前言
新千年迎来了金属切削应用领域的革新性解决方案。伊斯卡公司作为金属切削领域的技术先行者之一 ,正研究如何将增材制造工艺集成至刀具制造体系中。富于开创性的金属切削技术促成伊斯卡的研发工程师们能在为用户带来降低生产成本,提高生产率的技术创新的解决方案方面不断推陈出新。
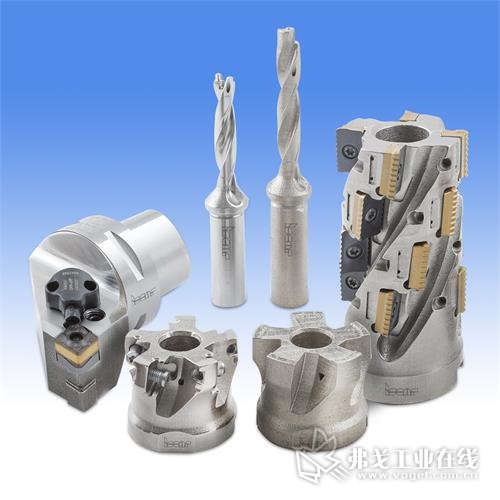
增材制造技术
数字化革命(也称为第三次工业革命)的主要成果之一就是推出了3D打印技术——即在计算机控制下通过熔融材料,逐层叠加生成具有三维(3D)特性物件的一种方式方法。以前,3D打印技术被视为“科幻小说”元素,在过去的二十几年间,3D打印已成为一项为制造商们和设计师们这类群体所接纳的一项颇受欢迎的因技术推动而带来的增益项。
今天,该方式方法主要被称为增材制造(AM)。增材制造这一词条准确折射出3D打印最重要的两大特点:制造:已经超越了原先人们所认知的快速成型领域,该方法已推广至许多工业应用中,用于生产各种零部件;增材:与传统的减材制造技术形成了鲜明对比,该方式方法通过不断地叠加材料制造出所期许的物件。而传统的制造方式只有在装配阶段才添补材料组件。
现在市面上有各种各样的增材制造技术,这些技术基于不同的物理原理:激光立体印刷术(SL)、多喷头建模(MJD)和激光烧结(LS)等等。根据最新的国家标准和国际标准,AM增材制造被明确地划分为几类。上世纪八十年代,3D打印开始被作为一种设计工具,用于实现原型的快速制造。通过3D打印,人们可以不再依赖于传统的二维图纸,而是可以创建出全息还原的3D模型;从而使人们能从美学、功能性、重量和表面光洁度等产品特性方面更好更直观地理解物件;并且该技术的采用还能够实现更快速的生产制造时间。
增材制造技术的应用
随着3D打印工艺持续不断的技术进步,人们最终步入了AM增材制造的时代。二十一世纪初,该技术开始被用于批量生产。与所有的技术创新一样,随着AM增材制造技术的普及,不断增长的产业应用和规模经济带来相关设备销售的快速增长,促使AM增材制造设备制造商之间产生了激烈的竞争,其结果是人们获取该技术的代价在降低。尽管在某些人看来,3D打印机似乎是来自未来的技术;但是在许多应用领域,该技术已经变得像CNC机床一样,成为了主流。
根据媒体和技术报告所称,3D打印主要应用于航空航天、军事、汽车和医疗行业,其中AM不仅仅用于原型制造,也可以用于小批量甚至大批量生产。尽管该技术的应用日益广泛,但是距离成为全球金属加工的主流技术,仍然还有很长一段路要走。
在医药、航空航天、汽车和军事等难以尽数的行业中,增材制造技术为各种组件的生产打开了全新的视野。更令人惊喜的是,数字化技术简单地抹去了物理空间的边界,现在无论3D打印机与计算机相隔有多远,人们只需将计算机模型发送到3D打印机即可进行生产,并且在组件生产过程中完全不需要进一步的人工干预。例如,现今在太空飞行期间,能实现在飞船上直接打印必要的备件。此外,还可以设计并特别定制骨科植入物。神奇的是,3D打印机还具有自我修复功能,甚至可以快速地生产自身所需的破损的部件或临时替代部件。
在航空航天业中,虽然有一些小型零件、配件及硬件非常适合采用3D打印制造,但是为安全起见(可以理解为,因为航空航天业对安全性的要求非常高),AM增材制造生产出的关键部件还需要通过各种严格的测评后,才能用于取代依赖传统加工方法所制造出的零部件。然而,人们通常能将AM增材制造用于制造各种各样的固定装置、夹具、量具;飞机的生产涉及了整条复杂的生产制造链,需要大量的夹具。从这一方面来看,在生产中引入AM增材制造从根本上减少了生产准备的时间和成本。
大大减小的尺寸和不那么严苛的安全标准为AM增材制造应用于无人机(UAV)制造开启了大门,这种新方法不仅可以减轻重量,还能以更低的成本更有效地从空气动力学角度来塑形无人机。
在全球的航空航天领域,钛是最常用的材料之一。而钛基合金零件通常都通过减材制造的方法加工来的。在典型的加工过程中,大多数昂贵且难以加工的材料被切除。飞机制造商们正在致力于使用钛粉来生产相对小型的钛基合金零件。类似于航空航天业的这一做法,人们同样也将AM增材制造技术应用于汽车制造业。
增材制造的优缺点也是并存的,准确理解这些优点和缺点就可以更好地在金属切削领域定义AM增材制造:
优点:在生产制造复杂零件时,采用增材制造能显著降低生产成本;极大的灵活性是该技术的另一项主要优势,例如,您可以使用同一台3D打印机来轻松制造不同的零部件,而无需进行大幅度的调整;此外,在实际的原型制作中,只需通过编辑零件的计算机模型,并进行重新打印即可完成零件的设计更改,因此AM增材制造技术不但能够显著地缩短从概念到交付的这一周期,还能够通过快速制造相合的部件对现有设计进行更改;从工程的角度来看,该方式方法确保了所生产出的原型零件非常贴近人们的设计:比如不同壁厚却具有同等强度;必不可少的可提高有效流动效率的管道形状等等;另外,在增材制造过程中,因所用即所得从而大大节约了生产中的物料成本。
然而,AM增材制造并非没有缺点:在精度方面,该技术尚不能满足零件表面精度要求,因此通常需要采用传统加工方法进行精加工;并非每种工程材料都适合于通过增材制造方法制造零件;目前的3D打印机工作空间尺寸有局限性,不能用于生产大型部件。
伊斯卡将增材制造应用于刀具制造领域
伊斯卡的研发部门深谙AM增材制造的优缺点,并基于这个认知将其应用于金属加工领域。当用于生产切削刀具时,3D打印也可以提供多种情况下的解决方案。通过AM增材制造能实现在刀体内创建复杂的内部通道和腔体。这些特征可以使冷却液流经刀体内流道直达刀具切削区域实现冷却。在设计高压冷却刀具(HPC)时,刀体内部冷却通道及其横截面形状是关键因子;增材制造为内部通道的“成型”提供了理想的解决方案。此外,AM增材制造技术还能够制造具有排屑槽,复杂表面形状,背锥和清根等特征的刀体。而采用传统技术时,这些特征都只能通过切削加工来实现的。在这些领域中,AM增材制造的应用将减少生产工步并缩短加工周期。此外,AM增材制造还能确保在成形过程中兼顾刀体强度和排屑槽空间之间的完美平衡。
当AM增材制造发展到允许采用硬质合金粉末或具有相似物理性能的材料来打印物件时,刀具制造将抵达一个全新的起点。伊斯卡研发工程师们正在采用新的加工方法来制造可转位刀片,取代早前昂贵且耗时的模具压制工艺;能显著缩短刀体和刀片的从研制到实施切削试验的周期。
尽管AM增材制造在刀具行业的应用有着鼓舞人心的前景,但仍有几个障碍需要克服。目前,由于受到精度的限制,3D打印还无法完全取代传统加工。例如心轴或刀柄的中心孔表面需要磨削加工;刀体的刀片定位槽基准面需要铣削加工;内孔螺纹也需要进行螺纹加工。值得注意的是,机床生产商已经推出了“混合制造”加工机床,融合传统的金属减材制造技术与3D打印技术于一体。但这些采用增材制造技术生产的零件的疲劳寿命、疲劳断裂和高速旋转下的可靠性都还有待考究。
伊斯卡作为世界领先的切削刀具生产商之一,其研发部门已引进了AM增材制造这一全新的技术,目前还有限地应用于制造原型;另外还主要用于小批量生产。这些领域的进展意味着在不久的将来,3D打印技术将在切削刀具生产领域得到广泛应用。
评论 0
没有更多评论了