增材制造在航空航天和医疗市场的广泛使用促使人们不断提高对精加工增材部件表面的要求,以满足最终应用需求。增材制造工艺能够生产出接近最终形状的组件,显著降低了最终精加工的需求。通过增材制造,可以降低材料浪费率,有利于整体制造工艺,但是这也意味着后续的精加工过程对后处理技术和一致性的要求越发严苛。因此,需保证后处理的一致性,满足部件公差和表面质量要求。在对公差和表面提出更高要求的应用中,磨削可以是增材制造的另一个有效选择。与其他传统材料去除工艺相比,磨削得到的表面质量和完整性更好。为了进一步了解增材制造的精加工,尤其是应用于航空航天业中的镍基高温合金部件时,Norton|Saint-Gobain公司的工程师对采用增材制造的Inconel 718样品进行了精磨削研究。研究主要围绕3个问题展开:需要从增材制造的部件上磨掉的最低材料量/体积是多少?使用最新一代的砂轮对增材制造的部件进行磨削可以达到怎样的表面光洁度?第三,精磨削对增材制造组件的表面残余应力(如有)有什么影响?
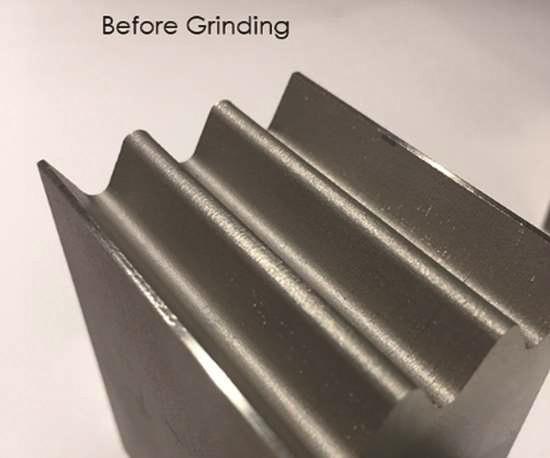
图1 磨削前的AM Inconel 718测试样品
采用直接金属激光烧结(DMLS)工艺制造的AM IN718样品由Stratasys Direct Manufacturing公司提供。图1所示为增材制造测试样品。增材制造后,对样品进行介质喷砂处理,完后消除应力。接着是热等静压、固溶处理/退火和沉淀硬化处理。样品硬度为40 HRC。然后使用Norton|Saint-Gobain Higgins磨削技术中心的Magerle MFP-125.50.65间歇进给磨削机上的Norton NQX60E24VTX2砂轮进行样本磨削,图2和图3所示为测试设置。
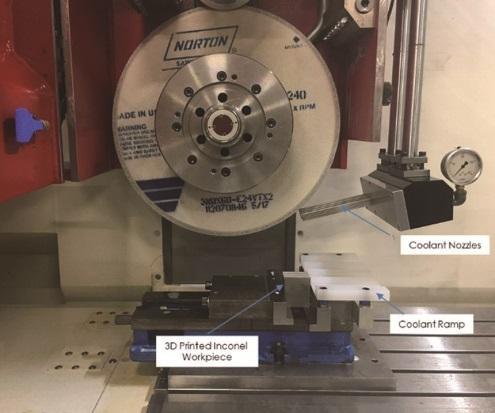
图2 整机设置
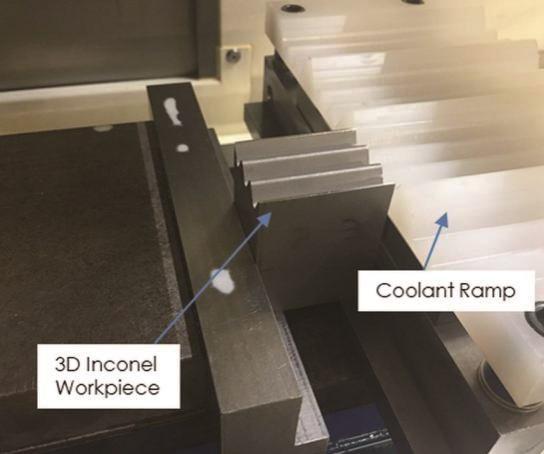
图3 设备特写
首先,逐渐加大切削深度,进行几个区域的磨削,确定需要清除的最小材料量后,对增材制造的表面进行处理。之后按照规定的切削深度进行磨削,然后检查表面是否存在明显缺陷。图4所示为实验期间部件清理后的样品图片。根据实验结果,为了消除增材制造过程中产生的所有几何不一致性和表面缺陷,需要从组件中去除大约0.30~0.45mm的材料。
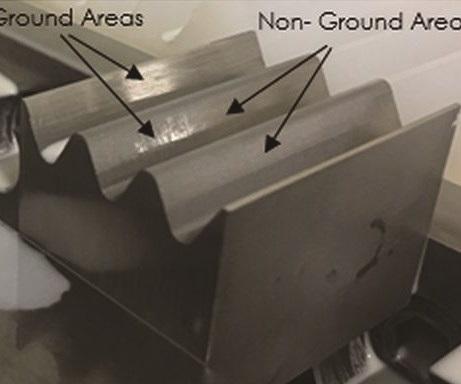
图4 部分磨削后的AM Inconel 718测试样品
本次测试采用的磨削长度为50.8mm,砂轮直径为462mm,工作速度为23m/s。总共对五个的材料去除率(MRR)进行了测试,范围为0.1mm3/sec./mm~3.9mm3/sec./mm。通过更改进给速度(mm/min)或切割深度(mm)调整材料去除率。对多个材料去除率进行了测试,以评估中低材料去除率对表面光洁度和磨削能力的影响。尽管可以使用现代工程磨料以较高的去除率对镍基合金(例如Inconel 718)进行磨削,但根据目前工业上用于精加工标准Inconel工件的标准精加工率,本研究选择了较低的材料去除率。以标准(非增材制造)工件磨削为例,预期结果是,随着材料去除率的增加,磨削功率增加,磨削后的工件表面光洁度(Ra)将增加或表面会变得更粗糙。
磨削前后,采用联邦接触轮廓仪系统5000测量工件的表面光洁度,测量点包括工件上的多个位置和两个方向(图5a和图5b)。此外,还在多个位置进行了非接触轮廓仪表面测量。
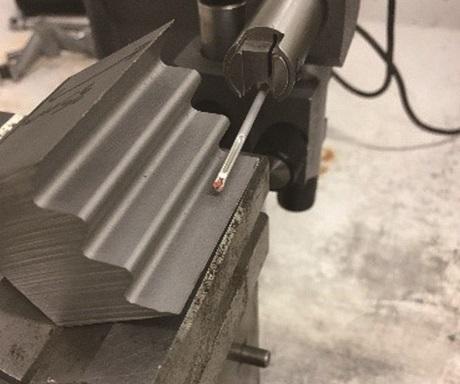
图5a 表面光洁度测量方向(平行于磨削方向)
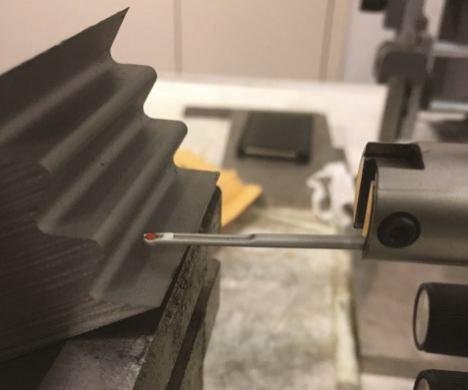
图5b 表面光洁度测量方向(垂直于磨削方向)
磨削前,对增材制造材料的表面光洁度进行评估后发现,在不同测量方向上,光洁度存在很大差异。纵向测量时,平均光洁度为3.3微米Ra;横向测量(图5b)时,平均光洁度为2.1?mRa。而在测量标准铸态Inconel 718材料时,不会出现这种显著差异。这种差异似乎与3D制造方法有关,但是目前尚不清楚确切原因。
采用接触轮廓仪测量磨削后表面光洁度的常规方法是垂直于磨削线,而不是平行于磨削线。本次研究中,在平行于磨削线和垂直于磨削线两个方向上测量了表面光洁度。然后将磨削后的测量结果与磨削前的纵向和横向测量结果进行比较。
重点在于,沿着垂直于磨削线的方向进行测量磨削后的表面时,测针会越过磨削线的波峰和波谷。而在平行方向上进行测量时,测针平行于磨削线移动,永远不会越过峰谷。因此,不出所料,本次研究中,垂直测量得出的(粗糙)表面光洁度明显高于平行方向的测量结果。
磨削前后对增材制造材料的表面光洁度进行评估后发现,不同测量方向的光洁度存在显著差异。本次研究中,采用平行于磨削线和垂直于磨削线两个方向上进行表面光洁度测量,结果确实存在显著差异。在平行方向上测量时,磨削前,平均表面光洁度为3.3?mRa,研磨后为0.21?ma。在垂直方向上测量时,磨削前,平均表面光洁度为2.1?mRa,研磨后为0.5?mRa。
此外,还采用了Nanovea 3D表面轮廓仪和白光色差技术对增材样品进行了分析,将表面特征以视觉化方式呈现出来。在本次测试中,收到增材制造样品后,采用玻璃介质对其进行介质喷砂处理,除去表面凸起的部分。磨削后在表面上可以看到的线条是磨削操作留下的线条。可以使用较细磨料粒度的砂轮或其他打磨产品,例如工程类磨带,进一步减少表面线条,形成超级精细的表面,前提是这点对于组件的性能和质量而言至关重要。
为了进一步了解磨削对AM IN718样品整体表面完整性的影响,采用Bruker-AXS D8 Discover微衍射设备,在收到和磨削样品后,进行了表面残余应力测量。对两种状态下同一样品6个不同位置的测量结果进行比较后发现,在两种条件下近表面残余应力均为负值/存在压缩力。这种情况主要发生在精磨削后的组件上,其近表面残余应力具有压缩性,可延缓表面裂纹扩散,提高疲劳寿命。
本次研究期间,按照5个材料去除率对磨削功率进行了测量。随着材料去除率的增加,磨削功率也随之增加。这种行为存在于大多数磨削操作中。在0.1mm3/sec./mm的最低速率时,磨削期间的峰值功率为1.4kW。而在3.9mm3/sec./mm的最高材料去除率下,磨削功率为10.8kW。
本次研究的结果证明,对增材制造的镍基合金(比如Inconel 718)进行精磨削可以将表面的粗糙度降低近94%(平行于磨削线)或34%(垂直于磨削线)。可以根据要求,使用磨料粒度更精细的砂轮或其他打磨产品,比如工程类磨带获得超精细表面。此外,结果还表明,为了提高表面精细度,需从组件上去除0.30~0.45mm的材料,并清除掉所有与3D制造过程相关的几何不一致性。对于增材制造商而言,最低去除率是关键信息,因为他们一直在努力以最具成本效益的方法让增材制造组件尽可能达到近净形状。此外,残余应力数据显示,磨削后的表面应力具有压缩性,可以延缓表面裂纹扩大,从而延长所制造的组件的疲劳寿命。
评论 0
正在获取数据......