平均系统可以通过设计过滤掉所有表面组成部分,粗糙度除外。粗糙度是指因车削、磨削、铣削或其他加工过程而留下的痕迹。但是制造商只知道平均粗糙度Ra还不够,制造过程中也会产生其他表面问题,如无法显露出来的波浪等。如果放任不管,则表面参数可直接影响产品质量。
在现今生产成本不断增加,客户对产品性能和可靠性提出了更高要求,这一解决方案顺势而生。诚然,大部分工件的表面修整规范仍然要求进行平均粗糙度测量,所用工具并不能揭露真实的表面特征。
曲轴案
发动机性能也来越高,客户投诉越来越多,某曲轴制造商一夜之间焦头烂额。通过检查加工后的曲轴轴颈表面粗糙度,发现某条生产线出来的产品表面粗糙度高了18~22 μin。
面对这种情况,该制造商增加抛光操作,并成功将粗糙度降至标准范围内。然而,结果却不尽人意。
正常情况下,平均粗糙度为18 μin时,轴颈负荷接近2 000 bar/in2。剖析显示粗糙度升高至22μin,同时,波纹频率下降,改变了部件的几何形状。最终导致轴颈与轴承之间的接触面积明显降低,负载提升到了20 000 bar/in2。
抛光只是降低了接触面积,让问题更加复杂。负载增加了10倍,增至200 000 bar/in2,导致曲轴在用了不到200 h后便出现裂纹。发现问题后,有关人员对波形进行了反向跟踪,发现原因居然是生产线上某机床非圆轴承振动所致(如图)。
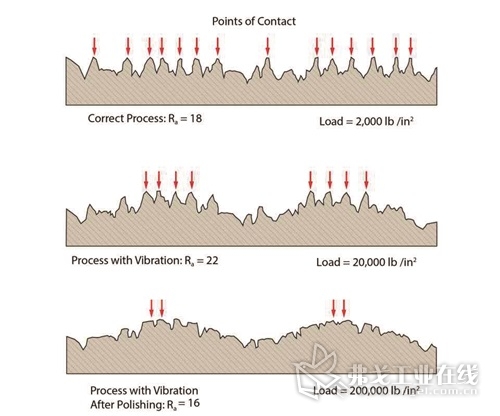
图1 虽然增加抛光操作可以将Ra减小到规定范围以内,但是也减少了轴颈和轴承之间的接触面积,增加了负载,导致产品不合格率高达98%
计算机磁盘损坏案
在使用相同过程对计算机磁盘进行8个多月的抛光后,制造商发现出现了严重问题,突然表面精细度(平均粗糙度)从10~12 μin升高到了15~17 μin,升高率达到50%。
各种校准方式,如修正砂轮、更换冷却剂、重新修正砂轮和更换磨料都没有起效。最后,制造商对表面进行了分析,发现错误:出现了0.006 in的波长。
进行调查后,发现问题来自屋顶某大型空调的偏心轴产生过大振动,影响到工厂建筑和机器。这种低频振动已经超出了平均粗糙度测量机器的工作范围。
从故事中吸取的教训
虽然Ra参数对于判定表面是否合格能够有一定的价值,但是在大部分情况下测量出来的数值并非其真正值。制造商如果在测量Ra时没有对Ra的限制条件进行全方位了解,没有选择正确的临界点,则很有可能会出现各种问题,特别是精细表面。大部分问题在对表面进行剖析后很容易解决。
现代表面精细度测量设备可以显示整个表面图像,准确提取各个组件的剖面,进行比对分析。然后将高频表面粗糙度与低频波浪分开,查到制造期间微英寸精细度发生变化的原因。
制造商可以记录和检查每个表面的总剖析结果,并对其任意部分进行分析,则可以建立和维持表面公差,使其满足产品性能要求。如今,达到最佳的表面精细度已成为基本要求。
评论 0
正在获取数据......