对于Spühl公司而言,毫不夸张地说,一切都以“弹簧”为中心,并且130多年以来一直如此。当时,该公司为其第一批用于生产各种家具弹簧和床垫弹簧的弹簧机申请了专利。从2014年开始,公司按照“精益制造”的理念来生产此类设备。
“Just-in-time 准时化生产”不仅仅是一个网红词组,更是一个规划完善的生产流程。瑞士制造需要最高水平的生产效率。EROWA的FMC制造技术是这个高效生产流程的重要组成部分。
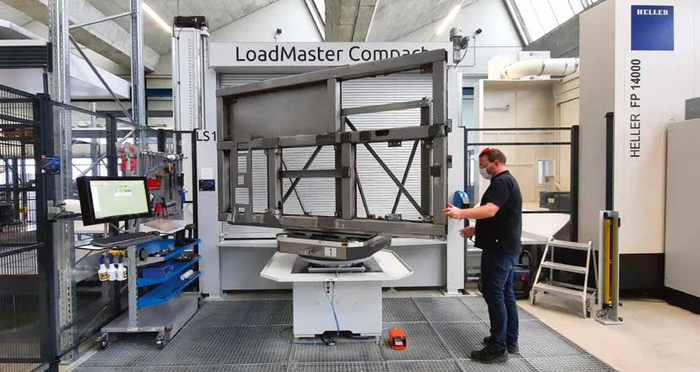
Spühl公司主要为其总部--Legget & Platt集团服务,该集团的业务遍及全球。该公司生产的设备仅有一小部分在自由市场上销售。该公司在德语地区以Spühl Production Services品牌提供通用机械制造服务。一方面,这样可以确保生产设备的能力得到最佳利用;另一方面,参与自由市场的交易使公司的交货速度和成本优化能够保持良好的状态。
顶级的设备
“当今世界,如果想一直保持竞争力,现代化的设施和不断改进完善的生产计划和流程是必不可少的,”生产经理Patrick Jung说,该公司生产车间的场景正是对这一点的有力证明。“标准化的组件和流程为我们提供了规划安全性。通过这种生产方式,我们奠定了高品质的基础,并保障了交货时效和竞争力。”
我们产品涵盖的尺寸范围和制造工艺非常广泛,这一特点令人印象深刻。这确保我们能够在自己的生产领域,以最佳的方式处理涉及不同要求的订单。为了在瑞士这样的“高价岛屿”生存下去,实现生产设备自动化是必不可少的关键步骤,这使我们能够以最小的工作量,灵活地从一个订单转换到另一个订单,无论工件批量的大小。配置的HELLER和EROWA的新设备,使我们的竞争力得到了进一步的提升。
一流的员工
当被问及为整个Spühl团队提供的支持时,Patrick Jung解释道:“我们将员工视为最重要的资产。定期为他们提供基础和高级培训有助于员工的个人发展。反过来,公司也得到满意度和内动力更高的团队。目前,我们已有200名员工,并且正在培养新生力量:我们的31名实习生将是公司未来成功的基础。

数字孪生
一次性零件加工面临的最大挑战是如何以最小的代价来实现自动化。Spühl通过对整个生产流程的数字化模拟,在这方面取得了成功。数字化模拟所需的部分条件是通过使用EROWA工装系统来创建的。装有工件毛坯的夹具安装在精密的托盘系统上,因此,它们在工作站和机床上可随时被重复定位。通过对数据模型,机床,工具,夹具和组件的绝对标准化,进一步满足了数字孪生所需的条件。所有这些加工流程中的已知数值为生产过程的模拟最大程度接近实际加工创造了条件,从而能以最少的试运转次数来实现一次性零件的生产。这大大节省了生产的预调时间!
自动化已经成为传统
Spühl公司很早以前就意识到自动化是未来发展的趋势,在那时就购置了HELLER加工中心并集成自动化。当时市场上的机床都没有配置自动装卸设备,Spühl公司选择了SCHULER线性存储系统。1988年,公司购置了第1台具有两层线性存储的设备。到了2014年,就已经发展成9台不同型号的装载设备。在整个使用过程中,设备的高品质和无故障运转令人印象深刻。2019年,Spühl公司购买了第一台HELLER HF 3500机床并配置了一台EROWA机器人Dynamic 150L。由于Spühl公司当时采取的是一种新的制造战略,因此这一投资的选择过程是具有绝对开放性的。“之前的自动化单元:一台HELLER 5轴加工中心配置一台EROWA机器人的使用体验令我们非常满意。当时,EROWA已经收购了SCHULER的‘LoadMaster’产品线,因此,我们又购置了最新的HELLER FP 140000机床并扩展配置了1台EROWA LoadMaster Compact。”Patrick Jung说。
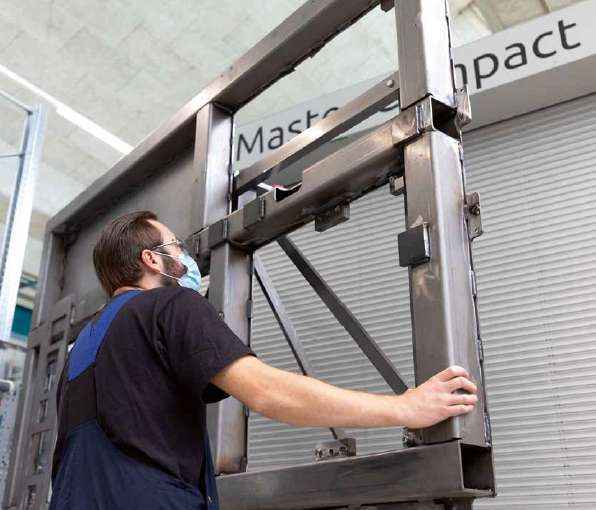
LoadMaster Compact扩展方案
为了不断优化改进,Spühl公司定期对其现有加工设备进行关键性指标评估,并在必要时更新换代。在这种情况下,本次更新涉及到的是一台加工行程范围为6米的平面铣床(该公司为数不多的未进行任何自动化的机床之一)。
由于项目的关键是在不新购大型设备的前提下,可满足日常大部分工件加工的尺寸需求,Spühl公司首先对所有工件订单的加工尺寸和加工要求进行了分析。
由于公司经常需要进行大批量加工,所以托板化工件的可加工区域最宽处尺寸设定为3米。这样一来,可加工工件的尺寸范围将覆盖公司80%的工件订单,这也意味着绝大部分订单均可在公司内部完成,有助于企业的经济发展。新采购的5轴加工中心配置了自动装卸设备,经评估可取代2台旧机床。无论如何,加工单元的自动化和生产效率的提高说明了该案例的成功。
满足高标准的要求
新的加工单元需要面临的挑战不少。尺寸大到2.9米的工件必须进行托板化,存储系统须可容纳至少10个托盘,且还须有增加更多存储位的扩展余地。重达3吨的工件必须能在可移动预调台上进行预设置。5轴加工中心必须通过过程控制系统与现有的ERP连接起来,以提供清晰的状态概览。
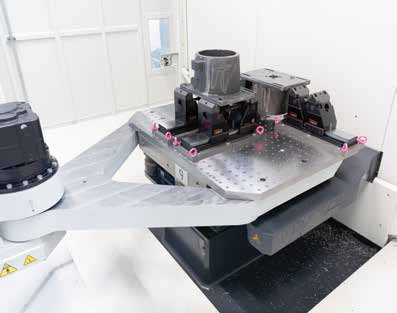
灵活的解决方案
归功于自动化单元的模块化设计,托板化工件的可加工区域可以非常简单轻松地适应我们的加工需求。此外,EROWA过程控制系统确保我们能够对复杂的订单处理系统保持全面的了解。该控制系统操作简单直观。由于链接到ERP系统,操作人员可随时了解当前订单的进度,以及下一个需要处理的订单信息。
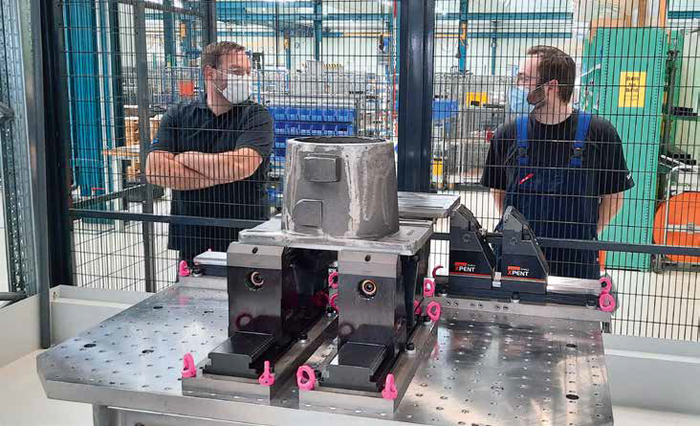
成果斐然
建立如此大规模的生产基地需要一定的时间。以Spühl公司的车间为例,大约用时两个月。安装工作进行得非常顺利,每个独立的组件都是标准化的,且须按照“即插即用”的概念相互连接。HELLER和EROWA之间的合作进展顺利。“机床操作人员从一开始就很好地掌握了操作要领,”Patrick Jung说。他们在EROWA自动化和JMS 4.0过程控制系统方面的经验可以按1:1应用于新工厂。得益于HELLER的承诺“如果您希望在一台机床上完成尽可能多的生产任务,并且希望您的生产从现在到未来一直是安全可靠的,购买一台HELLER F系列5轴加工中心是您正确的决定”以及使用EROWA自动化获得的成功经验, Spühl公司的自动化单元能够无故障地应对目前的所有加工任务。操作人员对易于操作的设备和易于管理的软件非常满意。生产管理部门很高兴能够通过控制系统对有效生产时间进行最合理的计划安排。
现在,正如故事的标题所言,Spühl公司的发展正在:“迈向成功的未来”!
评论
加载更多