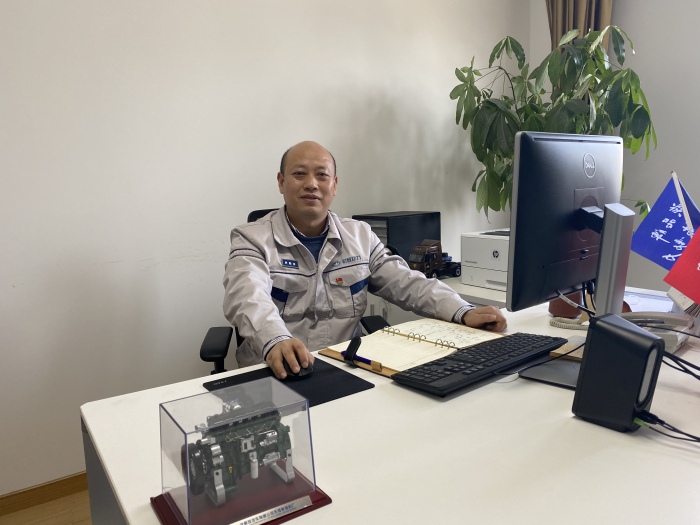
一汽解放发动机事业部规划发展部副部长史胜祥
加工中心在发动机批量生产过程中,相较于传统专用机床,优势较为明显。首先,加工中心充分发挥了主轴加速度1 g以上、主轴快进50 m/min以上的优势,大大节省了辅助时间;其次,大功率主轴、HSK100A刀柄,可适应CBN、陶瓷等超硬刀具的应用,降低了切削时间;第三,部分加工中心根据切削工况采用了双主轴,将切削效率提升了一倍,进一步凸显了加工中心高效切削的优势。同时,在质量保证上,设备的高精度和高可靠性是基础,高达±0.002 mm的定位精度、±0.001 mm的重复定位精度以及0.002 mm的转台回转精度,15 000 h以上的MTBF(平均无故障时间),辅以测头的自动测量补偿,保证了重要参数Cpk≥1.67,稳定持久保证了发动机的质量。
此外,加工中心最显著的一个特点是柔性强,可以适应不同产品包括四缸、六缸等共线生产、快速实现产品升级换代,满足用户个性化需求。
一汽解放发动机事业部(以下简称:发动机事业部)于2017年由中国一汽对集团商用车动力总成相关企业重组而成,旗下包括锡柴工厂、大柴工厂和大豪动力三大企业,分布在江苏、吉林、辽宁三个省份,主要产品为柴油机、天然气发动机、运动件、再制造和共轨系统。发动机事业部的下属工厂拥有多条国际一流的缸体、缸盖、曲轴和连杆等机加自动化生产线以及新品中试车间。加工中心作为发动机事业部生产过程中最常见的设备,尤其是加工缸体、缸盖箱体类零件,精切设备中加工中心的占比达到70%以上。设备以德国进口为主,其主要特点包括高精、高效、高柔性等。
从2003年起,发动机事业部开始大批量使用德国进口加工中心生产6DL奥威四气门发动机,这个阶段采用的是机械主轴,精切设备中加工中心占比约为60%,这种刚柔并济的生产线为奥威发动机的持续领航奠定了基础,此后建设的生产线加工中心使用比例进一步提升,电主轴、双主轴、MQL微量润滑、超硬刀具等新技术得到应用,有力保证了奥威发动机的高质量运行,也支撑了发动机事业部在国内柴油发动机行业前三甲的地位。
近年来,发动机事业部通过探索智能物流、智能生产保障以及智能生产调度三大系统建设,打造了一流的惠山工厂智能制造示范生产线。随着智能制造技术的发展,用户多品种、小批量的个性化需求越来越广泛,针对发动机行业,笔者建议国内外加工中心生产企业需要考虑以下三大因素:
第一,围绕生产线全加工中心柔性生产目标,推进新技术的应用。研发出适合发动机材料升级至GJV450以上的重载切削需要的更高刚性和可靠性的加工中心。同时进一步拓展新技术,通过加工中心U轴技术的应用,进一步满足发动机缸体缸孔止口、曲轴孔止推面、缸盖座圈锥面等车削应用需求,以及缸孔精镗刀具直径补偿、加工中心珩磨等技术的产业化。
第二,满足智能制造和大数据采集应用。建议应用数字传感技术,实时监控,采集机床主轴、刀具及功能部件的数据,实现设备的自适应加工,提升刀具寿命和切削效率,实现设备的预防预见性维护。
第三,围绕效率提升开发绿色制造新技术。通过不停机换刀、机床内自动检测等技术进一步减少辅助时间和停机时间,提升产线OEE;围绕MQL拓展,减少切削液使用,油雾烟雾收集进一步挖掘绿色制造新技术潜力。
诚然,以上这些需求和发展方向,尤其对于国内企业还有很长的一段路要走。
评论
加载更多