从Precision Manufacturing Solutions Inc.(PMSI)公司名字第一部分便可以看出该公司的主要业务领域。自1962年以来,这家承包了制机加工的车间在复杂的医疗、航空航天和军事部件加工方面从未停下精益求精的脚步。
PMSI生产的每个部件都对尺寸提出了非常严格的公差要求,有时候不能超过1/50000000inch(1inch≈2.53cm),而真定位的公差则要求控制在千分之一英寸以内。这些部件的生产环境要求保持干净整洁,采取气候控制措施。PMSI团队加工的材料多种多样,包括特殊的航空航天金属;410、440和416不锈钢;铬镍铁合金; 钛;铝和镁(一种危险材料,需采用特殊的冷却剂,防止发生火灾)。
该车间使用Mazak Integrex 300-IIIST 11轴铣削和轮廓加工机来加工复杂的部件和原型。 但是,由于设备采用的是双刀头结构,设备的后处理器(简称“post”)的开发过程十分具有挑战性。顶部和底部刀头要求单独的刀具路径,而且基本上无法通过两者协调来创建后处理器:刀具路径相互抵消,导致创建出来的数控后处理器无法反映出整个机加工过程(图1)。
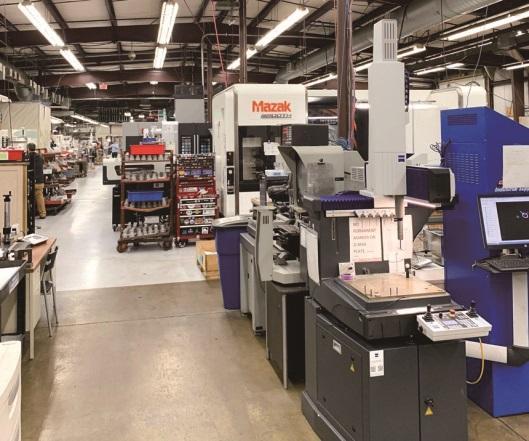
图1 PMSI当前拥有五轴铣床、标准铣床、11轴Mazak Integrex机床以及双主轴双转塔车床。车间同时还拥有3台DMG MORI NMV 3000,配有320个工具转盘,可处理32至115个托盘。该车间员有70名员工,包括36名机械师和6名过程工程师,负责加工过程开发和编程
在创建该机器的后处理器时,过程工程师Shaun McAlevey与Mastercam的经销商Cimquest和CNC Software Inc.取得了联系。协商后,Cimquest公司派出了Mike Slajka,CNC Software公司派出了Pedro Sanchez、Keith Goodrich和Quanwen Du,联手探讨解决方案(图2)。
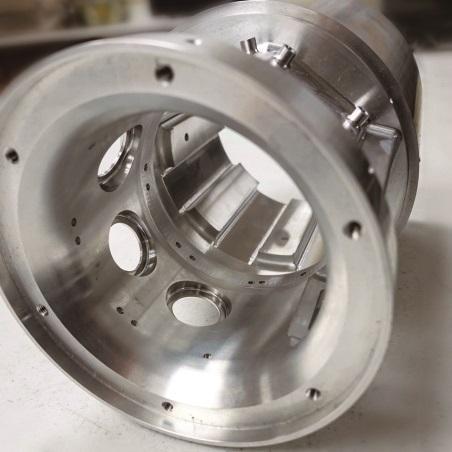
图2 后处理器开发过程中要解决的最终问题包括利用刀具补偿功能,获得在副主轴倾斜平面切出轮廓的工具(在Mazak Integrex上不容易做到)。为了解决这个问题,一支由CNC Software Inc.、Cimquest和PMSI员工组成的团队开展了各种试验,反复修改代码,最终终于找到了解决方案,图中为成品部件
从头开始研发后处理器
Pedro Sanchez先生表示,这项任务内部存在很多复杂因素。项目开始前,他最大的担忧之一是创建出来的后处理器需要先在所有类似的设备上进行测试。他希望编写出来的代码具有通用性,不要对设备的类别有所限制,也不能对操作人员的技能提出太高的要求。他说:“在考虑设备的运行方式时,我们的希望是通用。在设备交付给其他客户后,客户也能够正常运行设备。”
一边是项目人员日以继夜的辛勤付出,另一边是PMSI合同的时间逼迫。“这是一项双重挑战,我们必须充分利用车间的空闲时间来创建后处理器。”Pedro Sanchez先生说道,而该项目约需要6个月的时间才能完成(图3)。
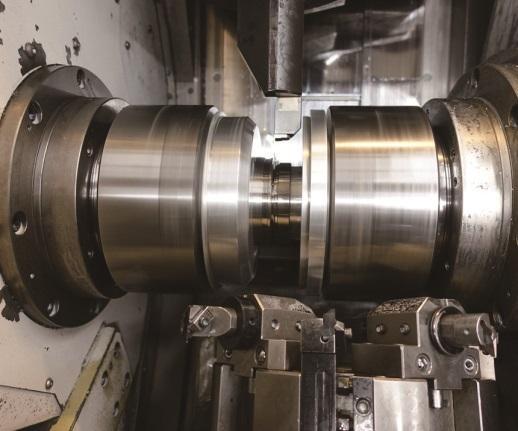
图3 图中所示为Mazak多任务处理机的上部和下部刀塔的视图。图中可以看到主轴与副主轴之间与上刀架分开的过渡区域。该设备使用Mastercam车铣复合软件编程,但是在开发出新款后处理器(6个月)前,暂时还无法做到真正协调两个刀头的刀具路径
Pedro Sanchez先生从一开始就知道,这个项目不仅仅是调整旧的后处理器。“我们使用的是新款Mastercam车铣复合软件,所以不能再将旧款后处理器用在新款发动机上。我们必须从头开始开发整个产品。”在Cimquest和Shaun McAlevey先生的协助下,CNC Software公司的开发团队通过在Mazak的设备上进行测试和代码修改后,带领大家研发出了一款全新的后处理器。工作人员不断运行刀具路径的测试工作,进行查漏补缺,直至后处理器能够准确无误地运行。
最终创建出来的基础款后处理器无缝结合了两个刀头,大大减少了PMSI的编程时间。经过调整后,这款后处理器能够与同一平台上的任何计算机一起使用,甚至适用于旧版的控件。CNC Software公司表示, Mazak Mark第三代后处理器已投入市场,需求量很大。
Shaun McAlevey先生这样说道:安装CAD/CAM软件后,目前设备运行平稳,可以完成各种棘手的任务。Mastercam软件简化了整个编程和机加工模拟过程,他可以轻松获得所需要的代码。
动态刀具路径数量翻了一番
PMSI主要承接军工领域的光学机加工任务。近期,公司新签署了一份合同,专门负责制造具有特定的复杂几何形状的镜架。在加工这些复杂的部件时,刀具需要沿Z轴和B轴倾斜约30°。此外,也会用到各种立铣刀,且在整个过程中,需从一定角度一层一层剥离材料,导致材料承受了较高的应力。以前,部件在加工后会变形和移动,操作人员不得不克服重重困难,采取限位措施,防止部件移动。
为了避免高速加工期间材料承受过高负载,Shaun McAlevey先生引入了Mastercam的Dynamic Motion技术,并通过算法进行刀具和材料监控。在进行一致性非常关键的精确切削过程中,为保持切屑载荷恒定不变,Shaun McAlevey先生还启用了“Dynamic Turning”和“Dynamic Contour”技术。PMSI团队现在可以使用较小的立铣刀来加工具有复杂几何形状和严格公差的小部件。
PMSI现在可以以300inch/min的速度向九轴机床进给材料。在这样的高速进给条件下,必须保证刀具路径准确无误。为此公司购买了Mazak的Smooth平台和Mastercam验证功能,协助查找错误,确保程序人员能够在加工开始预览成品部件并检查代码是否存在错误。
Shaun McAlevey先生还使用Mill-Turn软件中的模拟功能。Pedro Sanchez先生解释道,Mill-Turn支持产品和切割操作的可视化。PMSI团队可以利用这一功能生成代码并重建加工结构,以更好地适应两个独立的刀头,现在可以并排编程上下刀具路径。
“单单是使用Mill-Turn进行编程,都可以节省一两天的时间。Pedro Sanchez和Quanwen Du的加入更是将后处理器的开发时间缩短了好几年。”Shaun McAlevey先生说道,同时也认可了团队在这个过程中的贡献。Shaun McAlevey先生进行后处理器编程期间,CNC Software和Cimquest前后两次造访车间,提出了各种宝贵的意见和建议。
评论 0
没有更多评论了