内的任意一点;而圆C和圆F的面积范围内,即分别为跟踪仪测量近端平面P1和远端平面P2时的测量不确定度;通过右下角正面视图观察,圆F的面积要远大于圆C的面积,即:远端的测量不确定范围要远大于近端的测量不确定范围。
生产中,工件整体的装配精度要求是统一的;那么当使用激光跟踪仪单站装配一个超大工件时,即便通常情况下其近、远端精度都可以满足需求,但处于不同位置段的装配点仍然会处于不同的精度标准之中;如果需要精益求精、进一步提升装配精度、使工件各段处于同一精度标准下,就需要对单一跟踪仪远端较大的测量误差范围加以控制。
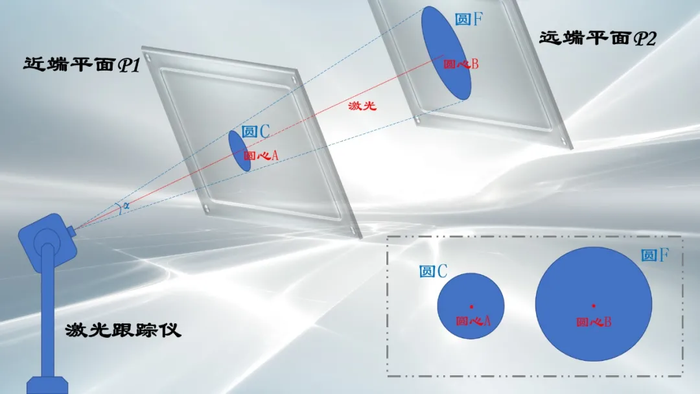
图2:激光跟踪仪角度误差示意图
2.站点间的关系
测量超出激光跟踪仪测量范围的工件、或是测量工件遮挡面时,往往需要将激光跟踪仪移动到另一个位置,来获得足够的测量覆盖范围。即:实施“转站”作业。
如图3,转站时,需在两站都可观测到的位置设置“转站点”(通常为4个点),使用激光跟踪仪在两个站点分别测量这些“转站点”,然后通过软件的“最佳拟合”功能,将两站带入同一坐标系进行测量。
使用“转站点”+“最佳拟合”功能来进行转站测量,优势在于较为快捷,可以通过转1-2站,就实现对常规尺寸工件测量范围的全覆盖,并同时满足测量精度要求。
但当装配超大型工件时,如果使用最佳拟合转站的方式,每新增一个站点,就会将前方各站点的误差进行累积,即:设置的站位越多,测量误差越大,并继续造成各装配点精度标准的不统一。
可见,超大型工件的装配对于跟踪仪站点之间的相互关系的误差,也有着严苛的要求。
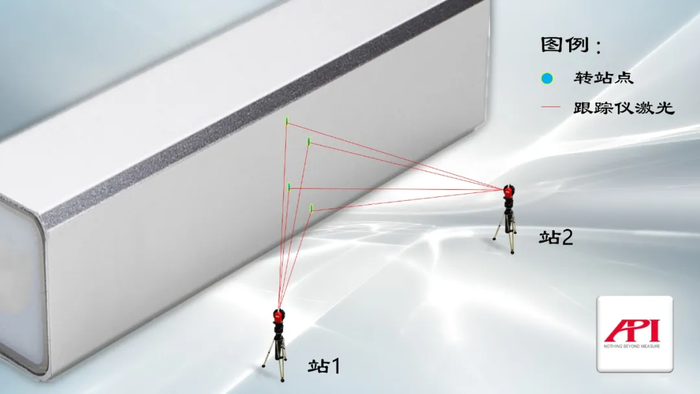
图3:激光跟踪仪转站示意图
API超大型工件高精度装配解决方案
经总结与实践,以下文介绍的案例为参考,可以使用激光跟踪仪进行平差测量的方法来满足广大用户对于超大型工件装配极致高精度表现的要求。
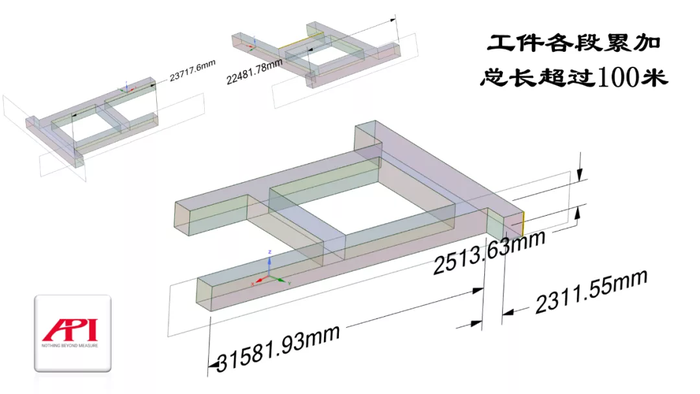
图4:标的超大型工件结构及尺寸示意图
测量案例:累加总长超过100米的超大不规则形状工件的高精度装配。
工件特征&测量要求:如图4所示,待测标的工件各段累加总长超过100米;要求装配整体最大允许误差为0.3mm。
仪器的选用:根据本次测量的要求和工件特征,选用了APIRadian Pro激光跟踪仪作为执行作业的设备。RadianPro激光跟踪仪集成有IFM干涉激光,其测距精度达到1/10000mm级别,高于激光跟踪仪综合精度(1/1000mm级别)。
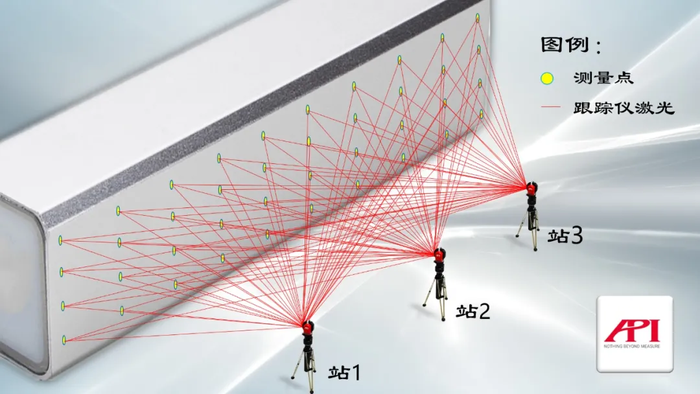
图5:跟踪仪平差测量站位设置及数据采集示意图
测量步骤&要点
根据工件的特征,在最合适的位置,设置多个激光跟踪仪站点,形成对工件测量范围的优质覆盖。设置站点时,需考虑本文上述的激光跟踪仪的近端精度优势特征、以及IFM跟踪仪的测距优势特征,尽可能地在最佳测量范围内正面工件设定跟踪仪站位(见图5示意)。
如图5示意,跟踪仪在每一站,都分别对可视范围内设置的所有待测点进行测量采数,形成数据网络,并综合记录于软件,用于最终的平差及分析。
待数据采集完毕后,在软件中可进行设置,将所有数据捆绑进行平差分析,并以优势站位的跟踪仪采集的数据为较高权重,在统一精度标准及统一坐标系下得到最终的整体测量结果。
▼以下视频全程记录了本案中超大工件测量装配的过程:
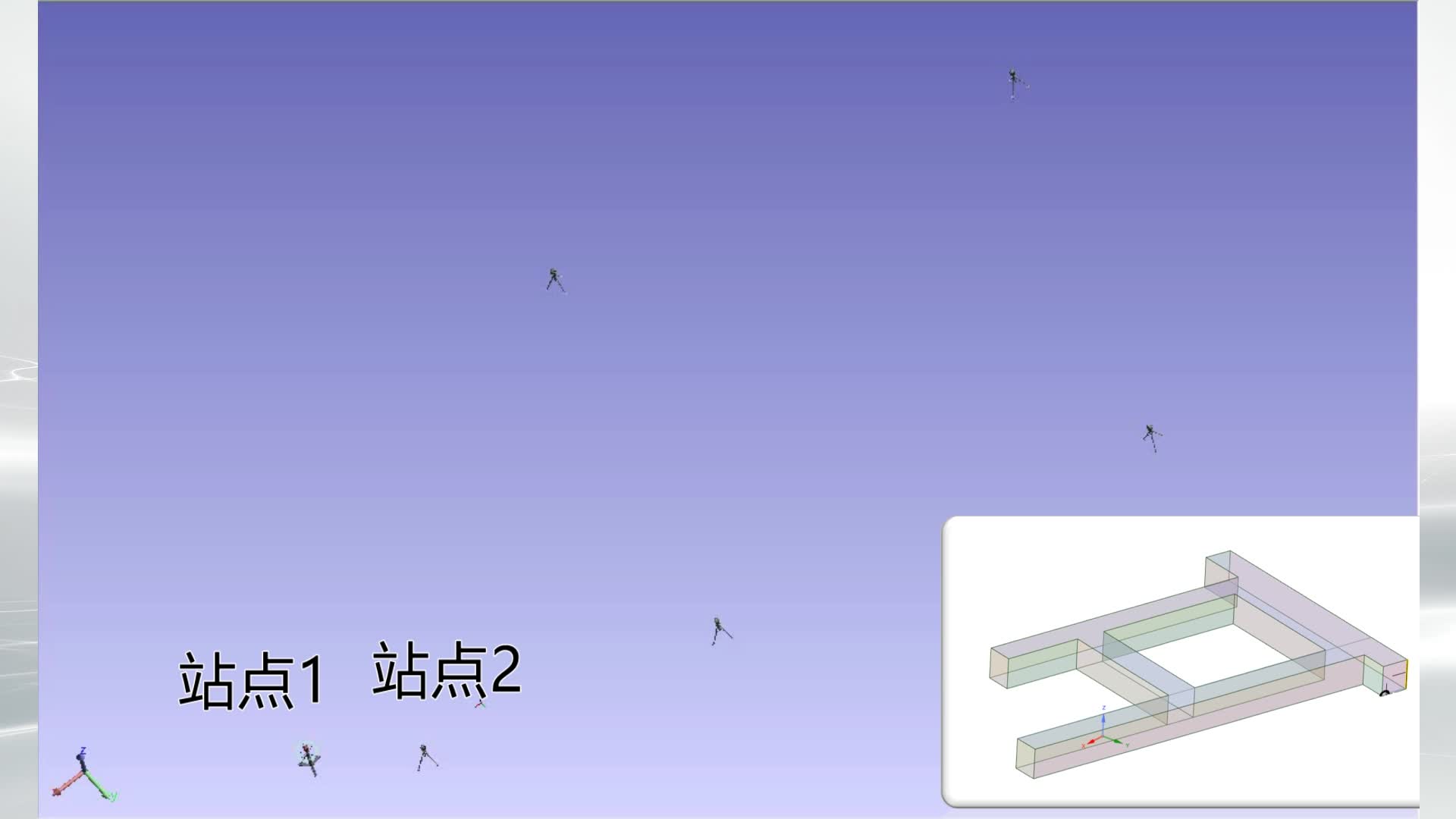
实际测量验证:总长超过100米的超大不规则形状工件,整体装配精度被控制在0.2mm以内,充分满足公差要求。
评论
加载更多