实施生产自动化和数字化项目之前,公司应精简现有流程中,重点在于识别和消除工作流中的瓶颈,确保所有子系统有效运行。主要措施包括收集操作期间各个事件的最新准确信息,并上报负责人。若无法按此要求进行,则可能导致工作流程订单减少,起到相反效果。因此,创建“未来工厂”的第一个阶段是建立机器数据收集(MDC)系统,或者机器监控系统。如果部署得当,机器监控系统可降低公司成本、提高生产率,将公司的最低水平提升到一个新的档次。
监控系统的主要目的是跟踪设备运行,提高设备效率。以Zyfra的MCDplus监控系统为例,有效机器监控背后的原理早已浮出水面。虽然总部设在芬兰的软件开发公司Zyfra刚刚才入驻美国市场 ,但该公司已为200多个海外客户的6000多台机器提供实时监控服务。
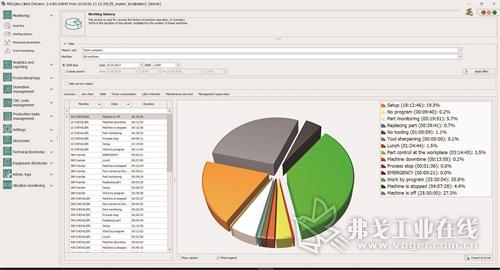
Zyfra的MDCplus系统的工作历史报告示例
和大多数系统一样,监控系统其实很简单。驱动器安装在现代数控机床上,提供关于机床状态变化的详细信息。原有设备配备监控终端和适配器,连接到CNC或机器的继电器梯形逻辑系统。硬件和软件代理负责收集关于机器操作和操作员操作信息,包括运行时间、停机时间、停机原因以及操作员在停机期间值班等。然后将采集的数据发送至服务器,由服务器软件进行分析,并将分析结果以方便易懂的形式呈现给用户。管理人员可根据结果报告,作出最佳决策,改善机器性能。管理控制通常分为三个层次。
第一层是为有效利用设备创造条件。例如,MCDplus能够对实际设备负载进行客观评估,确保工艺工程师和调度员能够识别工艺流程中遇到的瓶颈问题:工作时间损失、生产资源浪费以及过多设置或更改时间等。然后基于此类信息作出决定,消除妨碍生产过程顺畅流动的障碍,提高机械利用率。例如,精益制造技术可以更有效地应用于价值流。此外,这些措施可以提高工作站纪律,减少能量损失,优化维护部门运作。
第二层是控制生产过程,提高效率。管理人员可以将机器时间与特定操作联系起来,判断升级CNC编程技术、刀具、机上探测或其他变化是否能够提高整体性能。以MCDplus监控系统的结果为例,一般改进率为8%~12%。在该阶段还计算了整体设备效率(OEE)。
第三层是停机时间和计算机维护管理。在该层次上主要解决了两个问题:一是维护部门调度及时、有效,二是操作的有效维护和维修(M&R),要求在准确的时间,通过准确的方式准确修复问题。例如,MCDplus可以自动记录每次非计划停机事件。操作员在系统上对事件进行分类,然后向负责此类事件的服务部门发送通知。所有活动都反映在报告中,通过报告,管理层能够快速评估完成的工作,并在必要时,对特定事件进行彻底分析或对之后类似事件进行微调响应。通过这种方式缩短非计划停机时间,通过主动维护,提高设备使用寿命。
经验表明,智能M&R调度和现代规划方法可以将许多车间的非计划停机时间缩短10%~15%。
通过监测系统还可以有效解决过度功耗问题。机加工操作耗费的电力是会对生产成本造成强烈影响的因素之一。通过实时跟踪机器运行,监测系统帮助管理人员准确识别每台机器和员工消耗的电力,找到能量损失的原因。然后进行精确的用电规划,优化设备能源利用。将实际单位用电量和计划用电量进行比较,从而简化决策过程,将以基于累积数据的成本最小化。例如,可以将耗电量大的操作安排在公用事业费率很低的时段,比如夜间。
MDC系统功能和收集的数据可以用于解决各种生产管理问题。通过动态分析,公司经理或某生产部门负责人能够快速评估总体关键性能指标(KPI),以及任何单独车间、数控机床或特定操作员的KPI。可以跟踪随时间的变化,发现变化趋势和原因,并及时采取纠正措施。
简而言之,机器监控将推动公司效率水平再上新台阶,加速第四次工业革命(基于数字化和数据驱动制造)的到来。
评论 0
没有更多评论了