随着航空航天刀具产品的不断升级,各类航空铝合金、钛合金等难加工材料的广泛使用,大大增加了航空航天刀具产品的制造难度。许多设备或工艺无法解决的问题,可以通过选择三菱综合材料的航空航天刀具来解决。
行业人士都了解,超耐热合金加工中最大的难题就是切削过程中易产生大量切削热,并出现严重的加工硬化,从而导致孔加工刀具常常会出现崩刃和磨损量过大引起的刀具寿命短、加工不稳定等现象。如何做到保证孔加工高精度的同时,实现刀具的超长寿命成为了行业内重大攻克项目。
DSA系列钻头技术优势
三菱综合材料于2020年正式发售的DSA系列钻头,是专门为航空航天产业等超耐热合金零件孔加工研发的一款产品,其具有强韧的直线状切削刃,以及耐热合金专用刃口修磨、刃带设计,配合了TRI-Cooling冷却技术及最佳刀具材质。该产品能够使耐热合金孔加工中棘手的切屑不稳定、易崩刃、易加工硬化、刀具寿命短等问题得以最大限度解决,成为难加工材料加工的又一利器。
三菱综合材料的技术研发团队,历经三年时间,以及大量的模拟解析和反复的现场测试,最终破解了超耐热合金孔加工的难题。DSA系列钻头凭借四大要素,成功实现了高精度、长寿命等优势特点。
要素一:全新高韧性、高硬度PVD涂层硬质合金材质【DP9020】
通过不断调整硬质合金基体中碳化钨(WC)与钴(Co)含量及颗粒大小的配比,使基体维持高硬度的同时具备较高韧性,并配合耐高温PVD涂层,有效实现高耐破损性及高耐磨损性。
要素二:高强度的直线切削刃配合耐热合金专用的刃口修磨
兼具切削锋利性和耐崩刃性的刃口修磨可大大抑制加工超耐热合金中发生的崩刃现象。直线切削刃刃型强韧,且便于重磨再次使用。
要素三:保证孔精度的同时抑制切削热产生的刃带设计
采用适用于超耐热合金加工的较窄单刃带,可减少接触面积,降低切削热,抑制加工硬化层的产生,降低加工难度。
要素四:采用TRI-Cooling冷却技术
确保钻头刚性不会降低,使冷却液流量最大限度加大,润滑性、冷却性和切屑处理性提高。
加工案例
目前,作为性能优越的钛合金加工用钻头,DSA钻头已被成功应用于航空航天零部件高效加工中。
以下是涡轮盘两种典型材料Inconel718和RENE41的实际案例。从刃口磨损图片可以看出,专为超耐热合金设计的DSA钻头,其超群的耐磨损性,实现了难切削材料的高品质孔加工中稳定的长寿命。
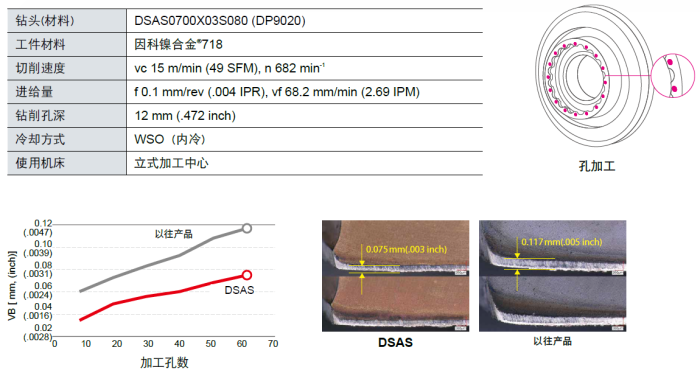
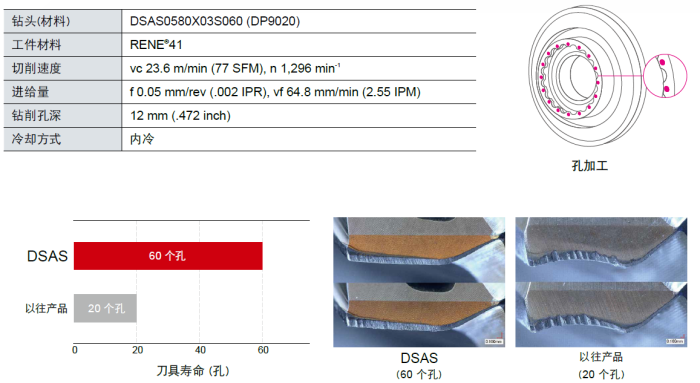
图1 端面孔加工示意图
1.加工内容:端面孔加工
工件材料为Inconel718,在与原刀具加工相同件数时,DSA钻头切削刃磨损更小,孔质量更高,加工稳定,寿命延长。
工件材料为RENE41,这种材料加工难度更大,粘且切削热高,DSA钻头可有效抑制切削刃的损伤,刀具寿命大幅提高。
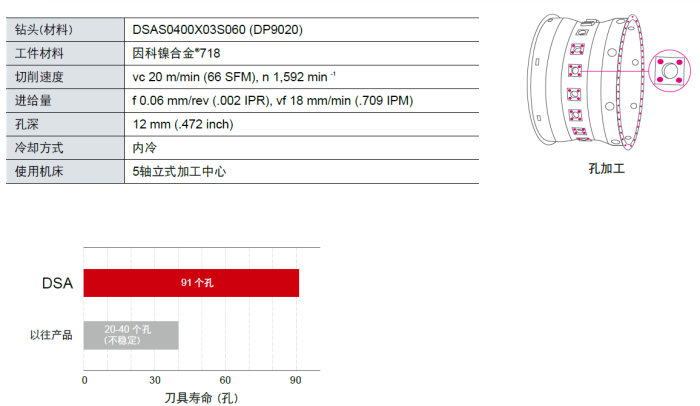
图2 发动机燃烧室外周及端面孔加工示意图
2. 加工内容:发动机燃烧室外周及端面孔加工
工件材料为Inconel718,发动机燃烧室外壳上孔加工数量较多,DSA钻头可大幅延长刀具寿命,减少换刀次数,有效地提高了加工效率,并且更是成功解决了困扰客户由于切削刃损伤引起的加工不稳定导致损毁工件的问题。
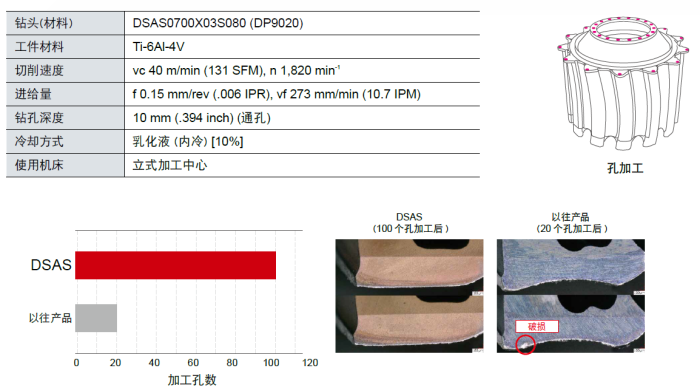
图3 发动机风扇盘端面孔加工示意图
3.发动机风扇盘端面孔加工
工件材料为钛合金Ti-6Al-4V,由于DSA钻头的独特刃型及TRI-Cooling内冷设计,使得冷却液充分、切削阻力低并有效抑制粘结引起的切削刃破损,孔品质提高,寿命达到原某日系品牌的5倍。
当然,超耐热合金不仅应用于航空航天领域,随着汽车行业的发展,涡轮增压器、废气含氧量传感器等零部件中均大量使用镍基合金、耐热不锈钢等难切削材料。
未来,三菱全新DSA钻头定能为用户带来更大价值。作为生产制造的专家,三菱综合材料也将继续全力以赴地协助每一位用户,满足他们的差异化需求,助力其高效稳定生产。
评论
加载更多