近几年来,公司信息系统支撑了工厂快速发展。但是,车间数控加工设备的信息化管理还比较薄弱。
1、程序传输现状。目前转向架机加工车间管理采用软件和手工编程、使用CF卡/U盘传输或网络拷贝等方式,但数控设备数量多、类型多且系统多,没有集中和统一管理。
2、程序管理及编辑仿真现状。
1)代码编写好了以后,需通过试切来检查错误和优化代码。
2)产品的设计变更导致了数控工艺及文档的变更。
3)大量重要的数据不能备份处理,例如:设备参数和数控代码等的备份,不能应对系统灾难的发生。
3、数据采集现状。
1)现有生产管理软件的基础数据来自于人工采集,缺乏实时可靠性。
2)无法对数控设备有效的进行管理,无法了解生产设备的实时生产状况。
3)无法准确获知数控设备的利用率及影响设备运行的瓶颈。
4)无法准确获知数控设备的待机时间分布,了解设备待机的原因。
为改善以上所述的瓶颈,公司导入DNC/MDC/MDM系列软件产品,实现程序模拟仿真、机床联网/程序传输管理、生产数据采集以及生产数据管理。以下对应用细节做详细介绍。
EDIT程序模拟仿真
EDIT可以对手工或自动编写的代码进行编辑和仿真,如图1所示,可让操作工提前查看刀路轨迹,有效避免过切和撞机等风险的存在。
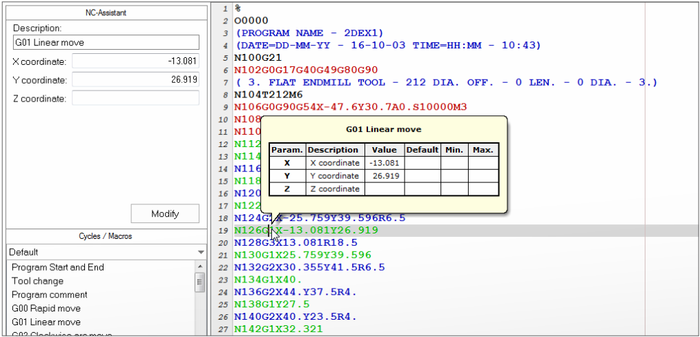
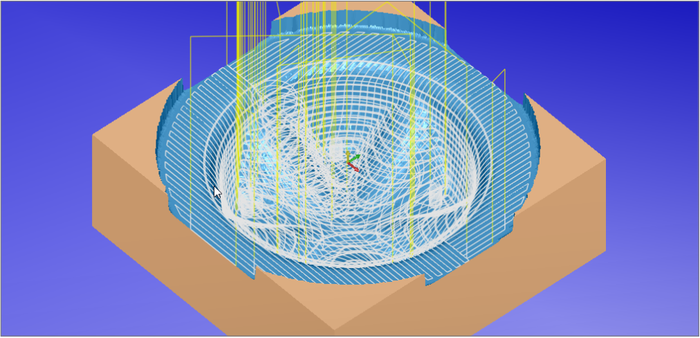
图1 EDIT可对手工或自动编写代码进行编辑和仿真
DNC机床联网/程序传输管理
通过机床联网,DNC系统完全支持Fanuc、Siemens、Heidenhain、MAZAK、三菱、OKUMA和HASS等各种控制系统,可对数控机床实现群控管理(图2),上传、下载程序,避免在机床和计算机间来回奔波,可节省大量的操作时间,并确保每次下载的程序准确而可靠,避免因为程序调用错误造成的加工质量事故。
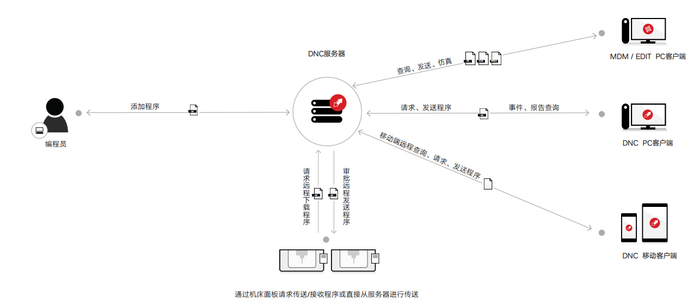
图2 通过机床联网可对数控机床实现群控管理
MDC生产数据采集
现有的生产数据采集主要依靠人工采集、输入的方式,管理部门通常在事后采集,输入到word或Excel表格中进行统计。数据的时效性会延迟,输入时的人工疏失会造成数据的可靠性降低。管理者无法准确的知道确切的机床开机率。登录MDC系统后,可以采集机床的生产数据,包括:
机床状态:机床开启、机床关机、机床空闲、机床故障和机床运行等状态信息,其中机床状态以程序运行与否作为判别方式;
机床加工参数:当前加工程序名、加工开始时间、加工结束时间、加工模式、进给倍率以及主轴倍率等;
机床报警和故障数据:设备报警信号、设备故障信息和其他有利于设备故障诊断的信息。
机床停机原因数据:通过条码枪或触摸屏的方式输入停机原因,准确知道机床停机的各类原因,停机时间,为管理者解决问题提供数据支撑。
采集后数据,根据公司的管理需求做相应的统计分析,如图3所示。
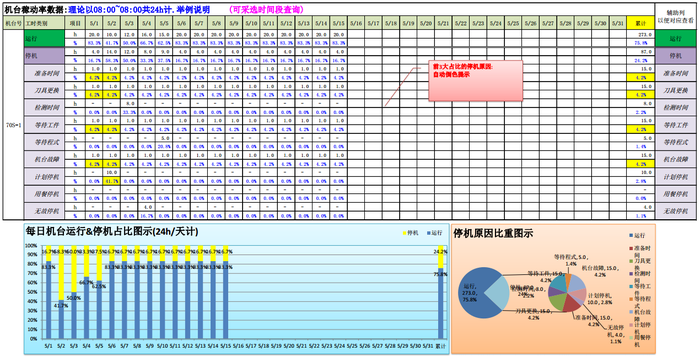
图3 数据采集后可根据公司的管理需求做相应的统计分析
MDM生产数据管理
在现有工作模式上,NC程序是按照程序名放在不同目录下的,有时同一程序又往往存在不同的版本,这样查找所需的程序就较为困难,并且容易出现程序调用错误的情况。MDM生产数据管理模块采用数据库管理方式,具有完善的版本管理功能,将所有相关的文档统一管理——数控程序、零件三维造型、工序图纸以及工装清单等工艺相关文档的集成管理,能够对Microsoft Office、AutoCAD、PDF、HTML、图片和UG、CREO三维图形文件等多种文件格式的关联管理。
MDM可准确快速地调用相应零件的程序(图4),自动跟踪并记录程序文件的所有变更,允许用户比较/恢复老版本,可靠保证操作人员调用最新版本程序。
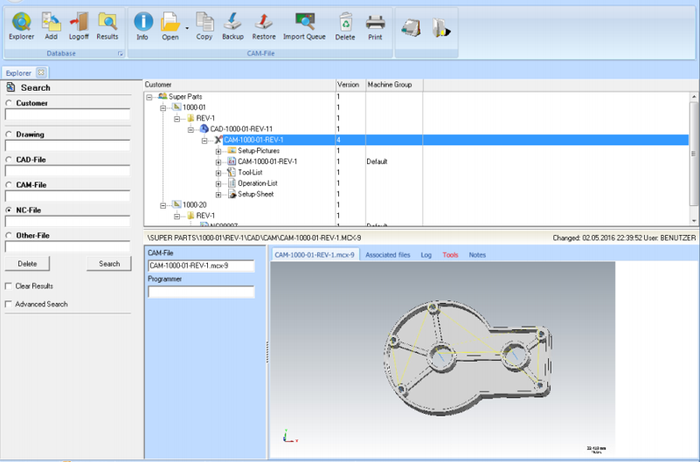
图4 MDM可准确快速地调用相应零件的程序
DNC/MDC/MDM数字化车间项目的实施取得了明显效果,减少了NC加工程序的出错率,缩短了程序传输的时间,实时而准确的数据采集为车间管理提供了有效的数据支撑,机床利用率大幅提高,为实现公司的智能制造奠定了坚实的基础。
评论 0
没有更多评论了