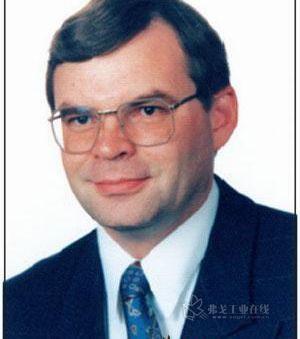
ThyssenKrupp金属切削集团Cross-Hüller公司执行副总裁Dr·Manfred Berger先生
在大批量生产制造过程中,敏捷制造系统所体现出的各方面的技术优越性和明显的经济效益已被人们所广泛认识和接受,将来的汽车制造业对敏捷制造系统的需求也将越来越迫切。
● ThyssenKrupp金属切削集团Cross-Hüller公司中国代表处
记者:现代汽车制造业需要各种柔性、自动化技术作为高效运行的支撑,在金属加工过程中尤其典型。作为ThyssenKrupp金属切削集团旗下著名的机床制造商,Cross-Hüller公司无疑是柔性和敏捷制造领域的技术和市场领先者。与刚性自动线、组合机床生产线相比,您认为柔性制造、敏捷制造系统的优势体现在哪些方面?
Dr·Manfred Berger:从产量角度看,敏捷制造系统的产量始于传统柔性制造系统的结束点(年产量>50000件),并有很大一部分和传统自动线(年产量>200000件)重合。如果使用CNC加工中心加工轻合金零件,对于敏捷制造系统而言,其投资平衡点大约为年产300000件(铸铁件约为年产 200000件)。这仅是从产量上进行分析,还未考虑敏捷系统对于不同品种工件的柔性乃至多品种共线生产的优点。
由于柔性自动线的局限性,众多欧洲生产商开始寻求更好的解决方案。复合单元(如可交换式铣头、可穿梭式动力头、三轴单元)的刚性连接及其串联式加工程序使整体设备的利用率(OEE)仅为65%~75%,而敏捷制造系统的并联加工方式使其在出故障时仅会暂时性地降低产量,而且很少会出现停产情况,设备利用率可达 80%~90%,在生产力上具有很大的优势。
由于以上的特点,使得敏捷制造系统具有加工中心的柔性和专机的高效性,而且在工艺编排上还可以进行最大程度的优化,特别是在产品更新换代时,再投资费用较低,而且可以最大限度地做到边改造边生产,使得生产线的投入产出比最大化。
记者:贵公司的敏捷制造系统在全球汽车工业中享有极高的声誉和广泛的应用,能否介绍一下在汽车行业的应用情况?
Dr·Manfred Berger:世界上最早使用带转接板的敏捷制造系统是在匈牙利的欧宝工厂、通用的巴西工厂以及HOLDEN工厂。通用在北美的工厂在1995年开始使用敏捷制造系统为V6、V8 和 V10生产大的缸体(铸铁和铝缸体),之后,法国雷诺和标致也引进了敏捷制造系统进行缸体和缸盖的加工。菲亚特在其巴西的FIASA工厂使用了双主轴的 CNC加工中心。福特在全世界范围内的工厂里有12条敏捷制造系统,其中最大的工厂于2001年安装了4条敏捷制造系统,共包含172台加工中心,生产能力达年产130万件缸盖。另外,通过引入最先进的技术,如干式加工等,敏捷制造系统也被用来进行转向节的大批量加工。传统的专机线现在大多数作为混合系统应用,即专机配合3~5个敏捷制造单元(每个加工单元作平行加工设计)。
敏捷制造的种种优势已经在汽车行业的大批量生产中体现出非常出色的应用价值,而汽车行业也是我们最主要的用户领域,大约占到我们业务总量的85%~95 %,今后,我们将继续开发面向汽车行业的制造系统,更好地满足用户需求。
记者:中国汽车制造业目前的设备升级和工艺改造对Cross-Hüller公司意味着巨大的商机,同时也面临着各方面的挑战,如操作人员的业务知识水平、复杂的工厂实际工作环境等因素都会影响到敏捷制造系统高效能的最大发挥,对此,贵公司如何培育和开拓将来的市场?
Dr·Manfred Berger:中国市场过去对于传统的制造设备的需求量较大,但在过去三年中,人们已经逐步认识到了敏捷制造系统的优势,一些主要的汽车制造商,如上海大众、上海通用、哈尔滨东安、奇瑞等都先后采用了我们的设备用于大规模生产并已从中获得了极大的经济效益。
对于敏捷制造系统,当今人们讨论的主要课题有两个——优秀的机床操作人员和空间利用率。熟练工以及相配套的完善的培训/人员考核制度是确保生产系统高生产力的必要条件,为此,Cross Hüller为用户方面的操作人员、编程人员以及电控/维修人员提供先进的互动多媒体结合现场操作的综合培训课程。由于高效的生产力不允许机床操作人员在错误中提高以适应机床,所以CrossHüller提供的培训课程从长远上保证了生产力。作为生产系统的提供者,我们能够清晰地了解客户在生产中可能遇到的问题并提供有效的解决方法。
记者:敏捷制造系统在实际生产线的布局和工艺设计中应该注意哪些问题?
Dr·Manfred Berger:在大多数的敏捷制造系统中,平行布置的机床由自动上下料装置连接,如王行 架机械手系统,其节拍时间约为36s(机床上下料、抓取、放下工件至自动传输装置)。王行架机械手或其他上料装置不应设置为在最大速度和加速度状态下工作,以便提高可靠性和系统整体设备利用率。在保证上料系统能力以及较高设备利用率的前提下,我们建议系统年产量选择在325000~400000件之间。
为获取敏捷系统适应不同品种的最高柔性,各工序可考虑多品种生产,如缸盖加工时考虑对将来品种加工的柔性,而非仅针对某个品种设计生产线,应将将来品种的加工也综合考虑进生产线工艺设计中。由此,在将来增加新品种时可在现有的机床上(带有转接板)进行生产,每个单元按照可放置最多数量的加工中心来设计,同时也可视需要为将来要添加的机床留出空工位,同时,生产线设计时,也可考虑在投产后还能将整个加工单元加入该生产线中。由此可见,该种生产线对于将来的扩展能力在产量以及加工内容(如:增加第二火花塞孔、增加阀门以及其它相关内容等的加工)方面都体现了很大的柔性。在单台SPECHT机床上使用新工件转接板和简单工具机,通过程序调整即可实现新品种转换。放置工件的转接板上的数据记录介质使得粗定位之前即可读取数据。加工单元的工控机(中央计算机)控制着整个自动化传输系统,当工件随同转接板一起传输时,在自动化传输和机床之间即会进行数据交换。有了这种设置,各生产单元之间的技术资料整合即可自动完成。
记者:能否介绍一下敏捷制造技术与产品将来的方向?
Dr·Manfred Berger:现在,敏捷制造系统的各项主要技术优势进一步促进了整个系统性能水平的提高和发展。从技术角度看,敏捷制造将来的方向为无冷却液加工,即仅使用最少量润滑液(MQL)的干式加工,另外,系统中降低成本后的加工中心将会在高产量方面发挥效能,双主轴机床可减少空间占有率,同时还可减少有效工件节拍时间(小于30s,同时加工或上/下料两个工件)。然而,操作人员仍是设备绩效保证的重要一环,因此,对于机床的更新换代和系统的进一步开发,必须考虑到操作和维修的方便性。不管怎样,零件创新速度的不断加快和产品生命周期的缩短使我们相信,将来的汽车制造业对敏捷系统的需求将越来越迫切。
评论
加载更多