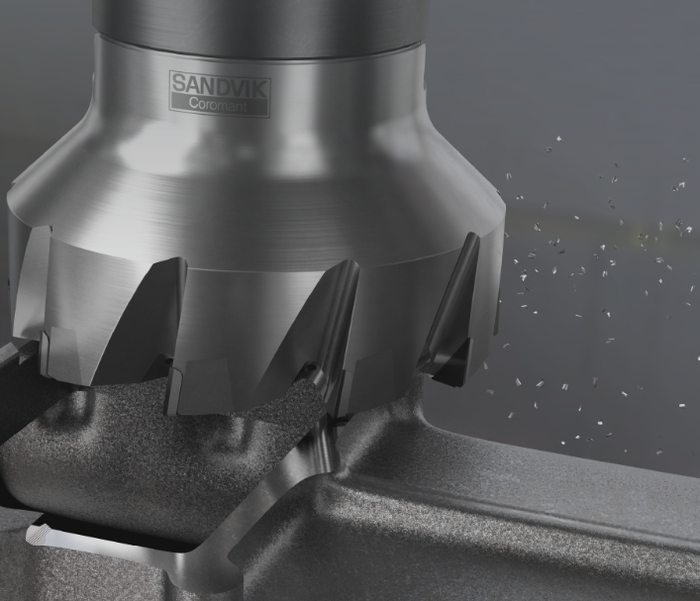
汽车业原始设备制造商 (OEM) 越来越多参与电池生产,地理上而言越来越靠近车辆组装工厂。根据麦肯锡咨询公司 (McKinsey & Company) 的报告,电池技术、耐用性及性能将是OEM赖以脱颖而出的重要不同点。在本文中,山特维克可乐满的汽车铝合金业务全球经理Fernando Oliveira阐释了其新款面铣刀具M5F90将对OEM能否领先同行发挥至关重要的作用。
未来,电池系统将继续演进,相应地就要求有新的突破和新的造型。对于OEM而言,这包括基于更复杂的设计生产出接近电池部件外型的零件。要加工出这些设计,需要高效的轻型切削刀具,以此把对机床刀具的影响力降到最低并确保零件不变形。
OEM的角色也在发生变化 — 他们将更多参与到电池生产中,而麦肯锡咨询公司认为这种变化归因于“OEM的后向一体化,即:从组件和模块的生产向上游的电池生产转化。”与此同时,关于打造更轻、更高效、里程更长之电动车辆 (EV) 的比赛也在进行中,旨在使电动车辆充满一次电之后可以行驶的里程最大化。
此外,制造商们根据最高品质标准且以高生产率生产这些更复杂的零件。那么制造商们如何能在保持单个零件较低成本的同时实现这一点呢?答案是借助更高效的切削刀具,这些刀具的可达性高,最大程度轻量化,以此实现快速换刀。
减少二氧化碳排放
制造商们正在向“轻量化”转变,包括建造重量更轻的轿车和卡车,以此实现更出色的燃油效率。
根据麦肯锡咨询公司另一项研究,轻量化措施有助于将二氧化碳排放量降低至一定程度 (大约每千克减少二氧化碳排放0.08克)。如果某OEM能够将车辆重量减少100千克,则每100公里可减少二氧化碳排放大约8.5克。
作为重量最轻的金属材料之一,铝合金是轻量化方案的解决之道。铝的重量比铁轻几乎三倍,虽然强度不如铁,但是强度依然很好,并且耐腐蚀。事实已经证明,从工程设计角度而言,如果把传统铸铁部件搭配铝合金材质,可将发动机组的整体重量减轻40–55%之多。
此外铝金属还有一个优势:重复利用度极高,可以熔化后再次使用,而丝毫无损机械特性。事实是,所有已经生产出来的铝合金材料,至今有大约75%仍在使用,证明了该材质在OEM可持续发展策略中的实用性。
更小的加工表面
一辆欧洲乘用车的动力系统通常包含约80千克铝合金材料,这使得发动机、变速箱、悬架部件、壳体等零件成为倍受关注的轻量化措施首选。此外铝还可用于电池本身:根据中欧能源合作平台 (EU-China Energy Cooperation Platform,ECECP) 建议,将铝空气 (AI-air) 电池作为锂离子 (Li-ion) 电池的替代品,因为低廉、轻型、强效等诸多优点。
这里,让我们聚焦铝合金电池架。此类部件通常加工面较小,更多的是螺纹、孔洞及其他加工特征。另有一个重要考量是用于卡车的电池架,尤其是需要在施工区域作业的较大型卡车,其所用电池架,长度可长至两米。
电池架所需的切削刀具应用,包括铣削和轮辋等类型。即使电池架结构很大,也并不需要大刀具,相反,电池架的加工面更小,螺纹和孔洞等特性增多。因此,它们需要的是能够满足质量和误差要求的方肩铣和面铣刀具或是铰刀。
消除振动
对于电池架的加工,山特维克可乐满建议使用其M5系列汽车铝合金面铣专用铣刀,包括不会产生毛刺、划痕或崩刃现象的M5F90面铣刀。该刀具专用于加工薄壁铝件,为此,其配备了直径为25–80毫米或0.98-3.15英寸的较小刀体。M5F90还包含焊接的多晶金刚石 (PCD) 刀尖,因此无需调整,就能保证极低跳动量。这促成了高进给,同时消除了刀具振动。
M5F90用于加工铝合金电池架的案例。这对于全新概念设计并生产的面铣刀具而言,电池架零件是理想的应用领域,M5F90刀具仅通过一道工序加工,就可将铝合金铸造毛坯件的表面粗精加工完成,而不会产生任何毛刺。
其尺寸大约为980 x 600 x 130毫米 (mm)。总计使用了48把刀具,包括整体硬质合金钻头、整体硬质合金立铣刀、高速钢 (HSS) 丝锥、焊接PCD铰刀,以及M5F90铣刀。铝件加工在一台5轴加工中心上进行,配备HSK 63高速刀柄。
M5F90的焊接PCD刀片具备两个方向的阶梯式切削刃 — 径向和纵向。这个特性降低了功率消耗,因此可以使用更高切削参数运行,从而消除了毛刺且减少了加工过程中的振动。尤其是减少振动这个优势有助于实现可靠性能,延长刀具寿命,即增加可加工零件的数量。
电池架加工应用,还展示了M5F90的一个关键优势。特别是,其仅需一道工序就可搞定粗、精两种加工,因此节省了时间。以铝合金电池架的加工为例,该零件加工用时为20.3分钟。凭借增强的刀具性能,OEM可更多参与电池系统的生产,同时使自身在一众竞争对手中脱颖而出。
文章来源:山特维克可乐满
图片来源:山特维克可乐满
转载平台:微信公众号
责任编辑:朱晓裔
部门领导审核:李峥
评论 0
没有更多评论了