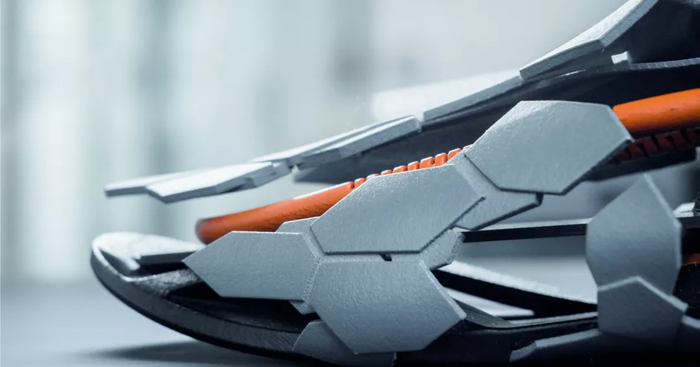
采用传统制造工艺时,技术人员需针对每位患者的情况手动调整模型。其中涉及繁杂的步骤,大幅增加了生产成本和生产时间。
增材制造技术能够令患者和制造商大大受益。该制造工艺以患者的个体扫描数据为基础,因此3D 打印的假肢和矫形器能够根据佩戴者的身体结构和需求定制,达到最优效果。
矫形器和假肢有利于提高佩戴者的活动能力。但每位佩戴者的身体结构、使用习惯和治疗需求各不相同。EOS 3D打印解决方案将快速制造工艺与佩戴舒适度优化方案成功结合。
应用案例
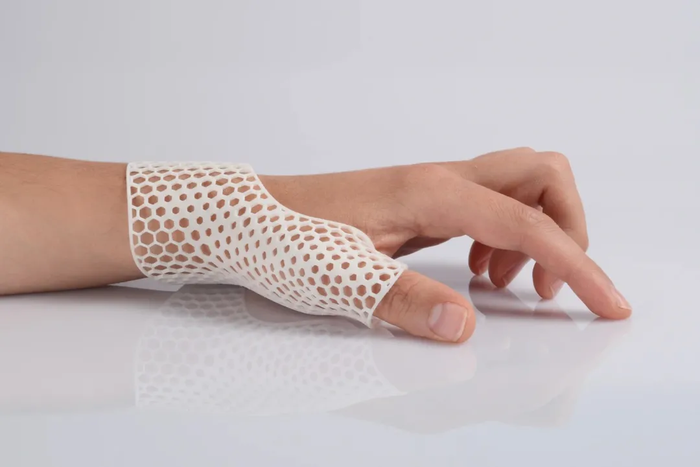
02
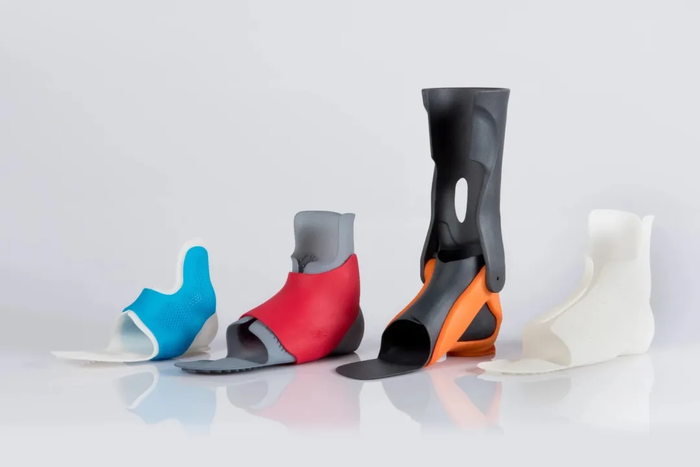
03
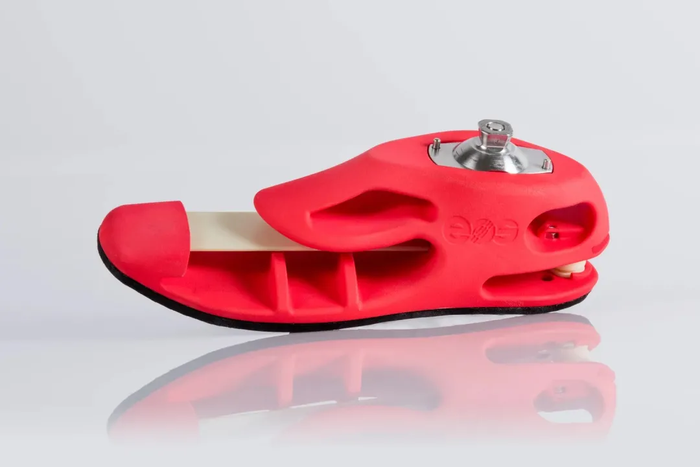
04
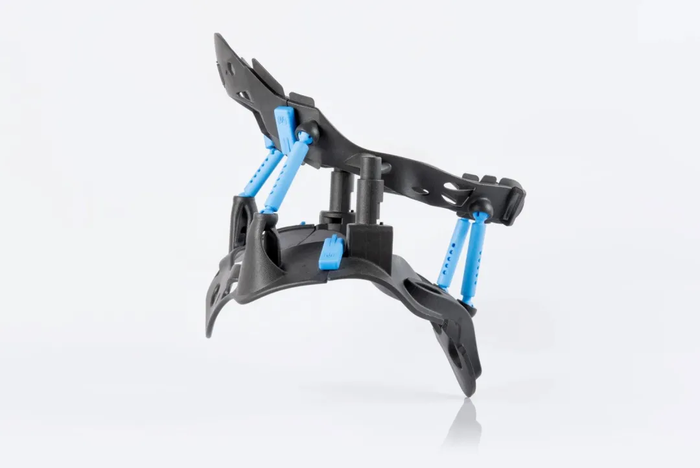
01 手部矫形器 02 足部矫形器 03 假肢 04 颈椎矫形器
在设计和功能方面拥有近乎无限的定制潜力
佩戴舒适:虽然结构复杂,但十分轻便且稳定
可持续性:可重复使用剩余材料,从而减少材料损耗
可快速执行任何必要调整,例如,针对仍在发育中的儿童进行调整
功能集成使设计更具弹性和透气性,提高佩戴舒适度
从扫描到成品的整个过程全部采用数字化工艺,加快上市速度
Mecuris 创新案例:按需制造义足
Mecuris 为患者、医生、整形外科工作室以及医疗器材供应商提供了一个数字平台。根据这些人员和机构提交的数据,Mecuris 使用 EOS 系统进行 3D 打印义足的合约制造。
定制的义足可帮助患者自如行走。借助增材制造工艺,Mecuris 大幅缩短了交期,极大地提高了佩戴舒适度,并实现了定制化设计。
残奥会自行车手 - 丹尼斯·施耐德
Mecuris 的EOS 3D打印工艺使理想假肢成为可能
自 2015 年起,奥托博克一直利用 EOS的3D打印 技术来制造和销售矫形器。作为世界领先的 3D 打印服务提供商,该公司与许多整形外科技术人员保持着密切合作,代其制造各种产品。
在这种成功合作模式的推动下,奥托博克制造的矫形器在重量、透气性、设计和定制潜力等方面都实现了巨大优化。
“借助增材制造技术,我们可以根据每位患者的需求,为其提供定制矫形器。此外,透气设计也让佩戴舒适度得到极大提升。”
卢卡斯·艾克曼
患者护理和个性化定制部门主管 | 奥托博克
评论
加载更多