数据驱动型制造业并不具备压倒性优势,也没有众人想象中那么复杂。对于制造厂商而言,可以通过简单的反馈回路将测量仪器与计算机数控系统相连,保证部件的质量,同时车间工作人员的需求量也降至最低。
由印度机床制造商Marshall Machines Ltd.的美国分公司Marshall Automation America Inc.生产的SmartCorrect专门设计用于确保技术型设备操作人员和检验人员稀缺行业的无缺陷高产量车削操作(如图)。
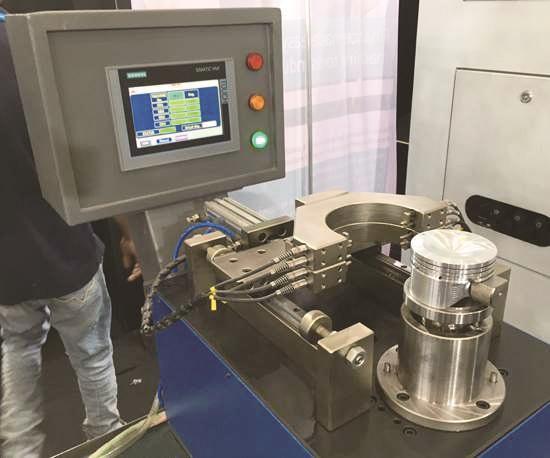
SmartCorrect测量工作站采用旋转的转台固定装置和数字探针检查轮廓精度,找到发动机活塞圆周上找到最大椭圆点,确定该点与活塞销中心线所形成的角度是否超出88°~92°范围。此外,测量工作站还可用于部件测量,自动计算后刀具磨损补偿量输入到车床的计算机数控系统中,防止在生产过程中被测特征超出规定范围,系统由机器人负责装卸,进一步减少了人员需求
每个测量工作站都是针对特定的部件和部件设计的,配备了Heidenhain和Marposs等公司的定制固定装置和数字测量工具。各种移动元件都可以操纵部件和探针,将原本手动的测量工作变为自动化模式。除了节省设备和可能发生的质控人工成本外,这种物理自动化还消除了错误的风险,例如使用错误的或未经校准的测量工具,或工具的使用方法错误。
此外,数据驱动自动化还解决了导致部件缺陷的另外两个常见错误。一个是检查数据分析。刀具磨损越厉害,测得的特征会逐渐放大,最终达到规定的公差极限。常规做法是测量值跟踪和定期调整工具磨损补偿,确保符合部件规范。计算错误或补偿校正执行时间不当也会造成部件、工具报废,甚至是机器损坏、额外的成本和工期延误。
SmartCorrect可以自动计算补偿量,但是,必须是在系统处理250~500个部件后,因为系统需要通过这个过程来了解变量的程度。系统需对大量数据进行分析后才能计算控制的上下限,即表明测量部件特征趋向上限或下限的阈值。在测量时,必须超出阈值,触发补偿校正功能。制程标准值等于三次最新测量结果的平均值。当平均值介于控制限和公差限之间时,系统重新计算补偿值并发送给计算机数控系统,进行自动升级。后续部件将参考相同公差,不再需要手动输入或监管。
导致部件缺陷的第三个错误是将错误的数据输入到计算机数控系统中。测量工作站与车床的计算机数控系统(或根据用户需要,连接到两条车床的计算机数控系统),解决了这个问题。在购买Marshall公司生产的设备时,测量工作站通过硬线与计算机数控系统相连。补偿升级和计算通过公司的CLAP(闭路自动校正生产)技术执行。而对于其他机床,公司一般会推荐Caron Engineering 公司开发的Autocomp软件。Autocomp软件是一款基于Windows的系统,通过以太网电缆连接,除了需要人工输入控制限外,其他功能与CLAP相同。
所有测量和校正数据均保存到文件中,以供未来分析。测量结果也可以输入到Marshall的SmartInsert系统中,由系统计算刀具的磨损程度,确保仅刀具使用寿命到期时及时更换。Autocomp软件可用于优化连接到其他制造商设备的测量工作站的工具使用寿命。
SmartChek仅适用于公司自己生产的机器,用于监控车床主轴和两轴组件的运行状况。通过系统生成的每日数字健康报告确定振动、电机负载或其他参数方面的任何偏差。
总体而言,该自动测量工作站证明数据驱动型制造不需要额外的工作便可实现,不会导致数据过载,不要求投资扩大储存和分析能力,而且也适用于机床应用。
评论
加载更多