机械加工技术市场竞争激烈。对于像ZSO这样的机械加工服务供应商来说,显然必须将质量、工艺可靠性和生产效率提高到最高水平,而这只有在流程持续自动化的情况下才能实现。为此,ZSO近年来在搬运系统和机器网络化方面进行了大量投资。在目前使用的35台加工机床中,有1/3已经实现了完全自动化。
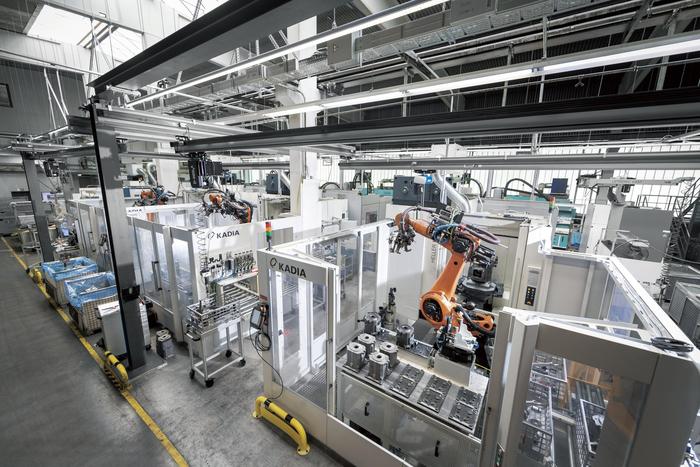
图1 KADIA的RHDC和ZSO加工中心一瞥。由于接口和周密的工艺设计,这两个工厂部分形成了一个完整的生产单元,并紧密合作
最近的一个项目对ZSO董事总经理Carsten Binder博士来说特别重要:搬运和去除重达26 kg的移动式液压泵的灰铸铁外壳。例如,这些泵用于工程机械的液压系统。壳体直接从铸造厂运到ZSO,在那里进行生产即可用于组装。
在之前位于Oberstaufen的公司内完成的自动化项目中,需要搬运和去毛刺的工件要小得多、轻得多,因此选择轻质协作机器人理所应当。然而灰色铸铁外壳太大、太重,不适合这种方式,因此员工们用手搬动和去除外壳的毛刺,这不是一件容易的事。
手工去毛刺也有一些缺点:每名工人的工作方式不一样,要从不同角度握住工具,并凭借各自的力量压住外壳边缘。当遇到难以够到的内部轮廓时,这是一道很麻烦的工序。另外,还存在手持工具打滑和损坏工件的风险。必须找到一种新的解决方案来更好地处理这些任务。“我们的计划是让机器人执行所有的重复加工,”Carsten Binder博士解释说,“去毛刺也可以在机床上进行,但机器人是性价比更高的解决方案。”
机床和机器人——一支完美的团队
在KADIA,ZSO终于找到了一个在重型工件全自动去毛刺方面拥有丰富专业知识的合作伙伴。不久经过短暂的时间,Nürtingen的设计工程师便提出了一个理念,令ZSO的经理倍感满意。即基于一个有效载荷为120 kg、行程为2.5 m的六轴机器人。KADIA客户可以完全获得一站式解决方案,这意味着供应范围包括工艺开发、机器人、单元、夹持器、去毛刺工位和拥有特殊解决方案的工具。当然,还少不了所有安全相关设计的序列化编程。KADIA在2019年4月交付了第一个自动化单元,9月交付了第二个,2020年1月交付了第三个。
该项目涉及将自动化单元连接到三台相同的Heller H5000加工中心(MC)上。ZSO公司已经陆续购买了几台这样的四轴机床,特别是用于生产泵壳的机床,已经配备了机器人接口。机器人将在MC周期内,即在大约20 min的时间窗口内完成机床的上下料和去毛刺工作。
由于需要两个夹紧装置,工件通过旋转台进给。壳体被夹持在由来自Oberstaufen的机加工专家们专门开发的夹具上,所有这些步骤还包括KADIA项目经理的大量编程和调整工作。此外,在外壳型号、夹具与夹持技术方面还需要与ZSO进行协调,并就机器人与MC的连接咨询机床和机器人供应商。现在,用户的努力得到了回报,因为机床和机器人单元作为完美的生产单元一起工作。所有相关人员之间的这种紧密合作在未来还将继续,例如当需要对新的工件型号进行编程时。
但是,去毛刺自动化单元到底有什么作用呢?最重要的步骤是:机械手一个接一个地拿起两个未加工的零件,并把它们放在夹具上进行第一次装夹。在加工过程中,夹持器将另外两个未加工的零件放置在剩余的空闲夹具位置,这样4个工件总是同时循环。第二台机器人夹持器用于第二次装夹。在工件放置之前,用压缩空气吹掉接触面上的切屑,以确保精确夹紧。机床以不断交替的方式完成第一次和第二次夹持设置。
一旦运行了两个设定的NC程序,机器人就会引导工件进行去毛刺。为此,KADIA根据外壳型号的不同,为该单元配备了3个或4个自主研发的带自动磨损补偿功能的毛刷去毛刺工位(图2)。外边缘和外表面使用圆形钢丝刷,孔和内轮廓使用特制的高强度长丝方刷。因此,可确保够到所有轮廓并完成去毛刺处理。
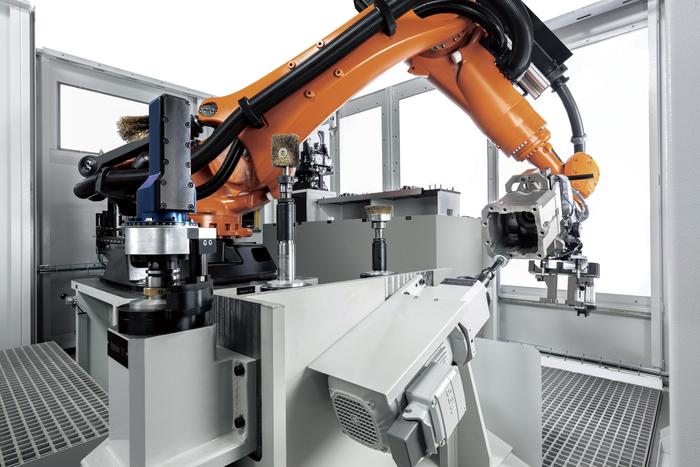
图2 根据不同的型号,机器人将加工好的铸件外壳引导到3个或4个毛刷去毛刺工位。前面的工位配备了一个宽大的凸出刷子,用于操作人员难以到达的深层轮廓
由于工件的洁净度对客户来说很重要,机械臂将去完毛刺的外壳放在清洗篮中,然后将其运出单元。该搬运已被作为下一道工序整合到自动化理念中。我们并非止步于此:每隔五个工件会做一次标记,以供质保部门进行检查。
流程复杂 操作简便
Binder列举了这个理念的优点。首先,最重要的是减轻了员工的繁重搬运工作。因此,与自动化之前相比,现在需要的人员更少。对于手工操作,每台加工机器需要一名员工。因此,一个三班制的操作,3台机器共需要9名操作人员。但是,由于实现了自动化,现在一个操作人员可以同时管理3个生产系统(MC和RHDC)。重要的是,操作人员无需特殊培训便能成为一名合格的机器人专家,因为KADIA和ZSO已就尽可能降低系统操作的简便性达成共识。“我们在理念中加入了‘回撤策略:初始位置’的选项。”KADIA的机器人和去毛刺专家Udo Frie解释说,“这允许操作人员在中断时随时将机器返回到初始位置,并从那里重新启动它。不需要机器人面板来完成这一操作(图3)。”
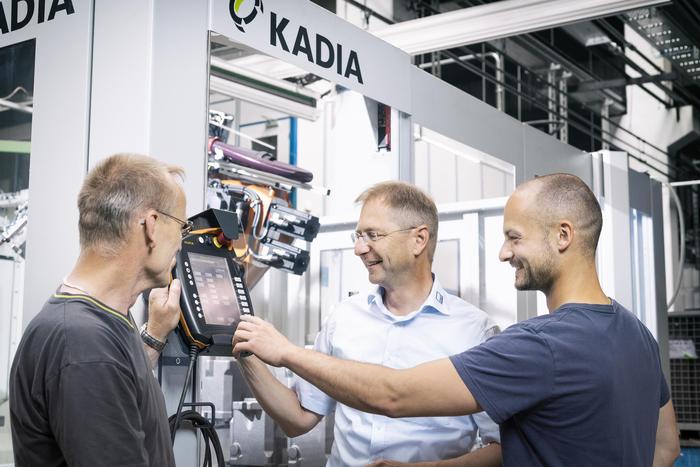
图3 负责整合位于Oberstaufen的ZSO的KADIA的去毛刺自动化单元。从左至右分别为: KADIA的机器人和去毛刺专家Udo Frie;ZSO董事总经理Carsten Binder博士;ZSO项目经理Michael Stark
ZSO的总经理继续说道:“对于我们的客户来说,重要的是我们能够在去毛刺过程中提高工艺可靠性,从而提高产品质量。如今所有的边缘都能根据客户的要求绝对均匀地完成去毛刺处理,但整个操作过程没有任何变化。此外,机器人永远不会忘记一个边缘或螺纹。这意味着,返工也成为过去。”这也适用于人工操作中永远无法避免的过程中断。“自动化消除了许多计划内和计划外的停机,出现生产工艺流程中断的情况越来越少,单位时间内产出的零件更多。”Binder确认道。KADIA的销售工程师Dominik Landhuer补充道:“显而易见,在去毛刺自动化单元的帮助下,机床的产量可以提高30%~50%,这取决于工件和要整合的工艺(图4)。”对于ZSO的董事总经理Binder来说,很显然需要沿着这条道路坚定不移地走下去:“未来,我们将在自动化解决方案的基础上引入每个新的客户项目。”
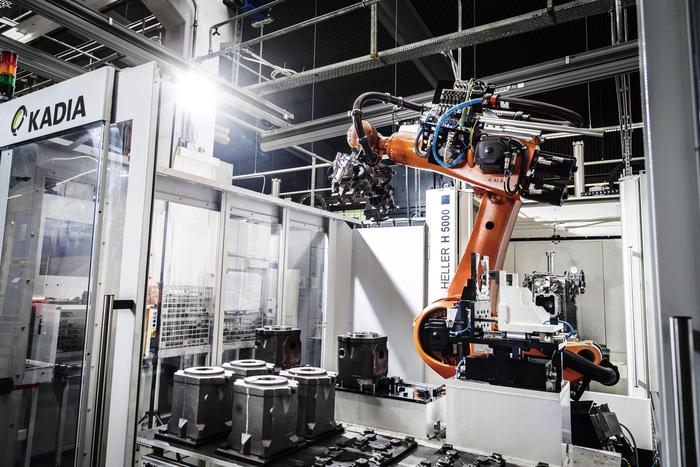
图4 KADIA去毛刺自动化单元内部一览。铸铁外壳装在托盘上,在加工中心进行双组加工
评论 0
没有更多评论了