整套模具是由多个模具零件装配而成,装配工作通常由人工完成。
当下,随着模具零件特征的日益复杂,制造工序随之增加,在多工序流转的过程中,管控模具零件精度的难度随之增大。
因此在整套模具装配环节中,需要先进行人工修模,而后再进行装配。
为了提高整套模具装配效率,高端模具制造行业已经形成了“只装不修”的模具零件加工方法:
通过减少工序流转 将模具做“精、准”以此来缩短整套模具的装配周期
北京精雕依托于粗、精、清根一体化加工理念和精雕“机内自动化”工作模式,将“只装不修”的模具零件加工方案应用于不同类型模具零件的加工中,包括整套塑胶模具、冲压模具的生产和装配。
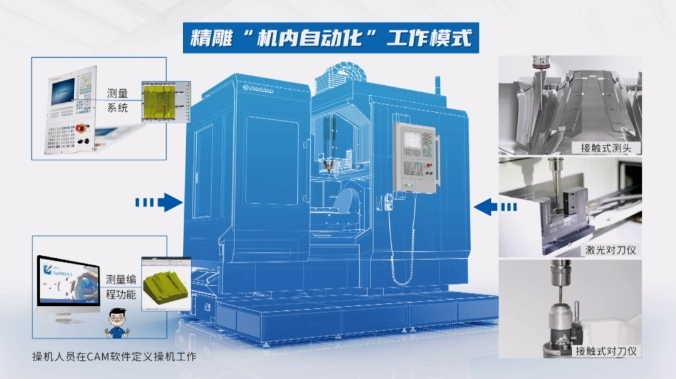
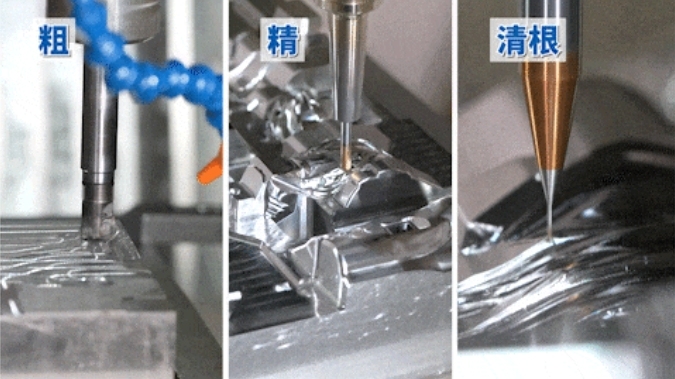
让我们一起看看该方案的应用情况吧!“ 只 装 不 修 ” 案 例
运动机构配合间隙小于20μm;
分型面精度±7.5μm;
产品面精度±10μm;
模具装配时间8小时;
加工出来的产品表面无飞边、无毛刺。
潮玩手办模具
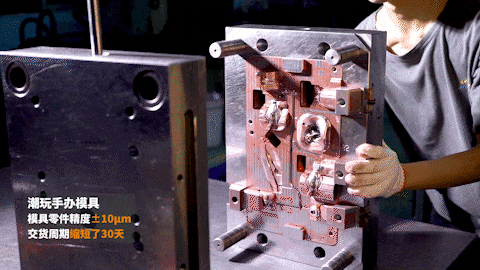
17套模具共计150个模具零件,模具零件精度±10μm,无需人工手工抛光,达到了“只装不修”的模具装配效果,模具品质稳定;
交货周期相较于行业通用方案缩短了30天。
笔记本外壳冲压模具
关键特征精度±10μm;
表面刀纹均匀一致,表面粗糙度Ra0.6μm;
装配用时4小时。
上述整套模具“只装不修”的效果具体的实现过程是什么?即刻为您解析!
在精雕精密数控加工中心完成模具零件的粗、精、清根一体化加工,减少制造工序的流转,实现模具零件精准加工。
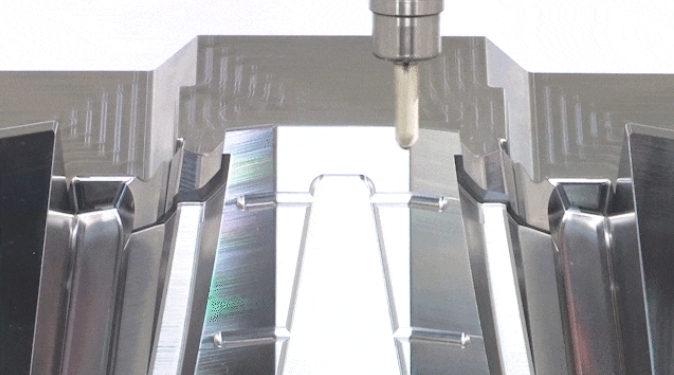
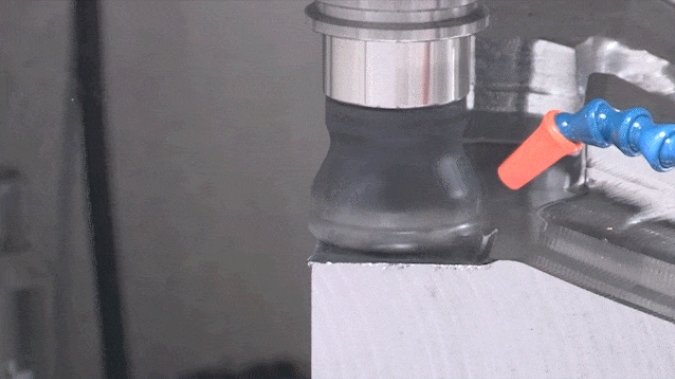
2、精雕“机内自动化”生产模式
北京精雕充分发挥自身机电软技术深度融合的优势,形成了一种“程序定义,机床自动实现调机、管控、加工、测量等工作”的精雕机内自动化生产模式。
在精雕机内自动化工作模式的支持下,人工仅需完成上下料和毛坯粗定位等基本操作,其它工作如:工件坐标系精准定义、刀具磨损及补偿、工件精度检测等,均在精雕CAM软件中进行定义,由程序驱动机床自动完成,减少人工干预,保证生产过程的稳定和设备运行的高效。
在精雕“机内自动化”工作模式的前提下,配合精雕供料系统或构建自动化加工产线,北京精雕还形成了“机加自动化系统”,分为自动化单元和自动化产线两种落地形式,实现了从模具毛坯进入料仓或料架开始,即可自动进行加工、测量和换料,不需要进行人工干预。
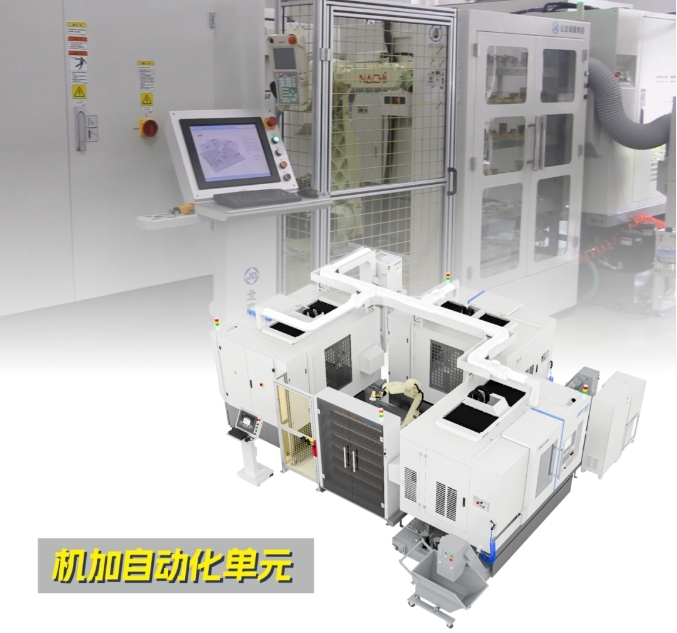
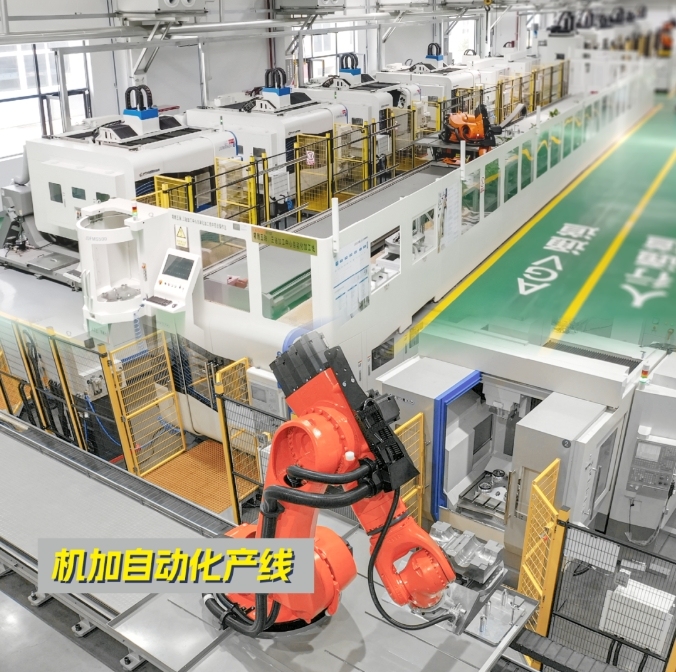
北京精雕在模具行业实现“只装不修”的加工方案你Get了吗?
北京精雕实现整套模具“只装不修”的加工方法,核心在于使用精雕精密数控加工中心完成模具零件的粗、精、清根一体化加工,减少制造工序的流转,并在加工过程中采用精雕“机内自动化”生产模式,将模具零件加工过程中原本需要人工完成的工作,如:人工试刀、人工打表分中、人工进行工件测量等等,均由机床自动完成,减少人工干预,保证生产过程的稳定和设备运行的高效。
在精雕“机内自动化”工作模式的前提下,配合精雕供料系统或构建自动化加工产线,北京精雕还形成了“机加自动化系统”,实现了从模具毛坯进入料仓或料架开始自动进行加工、测量和换料,不需要进行人工干预,有效提升机床稼动率。
文章来源:北京精雕
图片来源:北京精雕
转载平台:微信公众号
责任编辑:朱晓裔
审 核 人:李峥
评论
加载更多