如今,制造厂商必须越来越多地符合用户对高度个性化产品的需求和期待。但是,一旦产品个性化,生产效率可能会受到影响。无论是作为一家制造厂商,还是作为一家制造技术方案的供应厂商,Okuma公司对于这种情况已经非常熟悉。早在2013年,该企业就已经为其多功能机床和大中型车床设备的生产开启了Dream Site 1(DS1)智能工厂技术。制造厂商通过采用高度自动化的生产设备,可以缩短生产准备时间和极大提高生产效率。
针对小批量生产的技术方案的多样性
基于在设计和实施DS1过程中所积累的知识,Okuma公司在新的生产设备上投入了相当于800万欧元的资金。其目的是要对品质较多但批量很小的混合性产品进行全自动、高效率的生产,以对Okuma公司多品种产品所需的零部件进行制造。
事实证明投资是值得的,因为Dream Site 2所达到的自动化程度比DS1还要高。针对无缝对接的物流作业,所有元件均设有工件ID号,以便系统随时确定出其位置和目的地。这使得用户和物流管理人员可以随时作出快速反应,并为确保每一个部件的连续加工而可及时采取可能的替代措施。新设备采用了Automated Guided Vehicles(AGVs)自动导航车技术。通过采用无人驾驶运输车辆,可以省去物料的人工搬运,从而极大缩短不同装夹作业之间所需的时间。
目前,DS2可以实现72h完全无操作的运行。在过去,对于加工线上产品品种繁杂且加工批量小的情况而采取机器人作业的做法遇到了问题。通过对各种不同加工工艺的融会贯通,DS2技术解决了此类问题,并允许在完全无人化的零部件生产中采用机械自动技术方案(图1)。在DS1应用基础上得以改进的生产计划系统(PPS)可以显著缩短供货周期,并使Okuma公司能够对持续变化着的生产要求和用户愿望作出灵活的反应。
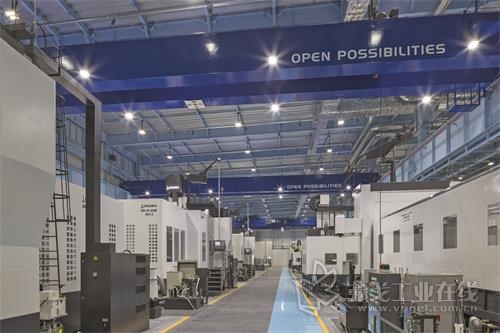
图1 DS2系统可以在制造批量小、品种多的产品过程中达到与大批量生产相同的良好效益
设备3D模拟
为了使DS2系统实现顺畅运行,Okuma公司采用Frontloading(前端装载)技术,以便在生产开始之前尽量多地完成其他工作步骤。对此,一个重要的工具便是3D虚拟监视器。应用软件依据机床特定的精确数据,生成设备3D模拟场景,用户事先即可知道是否能够在所计划的时间段内对工件进行精确和无干涉的加工。由此,在生产开始之前,就可以避免高昂的维修和停机等成本。
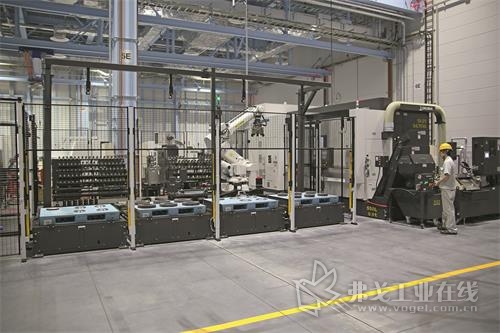
图2 针对无人化的生产,DS2系统实现对灵活加工站和加工系统的操控
DS2系统所含4个部分的占地面积可达11000m2。在小件加工区域,主要是对各类不同的、尤其是直径在30mm以内的圆形工件进行生产,例如凸缘和弯头等(图2)。此类部件在Okuma公司的MU-4000V型立式五轴加工中心设备上接受加工。机床设备被置于一个无人操作的机器人辅助的加工站(FMS)内,可以确保实现不间断的切削加工和全自动卡盘与刀具的更换。工件的更换也可由机器人来执行。通过上述的AGV技术,可以对原材料和成品部件进行全自动输送。DS2系统放弃了使用需要人工操控的叉车(图3)。
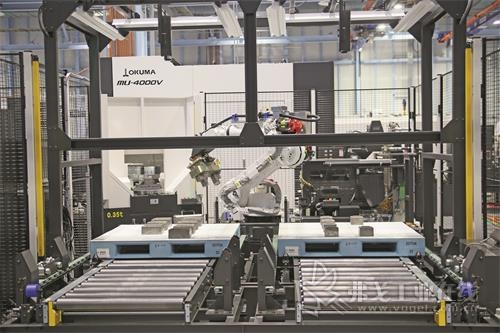
图3通过采用机器人来搬运材料、刀具和工件,DS2系统可以达到很高的自动化程度
无变形的表面质量
精密部件制造系统负责对主轴、尾座端部、凸缘和其他众多部件的生产。这个区域的温度被保持在恒定的21℃±1℃的水平上。在此理想的条件下,Okuma GP-47N型磨床设备可以达到最优的表面质量,而不会出现热变形等现象(图4)。
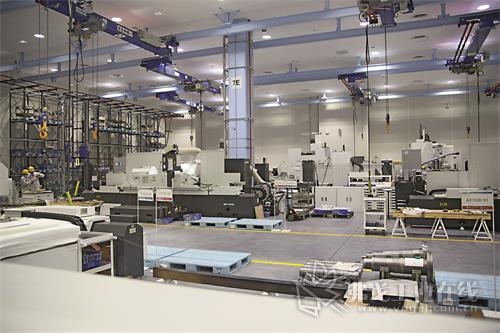
图4在精密部件区域维持着21℃的恒温,以避免因温度变化而导致精度偏差
针对中等规格零部件的区域包含了主轴箱、尾座和转位刀座等。对于此类部件,则采用4台Okuma MA-600HII型加工中心和3台MB-8000H型设备单元进行加工。该区域由一套灵活的生产系统(PPS)进行控制。该生产系统可以对FMS和机器人、多套物料投放与元件输送的AGV设备以及成品储架系统等部分进行整合。物料投放后的所有流程(如装夹、切削和去毛刺以及清洗等步骤)均实现自动化,以确保达到24/7无人生产状态。
设备的最后一个区域包含了诸如机架和鞍座等的大件产品。为了对此类大尺度部件进行加工,Okuma公司在一个灵活的加工站上投入使用了3台MCR-BHI型龙门铣床和一台大表面磨床。通过采用全自动装夹技术,上料和卸料的时间得到大幅缩短。
DS2整体工厂结构可在中央监视器和平板电脑上实现可视化。此类装置可运行本公司自行开发的Application Factory Monitor(应用工厂监视)系统,可以显示整体设备和所有加工站以及机床设备的工作状态。企业可以实时观察和分析设备的各类数据,从而可以快速识别和处理所存在的问题,或识别和分析造成生产效率低下的各种缘由。在设备运行期间,软件系统收集和储存了所有信息、报警记录和停机时间。最终结果是工厂可以每天获得更多的信息资料,从而使每个生产循环都能够更优于前一个生产循环。
能源成本降低30%
整体设备采用地热能源来进行高效加热和冷却。与DS1一样,DS2也利用外壁上的绝缘太阳能蓄电池和发光二极管照明系统以及针对空压机和电热泵的逆变器控制系统。通过此类措施,Okuma公司可以促使能源成本降低30%。
Okuma公司对DS2系统的功效非常满意。自从2017年5月份开业以来,该制造厂商把其零部件生产的生产效率提高了30%,并使其生产循环时间缩短了一半。这家独一无二的供应厂商将在新型加工设备的研发工作上继续投入,以充分挖掘出工业4.0的内在潜力。目前,工作的重点是在于对DS2的扩展上。企业也规划出了一个装配区域,以便从设备中得出一个能够整合从零部件制造一直到机床设备装配等所有步骤的类似于DS1的集约式工厂。同时,Okuma公司负责人也已经有了另外一个梦想:该制造厂商拟通过第三套Dream Site系统来再次为智能制造设置新的标杆。
Okuma公司很清楚一点,即面临着同样瓶颈的客户也都在为能够实现个性化大批量生产而努力拼搏。因此,该制造厂商把在DS1和DS2开发过程中所获得的技术诀窍传授给客户,以便帮助他们对其生产进行优化。有了自行开发的技术工艺,Okuma公司也可为其他生产企业提供可视化和数据处理等方面的相同的提升机会。
评论
加载更多