加工是增材制造(AM)之后修整金属部件的唯一方法吗?也许你会这样认为,但事实上,还有其他各种后处理技术,可以提高部件的表面精细度和尺寸完整性。此外,如果必须对增材制造(AM)部件进行加工,您可以选择利用固件和夹具固定部件方向,特别是复杂形状的部件;也可以在将部件从建造板上取下来时,建立部件的基准和参考点,辅助确定部件的朝向以及对齐与否。简而言之,通过这一系列的额外工作,可以帮助您快速发现使用增材制造(AM)带来的种种益处和优势。
金属增材制造(AM)部件加工最大的挑战就是从构建板上取下来时,容易出现表面不光滑现象。图1所示的晶格结构的特写就是一个最佳的例子。粘附在部件上的部分熔化粉末颗粒、逐层加工期间产生的阶梯效应、3D实体模型的镶嵌以及上表面和下表面的差异都会影响表面粗糙度。平滑这些粗糙的边缘和表面也增加了后处理的时间和成本,但是这对于满足规格和公差要求,特别是机械性能和疲劳寿命而言至关重要。
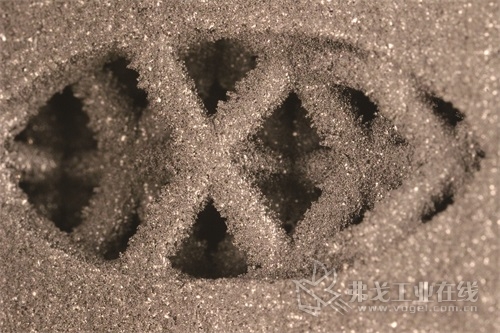
图1 Ti-6Al-4V晶格结构中部分熔融粉末颗粒的特写图
事实证明,有很多技术可用增材制造(AM)部件的修整和后处理。实际上,这些技术同样也适用于修整一切金属部件。增材制造(AM)并没有重写规则或重新定义物理定律,也没有否定安装在飞机上或植入人体内的部件必须满足的要求。我们依旧对公差、机械特性和成本竞争性提出要求,这跟其他制造过程相比并无差异。
那么,目前流行的增材制造(AM)后处理技术有哪些?比如采用砂、砂粒或陶瓷珠等磨料进行介质爆破是降低表面粗糙度较为简单方法,但其劳动强度大,难以确保对整个部件表面进行均匀和精确加工。再有,喷丸处理可以提高表面光洁度(图2),并且还可以在加工过程中发生塑性变形,改善部件表面的机械性能。还有,磨光适用于某一增材制造(AM)部件的特定部件处理(而不是像喷丸材料那样,对整个部件进行喷丸处理)。
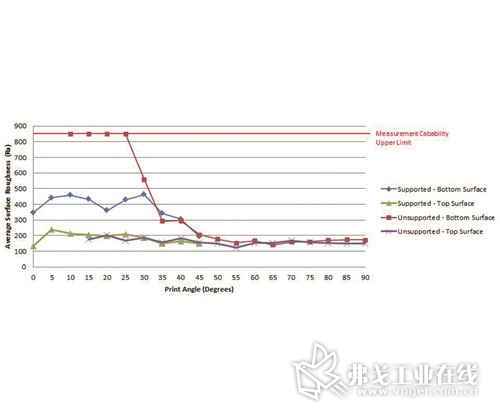
图2 具有不同外伸角度的不锈钢顶部和底部表面的表面粗糙度测量(喷涂后)
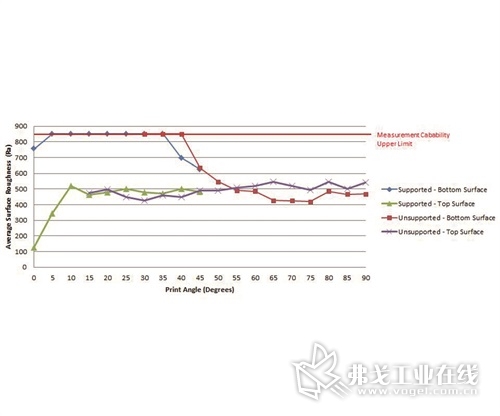
图3 具有不同外伸角度的不锈钢顶部和底部表面的表面粗糙度测量(喷丸强化后)
喷丸强化是一种冷加工工艺,而很多公司会选择激光强化作为替代。有趣的是,真正发挥作用的并非激光的热效应,而是激光脉冲产生的冲击波所引起的机械效应导致的塑性变形和表面硬化。事实上,研究人员正在试图将不同的激光组合成一个增材制造(AM)工艺,使用一种激光逐层熔化粉末,制造3D部件,然后使用另一种激光进行微加工和表面精加工。
振动抛光、滚光(例如滚筒抛光)和离心抛光(例如钻削)也是促使表面光滑的好方法,且无需借助任何特殊夹具或固件。与介质爆破和喷丸强化一样,这些工艺用于精加工外表面时效果良好,但是在进入内表面和通道内存在很大限制。为了克服这一困难,表面精加工技术如磨料流加工(例如挤压珩磨)开始采用含有磨料颗粒的粘性流体去毛刺,抛光内表面和通道。
电化学抛光或蚀刻可以替代磨料抛光。通过电流刺激化学蚀刻剂平滑和处理金属部件的内表面和外表面。该工艺相对便宜,且容易控制,但在处理蚀刻剂和废品时要特别小心。
抛光和超精加工工艺也可以用来精加工金属增材制造(AM)部件。例如,各向同性超精加工,因能够使表面光滑并同时提高其性能(例如耐腐蚀性和耐磨性),开始在增材制造(AM)界引起更多关注。
在上文介绍过程中,还有其他选项我没有列出,但是我十分希望大家能够从这些文字中感受到增材制造(AM)界现在正在使用和研究哪些技术来进行后加工处理和表面精加工。请大家记住,在选择后加工技术时,应当以成本有效性、可控性、可重复性和适用于内外表面为基本要求。该过程无需特殊固件、夹具或工具,无论是处理一个部件还是上百个、上千个部件,设置和清洗时间都应降至最低水平。为了提高下游操作,增材制造(AM)界可谓做到了“耳听八方”,如此才能坚守“复杂即是自由”的信条。
评论
加载更多