作者关注的是使用激光粉末床融合(PBF)的增材制造(AM)。考虑到粉末床融合(PBF)具有制造复杂形状和有机结构(这些形状和结构在以前由于成本过高或无法通过传统的制造操作来制作)的能力,所以这种增材制造(AM)过程在很大程度上起到了推动的作用。例如,激光粉末床融合(PBF)所带来的设计自由度可以被应用于轻量化的组件,以便构建复杂的晶格结构来提高材料的使用效率,整合多组件装配,优化零件的形状以实现其功能。当然,激光粉末床融合(PBF)也有缺点,包括难以移除的支撑结构,可能在构建过程中出现问题的薄壁/高深宽比零件,对表面粗糙度的分层效应和不同的工艺参数设置(例如,上表面和下表面的激光设置)。
尽管激光粉末床融合(PBF)有很多优点,但最大局限在于可以在构建外壳中可打印的零件尺寸。但由于各种各样的原因,大多数商业激光粉末床融合(PBF)系统只能提供一个250 mm×250 mm×325 mm(约为10 in×10 in×12 in)的建造外壳,不过一些激光粉末床融合(PBF)系统可以容纳更高的部件,且更大的系统也正在开发中。例如通用电气的概念激光X射线2000R拥有一个800 mm×400 mm×500 mm的建造外壳,该公司计划建造一个至少1.1 m×1.1 m×0.3 m的系统。
激光粉末床融合(PBF)系统限制构建外壳尺寸的原因之一,是填充机器所需粉末的成本。填充一台激光粉末床融合(PBF)系统所需的粉末量等于lxwxh(构建板的面积乘以部件的高度),无论在构建板上制造多少个零件,都必须往机器里装那么多的粉末。因此,最高部件的高度决定了填充机器所需的粉末体积,而与生产量无关。
虽然更大的构建板或更高的构建高度当然是可能的,但粉末的成本很快就会变得非常高。作者在宾州州立大学(Penn State)金属增材制造实验室CIMP- 3D的两位同事估计,大约3~4年前,在一块10 in×10 in的构建板上,用Ti-6Al-4V制作一个6 in高的组件需要成本近5万美元的粉末。而自那时起,Ti-6Al-4V粉末的成本已经下降了30%~40%,但这仍然是一个过高的成本,无论是在一个给定的构建板上制造数百个部件中的其中一个,都必须支付这个成本。
那么,企业如何能够负担得起直接使用增材制造(AM)来生产更大的部件?直接能量沉积(DED)是一种很有前途的激光粉末床融合(PBF)替代方法。在增材制造(AM)过程中,激光(或电子或等离子)束被用来创建一个能注入粉末和注入金属丝的熔池。当粉末或金属丝进入熔池时,被加热并熔化,与相邻的材料和下面的层相结合,然后随着熔池的移动迅速凝固。
因为直接将粉末或金属丝放入熔池中,所以不必像使用激光粉末床融合(PBF)那样填满整个构建外壳。在这种情况下,材料成本直接与零件的体积成比例。当然,根据激光参数,粉末捕捉率(喷嘴喷出的粉末量与熔体池中捕获的粉末量之比)一般在40%~80%,但即使这样,也只需要分别用2.5~1.25倍的粉末,来构建带有直接能量沉积(DED)的部分,而不是由构建高度所定义的粉末体积。如果是金属丝应当会更好,因为熔池的大小可以融化整个金属丝。
在零件尺寸方面的另一个大挑战是制造速度,直接能量沉积(DED)的性能又一次超过了粉末床融合(PBF)。激光粉末床融合(PBF)在制造部件时通常使用50~100 μm的目标尺寸,然而,在基于激光的直接能量沉积(DED)系统上,目标尺寸在商用系统上可以在0.5~3.0 mm。较大的光斑尺寸意味着较高的沉积速率,这意味着更快的构建。其中速度最快的直接能量沉积(DED)系统是Sciaky公司的电子束增材制造(EBAM)系统,该系统利用电子束熔化的金属丝,每小时可沉积15~20 lb钛(如图)。Richard Martukanitz博士是宾州州立大学CIMP–3D的主任,他提供了一个关于不同沉积速率的比较方法。
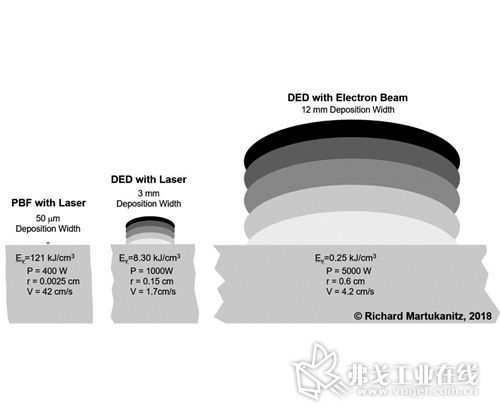
用激光和电子束进行的激光粉末床融合(PBF)和直接能量沉积(DED)的相对沉积速率。(Ev表示能量/体积,P表示功率,r表示半径,V 表示速度)
那么,直接能量沉积(DED)的缺点是什么?想象自己正在粉刷房间的墙壁,粉末床融合(PBF)就像一把在刷墙的非常精细的油漆刷。在粉刷墙角和边缘需要非常精确,但要粉刷墙壁本身需要很长时间。另一方面,直接能量沉积(DED)就像使用一个滚轮,它覆盖了很多区域,速度很快,但是在墙角和边角上就没办法很准确。因此,直接能量沉积(DED)可以用更少的材料更快地制造零件,但直接能量沉积(DED)零件将需要大量的加工和精加工以满足公差的要求。
评论
加载更多