随着人力成本的上升及工业4.0的推进,国内外各行业正在推广无人化、自动化的生产和物流方案。在汽车行业内,随着自动化焊接等工艺的成熟,目前国内外整车厂将自动化进一步向上游推进,即解决零件取放的自动化,以推进解决生产过程中的无人化问题。
零件取放自动化包括自动化装箱和自动化取件两个方向,分别对应机器人将零件装入工位器具和机器人将零件从工位器具中取出。对于自动化装箱,如冲压零件的下线装箱,因受生产柔性、场地和质量等因素的影响,目前在国内主机厂尚未推广。但对于自动化取料,由于车身车间每个工位可以根据实际情况灵活布局机器人,对场地和生产柔性影响较小,尤其对于车身车间使用的冲压零件,以机器人取料代替人工取料,以解决人工拿取零件节拍高和人机工程不佳等缺点,是目前各大主机厂研究的一个热点课题。
自动化取件的成功率与零件在生产线旁的绝对姿态紧密相关。自动化取件历了两个阶段,第一阶段为机器人抓手采用固定轨迹从工位器具内抓取零件,由于机器人取件采取固定轨迹,对零件姿态要求较高,因此工位器具公差及零件在工位器具内的活动空间均较小,以防止零件在物流过程中的窜动影响零件姿态及抓件。因此固定轨迹抓件模式不利于工位器具制作和运作,成本较为昂贵。同时,在人工装箱的前提下,因零件可移动距离小,也不利于工人装箱,尤其是对高冲次冲压生产线的装箱,更是一个挑战。
第二阶段为机械手采取活动轨迹抓取零件,即自动化视觉抓件。机器人抓件抓手上集成摄像头,在视觉系统的辅助下从工位器具内抓取零件。其工作流程为抓取零件前,由摄像头先对零件特征点(一般选取零件尖角和销孔等易于识别的特征点)进行拍照并与视觉系统内零件的标准姿态值进行比对,引导机械手调整位置,从而实现对零件的抓取。与固定轨迹抓件模式相比,视觉抓件模式对零件姿态要求相对较低,对工位器具公差和零件间隙的要求更低,利于工位器具的制作和工人的装箱,因此带视觉系统的自动抓件模式目前应用较为广泛。
自动化视觉抓件工位器具的设计和制作
上汽大众从2016年起引入视觉抓件技术,目前已在各工厂主流车型上广泛应用(如柯珞克/途岳侧围外板、车顶和门盖,朗逸家族侧围外板/车顶,帕萨特/科米克家族车顶和门盖等),实现了取件人员的节约,部分工位彻底实现了无人化。
在定位工位器具的问题上,国内部分整车厂线边对工位器具进行定位,通常需要举升机构等设备,费用相对昂贵。与此不同的是,上汽大众采用线边机构对Dolly(用于运输工位器具并存放于生产线边的输送小车)进行限位和定位的技术,实现了成本的降低。本文拟对上汽大众机器人视觉抓件对应的工位器具(简称料架)设计、制作、运营及维护流程进行分析。此流程包括工位器具设计、样架制作、样架验证、批量制作及验证(含小批量)、运作和维护等过程,各程流程及注意事项如下。
1. 工位器具设计。工作流程为:公差定义→工位器具设计→工位器具数模匹配→图纸初步锁定。
公差定义:需要定义零件相对于地面的公差链,包括地面定位机构与Dolly的匹配公差(即Dolly相对于库位Dock,含Dolly制作公差),Dolly与工位器具之间的匹配公差,工位器具制作公差,零件在工位器具内的可移动距离等,图2为一般性公差要求(具体零件需视情况而定)。
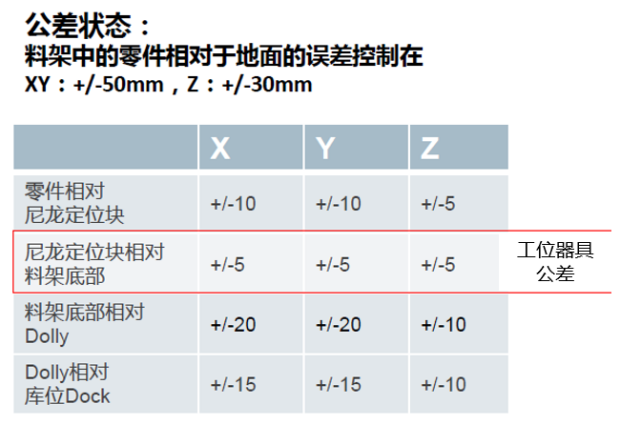
工位器具设计:工位器具设计时,除常规考虑零件的受力点、人机工程和仓储存放等因素外,还需考虑工位器具外框或结构件是否与机械手干涉,并设计契合的解决方案。部分工位器具还需考虑:抓取过程中,零件的防晃动措施,如图3所示。

工位器具内如有活动机构,活动机构需要增加是否打开的识别板,多车型共线生产时,增加多车型工位器具的区分感应板。同时考虑与Dolly的匹配方案等。王红磊等人也对车顶类自动抓料工位器具设计进行了研究。
工位器具数模匹配:工位器具数模设计完成后,需与Dolly图纸一道,由机械手进行抓料匹配测试,对公差和零件极限状况进行模拟,并视模拟结果进行设计修正,直到完全匹配,方可完成图纸的初步锁定。
2.工位器具制作和验证。
样架制作和验证:图纸设计完成后,供应商按照图纸进行工位器具样架制作,与常规工位器具相比,自动化视觉抓件工位器具制作完成后,除常规的验收外,还需增加工位器具尺寸测量及验收,以确保工位器具尺寸和图纸尺寸一致。
批量制作和验证:自动化工位器具图纸及样架验收完成后,开始进行批量工位器具制作,考虑到自动化工位器具对生产效率和设备的影响,我们在自动化抓件工位器具正式投入使用前,对每只工位器具均上线进行抓取测试,抓取成功后投入工位器具循环使用系统。
自动化视觉抓件工位器具的运营和维护
工位器具的运营:冲压工位器具是多部门使用,且存在诸如卡车、铲车、拖车或AGV驳运等多个过程,可能会造成零件窜动及工位器具损坏等,造成抓件失败。若抓件失败,需按照应急处理流程对抓件失败进行分析及处理,并报相关部门进行后续处理。
工位器具维护:如工位器具受到外力因素或定位件磨损等因素的影响,造成零件在工位器具中的三坐标尺寸发生变动,由发现部门对问题工位器具进行隔离,并标注问题原因,将工位器具退回物流主管部门,由物流主管部门通知维护供应商将进行维修,维修完成后供应商通过检具及测量,确保工位器具尺寸符合图纸尺寸要求后送货。上汽大众车身车间将对工位器具进行上线复测,复测通过后投入循环进行使用。
视觉抓件系统及工位器具发展方向
视觉抓件技术经过近几年的发展,视觉系统、抓手系统和工位器具系统等均发生了较大进步,目前可满足多种零件的自动化抓件需求。但由于视觉系统和抓手柔性还未能发展为无限制的抓取零件,目前视觉系统对零件还存在诸如不能打磨以免影响零件识别等要求,抓手对工位器具也还存在一定的公差要求。为更好的提升视觉抓件能力,降低成本,视觉化抓件需重点向以下三个方面发展进步:视觉系统的升级,提升零件的识别能力;抓手系统柔性的优化升级,做到无限制的抓取零件;以及满足视觉抓件工位器具的制作和使用的升级。
其中,要实现最后一个升级,首先要完成工位器具及配件的模块化和通用化;以及工位器具的3D打印化,提升工位器具制作精度的同时降低工位器具制作和维护成本。
上汽大众通过一系列的工作方法,对工位器具从设计、制作、运营到维护,进行全流程跟踪,从而保障了各车型自动化抓件的流畅运行。随着自动抓件设备及工位器具制作,应用技术的不断进步,设备及工位器具制作,维护等各项成本将逐步降低,预计自动抓件技术在车身车间将不断推广,无人化车身车间将不再遥远。
评论 0
正在获取数据......