对于很多车间而言,遇到加工问题时,就会想到更专业的工具制造商。销售人员会前往现场,对出现问题的操作进行观察,然后根据公司的选项提出建议。结果往往都是“试着”将他们推荐的切割工具、刀片或刀架插入加工过程中。所幸工具供应商会在车间停留一段时间,与车间操作人员或制造工程师一起开展工作,直至解决方案的结果得以证实。根据Sandvik Coromant所言,这种方案比优化某一个加工过程更能起到改进效果。
如果将上述简单的故障检修扩展为长期队伍建设持续性改进,将会发生怎样的变化?如果销售代表的知识储备、经验与工具公式的技术资源相结合,又是否能够解决所有制造问题?
精益生产实践新视角
这一现象正在Volvo Powertrain北美公式的马里兰州哈格斯敦工厂发生(图1)。2017年,由50多位Volvo公司和Sandvik Coromant公司代表组成的团队进行了为期一周的生产改进计划(PIP),旨在提高两个新增生产单元的加工过程。
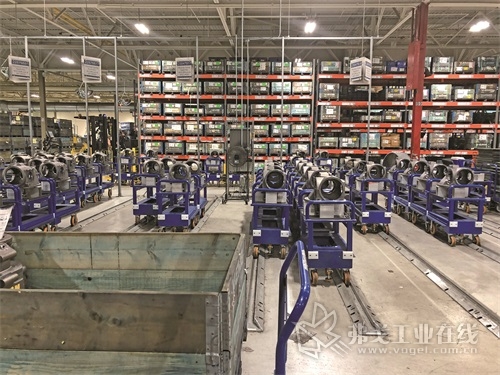
图1 Volvo Powertrain公司在马里兰州哈格斯敦的工厂可生产D11和D13发动机以及I-Shift自动手动变速器,图中所示轴套成品已完成加工,准备送往组装部进行组装
Volvo公司的加工主任Johan Alexandersson先生解释道:“设备虽然购入不久,但工作人员已经熟练掌握了设备的使用方法。而现在面临的问题主要是公司的铸造供应商被收购,而收购方开始执行另外一种铸造工艺。材料达到了我们提供的规范,但硬度更大,孔隙多,铸造过程中公差控制发生了一定变化。我们发现工具磨损情况日益严重,导致产量严重下滑,工具成本明显增加。”
Volvo公司的PIP以轴加工领域两大项目区域为中心。第一个是三轴或四轴的Heller H 5000卧式加工中心加工单元,采用的是HSK 100主轴、800 mm×800 mm×800 mm工作区域,两次切割之间的时间间隔为4 s(图2)。第二个单元由两台Okuma 2SP-V60双轴立式车床组成,每台配备了转速为2500的主轴和机器人部件搬运系统(图3)。Johan Alexandersson先生告诉我们,PIP的目标是增加设备效率,降低产品报废率,提高工具使用寿命。
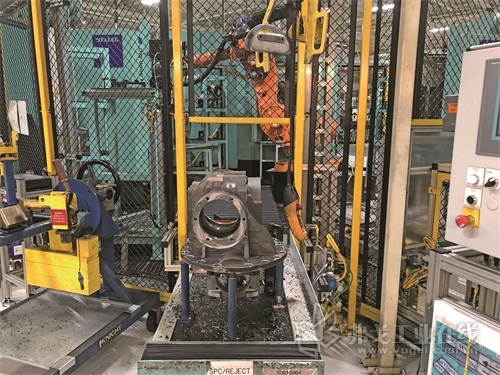
图2 Volvo Powertrain公司的Heller H 5000四轴卧式加工中心正在输出轴套成品

图3 Volvo Powertrain公司的Okuma 2SP-V60双主轴立式车床主轴转速2500转,还配备了机器人部件搬运系统
Sandvik Coromant公司的销售工程师Curtis Scott注意到,和典型的PIP不同,Volvo公司的PIP方案要求利用精益方法分析各个生产区域。而在普通PIP中,则是解决某一具体问题。他说:“Volvo公司的PIP非常丰富,除了加工过程外,我们还查看了材料流和安全问题以及机器和支持设备布局、操作员日常工作步骤等,不放过任何一个细节。”
不言而喻,Volvo公司并非精益制造方面的新手。将两家公司聚集在一起的并非缺少精益的制造知识,而是希望能有更多的突破。
提高卧式加工单元的生产能力
Sandvik Coromant公司的工程师与Volvo公司的指定员工分成两个小组,负责卧式加工单元的小组在调查过程中发现,机床和固件很容易完成4140钢制后轴壳的加工任务,但是建议更换铣刀。例如,针对特殊订单安装的切口铣刀采用的对称设计导致其位置偏移,需要加强加工主轴的维护工作。于是公司将其改为标准的CoroMill 331切口铣刀,过程安全性和部件质量得到明显提高,并且机器负担下降,减少了维护问题。另一款特殊形式的工具,12刀片铣刀(交货期为9~12周)被CoroMill 390 90°套式面铣刀和CoroMill 495倒角铣刀代替,单次循环时间降至1.75 min。
直径4 in的CoroMill 745套式面铣刀也可以达到蕾西效果,将循环时间缩短一半,只需1.34 min,刀片数量也降至11,原因是切割边缘数量从4个刀片提高到了14个,明显降低了每个部件的工具成本。通过这些改变你,单元产量翻了一番。
稳定车削单元
目前工厂中的车削单元存在一些铸造问题,导致后小齿轮的加工过程存在不确定性。操作人员不得不频繁更换工具,造成机器停机。双主轴车床操作也存在不平衡问题,导致10号工序忙碌不停而20号操作工序却闲置不用。团队必须以缩短循环时间,提高工具寿命和过程稳定性为内部目标,对设备进行变更。现在,完成生产所需时间最多6 h。
他们开始使用CoroTurn Prime全方位车削工具,以及其他多功能开槽和镗削工具,进行后小齿轮车削。车削过程中,不需要长时间的重新编程。同时因为Prime能够将粗加工和精加工结合到一个单独的工具中,其切割效率明显优于比传统解决方案,将周期时间减少了一半以上。
这次的车削操作更换以及启用带后倒角功能的专用Coromant钻孔工具减少了1.5 min的循环时间,整个车削过程变得更加顺畅。
持续的改进
虽然改进效果明显,两个队伍并没有满足于此,还提出以下改进意见:
第一,通过Heller单元的值流映射确定,更改材料装载到托盘系统的方式,可以提高产量,这种变化最终简化了材料搬运过程(图4);
第二,通过防错装置检查固件,可以避免由于部件装载不当而造成的生产延误,并减少操作人员在执行操作时的困惑;
第三,扩大卸货区域,增加物料搬运车数量,满足日常需求,也有助于消除开放式地板空间被随机物品占用问题;
第四,通过Andon系统安排午餐休息时间以及增加机器停机时间的可见度,进一步提高机器的整体设备效率;
第五,安装快速更换的模块化工具不仅可以缩短安装时间,而且可以加快操作者改变加工工具的速度,让整个过程更加简单。

图4 图中所示一对轴套已放入Volvo公司的Heller水平线上准备进行最终加工,每个加工中心配有HSK-100主轴和800mm2的工作区
经过一年的使用,Johan Alexandersson先生在报告中表示带领团队执行了多项Sandvik Coromant公司的建议:“其中最大的改进应当归功于Okuma的设备单元,将更换时间缩短了约2 h。我们循序渐进,不断改进,现在已在多个生产区域执行成熟的快速换模(SMED)程序,凸轮轴机加工部便是其中之一。我们将操作过程拍摄下来,将整个制造过程细分为多个部分,然后根据观察进行快速更换系统设计。模块化快速更换切割工具的应用也很成功,缩短了设置时间从6 h缩短至1~2 h。整体而言,可谓受益匪浅,我们准备将此项目扩展到其他机架工厂。”
评论
加载更多