不同于汽车零件高效的批量加工模式,加工超大、超重型的能源类零件,在很多人的印象中,还是需要专机单件打磨的“慢工细活”。但随着当前能源行业的快速发展,高需求量以及日趋激烈的行业竞争,对此类零部件的加工效率提出了更严苛的要求。
如何实现高精度要求的、超大型能源类零部件的高效批量加工?本文着重对欧洲大型风电铸件商,也是风电行业的全球知名企业——西班牙SAKANA集团的探索之路进行阐述,相信能给各位读者带来一些启示。
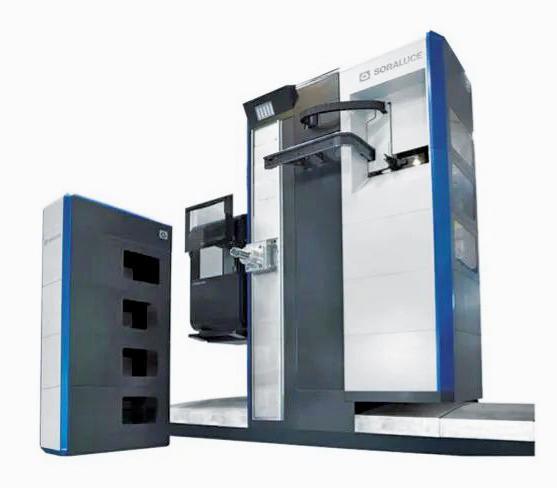
图1 FXR-12000-W多用途落地镗铣加工中心
SAKANA集团位于西班牙北部的拉昆特萨,专注于为大型制造业提供全面服务,包括铸造工艺、机加工、检测和表面处理工艺等。大型铸件的生产加工是SAKANA集团突出的优势,其铸件年产量位居欧洲第一。SAKANA集团旗下的Lakber公司成立于2008年,主要负责集团大型零部件的加工。十余年的发展已使其成为了全球风电铸件加工领域的领先企业,产品出口德国、丹麦和巴西等诸多国家,其开发的风电部件原型,如风机轮毂和框架等,得到了西门子、通用电气、GAMESA和阿尔斯通等风电行业巨头的认证。
风机轮毂和框架属于风机的核心部件,不仅尺寸、重量大,而且结构复杂、精密,Lakber公司能够做到高效批量生产主要依靠两方面的优势:第一是完全自主的加工工艺,不仅是工艺技术,Lakber的夹具、检测和激光测量系统均为自主研发和生产,进一步把控产品品质;第二是要归功于其高效率的加工设备,在这其中,5台索拉露斯(Soraluce,达诺巴特集团旗下镗铣品牌)FR和FX落地铣床和镗床可以说是绝对主力。这些机床的垂直行程达4800 mm,横向行程达1600 mm。
近期,由于能源、造船和其他领域对大型零部件加工需求的不断增加,以及公司扩大产品范围和应用领域的战略布局,Lakber公司再次与索拉露斯合作,引进了尺寸更大、应用更广泛的FXR-12000-W多用途落地镗铣加工中心,在其4000 mm×4000 mm的回转工作台上,垂直行程达6500 mm,可加工重达200 t的工件。
大工作范围满足多尺寸和多种类零部件的加工需求,而车削和铣削一体化的创新结构设计则帮助Lakber公司带来了高效率。例如,针对风机轮毂,FXR-12000-W通过可旋转、高承载力的工作台,能够一次装夹实现零件的铣削、车削和钻孔等操作。另外,量身定制的高扭矩车削加工头,可与主轴在任意角度定位,大幅提升了车削操作的灵活性。
另外,FXR-12000-W还集成了一系列索拉露斯自主研发的创新功能,确保了机床的稳定性与加工的高精度。
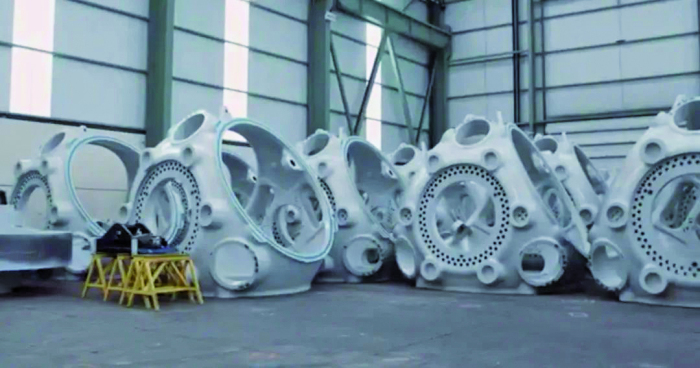
图2 风机轮毂
DAS系统是索拉露斯自主研发的动态主动稳定器,荣获了多个国际创新奖项,该系统集成了一系列实时控制震颤,并可监控加工过程的传感器,能够有效增加机床动态刚性,增强切削能力,高达300%,生产节拍时间可减少45%。
索拉露斯模块化镗杆可与其它附件头之间全自动互换,因此可配置不同直径和长度的镗杆;同时可配置加工所需的全部铣头。与传统方案相比,模块化镗杆保证了无论是使用镗杆还是其它铣头,机床立柱和主轴鼻端距离一致,使得五面加工可一次装夹完成,避免了工件在距机床较远的位置再次装夹加工。
滑枕平衡也是索拉露斯专利研发的一种动态补偿系统,可确保整个滑枕工作领域的几何精度,对确保铣削的加工稳定性至关重要。
索拉露斯自适应控制,可根据实时加工状况,自动调整原切削参数,包括主轴进给速度和切深等,从而实现无人值守的高效率加工,加工时间缩短多可达25%。
此外,FXR-12000-W还是一台工业4.0机床,其带有完整的云计算监控单元,使Lakber公司能够很轻松地将机床接入工厂网络,并实时监控加工情况,显示相关信息,如当前程序、使用的工具和主轴转速等。Lakber公司的总经理表示,索拉露斯FXR多用途镗铣床拥有卓越的多功能性、高性能和高生产率,且工件设置数量较少。
评论 0
正在获取数据......