一、数控刀具模具(冲头)
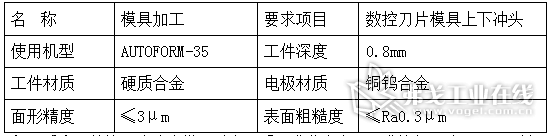
加工难点:数控刀片冲头模具对表面质量求非常高,要求均匀一致,无明显缺陷,刃口锋利;另外,这类模具上很多加工面具有复杂的花纹,对加工后的面型精度要求也非常高,达到3μm。因此,加工时,要求参数合理,放电能量控制精准,要求伺服间隙控制稳定,加工过程不能出现异常放电。另外,为了面型精度,不能采用摇动加工,必须通过多电极的非摇动的方式进行加工。
加工前外观:
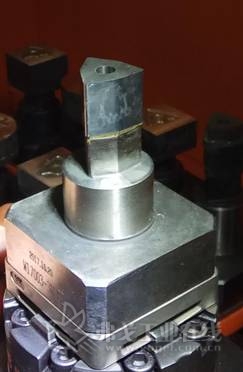
试切方案:
夹具及量具:初始套装3R-628.28-S、基准座3R-610.21-S、定位心轴3R-606、基准测球3R-656.31-3P
装夹方法:
1. 工件和电极都使用3R基准加工并安装在机床上
2. 基准测球装夹在主轴的3R基准上,定位心轴装夹在工作台的3R基准上。
3. 使用机床外形找中功能,找到工作台上3R基准的中心。
4. 依次将三个电极安装在工作台的3R基准上,使用基准测球测量电极中心点的高度,记录并计算中加工电极和粗加工电极,精加工电极与中加工电极的高度差,在更换电极时,使用刀具补偿功能调整偏移量。
测量标准:重复测量中心误差1μm以内
供油方式:浸没加内孔下冲油
方案简述:第一个粗加工,第二个半精加工,第三个精加工。
加工参数选择:中粗加工采用效率优先,精加工采用抛光功能,
加工后外观:
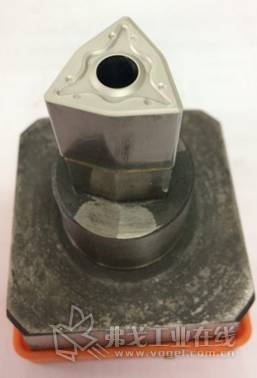
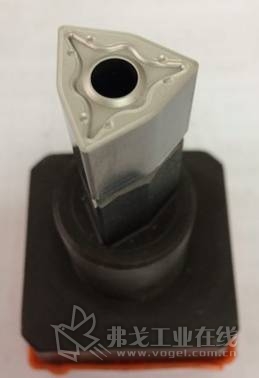
上冲头模具 下冲头模具
加工结论:
总加工时间为上模2小时48分钟,下模2小时39分,表面粗糙度为Ra0.28μm,面形精度2微米,表面均匀一致,刃口锋利,无缺陷。试验结果表明:AUTOFORM35机床综合加工效率与外国某知名公司设备(约2小时30分)加工效率相当,加工后的表面质量、电极损耗和加工效率与其相当。另外,AUTOFORM35机床对电极的制造无特殊要求,延用某刀具公司现有标准制造的电极就可完成整套模具的加工。
二、软磁材料模具(模体)
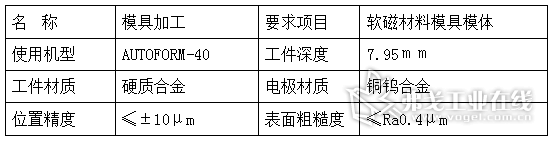
加工难点:软磁材料模具模体加工的工件材料为硬质合金,加工深度较大,要求加工面均匀一致,无明显缺陷,电加工面与线切割加工面要求衔接平滑,且不损伤线切割面;另外,对加工效率要求较高。
加工前外观:
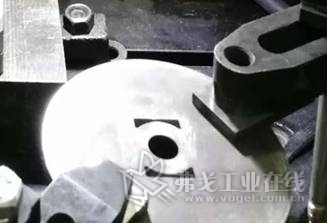
加工方案:
夹具及量具:基准测球3R-656.31-3P
装夹方法:用压板将工件压在工作台上,电极使用夹板装夹在主轴头上。
找正方法:
1. 使用千分表将工件上表面沿X向和Y向分别找正,将工件线切割平面沿X向找正。
2. 使用千分表将电极底面沿X向和Y向分别找正,将电极侧面沿X向找正。
3. 借助两个基准测球,使用机床外形找中功能将电极中心与工件中心重合;借助两个基准测球,使用端面找正功能,使不同电极间的Z向加工起始点重合。
测量标准:借助两个测量基准球进行多次重复测量,中心与端面误差≤2μm
供油方式:内孔下冲油
方案简述:第一个和第二个电极粗加工,第三个半精(中)加工,第四个精加工。
加工参数选择:中粗加工采用效率优先,精加工采用抛光功能,
[加工后外观]
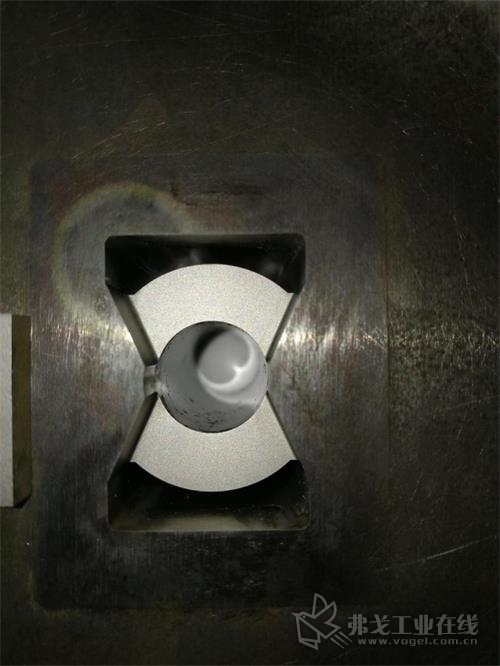
加工结论
总加工时间为7小时4分钟,表面粗糙度为Ra0.29μm,位置精度为5μm。加工质量和效率符合用户要求。试验结果表明:搭载了新一代节能型电源和源于国家重大专项成果的EDM专用数控系统的AUTOFORM40机床的综合加工效率有大幅提升,表面质量也有较大提升。与公司原有机床GW735机床(约18~20小时,表面粗糙度为Ra0.4μm)相比,加工效率提高了近2两倍,粗糙度也有较大降低,电极损耗也无明显变化。
评论
加载更多