2014年,贵州西南工具(集团)有限公司(以下简称“西工”)牵头,联合北京航空航天大学、贵州黎阳航空动力有限公司(以下简称“黎阳”)和厦门金鹭特种合金有限公司,共同承担了“航空发动机机匣加工国产化成套刀具产品开发及应用”课题,目标是,实现国产航空发动机机匣加工用数控刀具的国产化和自主化,扭转高端刀具长期依赖进口的被动局面,提升航空发动机机匣零件加工的制造水平和生产效率。课题起止时间为2014年9月至2017年12月。
围绕课题任务,西工首先考察了黎阳,现场了解了机匣的结构特点和加工特性,经过反复研究讨论,确定了机匣加工所需的刀具种类和刀具性能,并据此分解了任务并拟定了责任目标,下发给课题各合作单位。根据任务分解目标,西工主要围绕用于高温合金及钛合金机匣加工的整体硬质合金刀具(包括铣刀、钻头和铰刀)而展开研究。
针对黎阳某型号高温合金机匣和钛合金机匣,结合机匣加工特性,西工成功地研制出81款整体硬质合金刀具,包括:用于钛合金机匣加工的39种立铣刀、9种钻头和8种铰刀,共计56种刀具;用于高温合金机匣加工的16种立铣刀、4种钻头和5种铰刀,共计25种刀具。
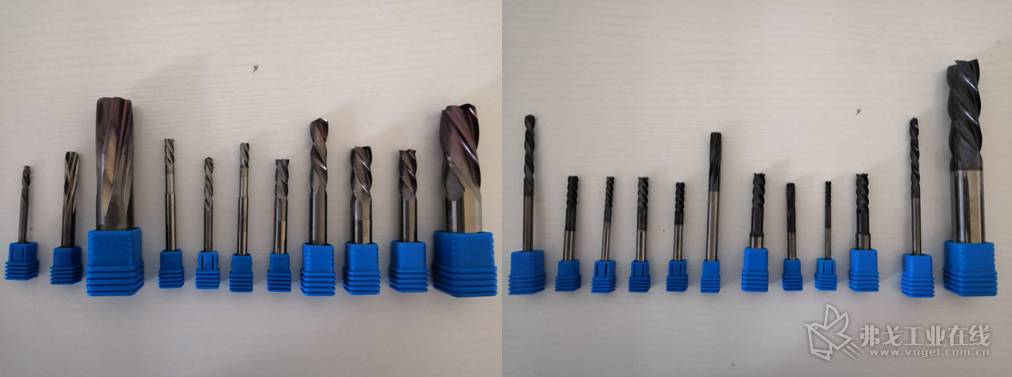
图一西工研发的部分刀具示例
开展的研究及突破的技术瓶颈
机匣属难加工材料薄壁复杂结构件,不仅切削加工余量大,而且工艺要求高,特别对精度的要求极高,因而对整体硬质合金刀具提出了更高的要求:不仅要求刀具具有较高的切削性能,而且要求刀具刃部直径公差0.02mm,径向跳动5μm,形状精度5μm,钝圆半径误差不大于15%。
为提高刀具使用过程中的切削性能和效率,西工对高温合金及钛合金刀具分别开展了有针对性的研究,包括:
1.不等分、不等螺旋角涂层合金立铣刀的研究
为了减少切削过程中刀具振动,采用了不等分齿和不等螺旋结构。适当的前角、后角和螺旋角的匹配,在保证刃口和刀尖强度的同时还降低了切削阻力。螺旋周刃上设计有保护韧带,增强了刃口强度,延缓了刃口的磨耗失效。合理的结构设计及优选的几何参数,在很大程度上保证了刀具的使用寿命,达到了提高加工效率和加工质量的目的。
2. 圆弧型钻尖合金钻头的研究
钻头钻尖部分切削刃的内刃和外刃均采用了圆弧型过渡,降低了实际钻削过程中的钻削阻力,同时,切削刃上设计的负倒棱增大了刃口强度,一定程度上延缓了刃口的破损和剥落,后刀面采用直线形式的后角,减少了与工件之间的接触摩擦,再加上各主要部位合理的参数设计,这些有利因素共同确保了实际切削过程中钻头的耐用度,特别是在钻削高温合金等难加工材料时,性能表现更为优异,最终可满足高效钻削的要求。
3. 高效整体硬质合金铰刀的研究
采用优化后的径向前角、径向后角、螺旋角及倒角等几何参数,在保证铰刀刃口强度的同时,还提高了切削稳定性。倒锥刃上设计的圆柱韧带增强了刃口强度,延缓了刃口的磨耗失效,降低了切削振刀,从而达到提高刀具使用寿命、加工精度以及表面质量的目的。
在课题实施过程中,西工进口了国外高端数控工具磨床,但国外对其核心磨削软件系统进行封锁,不仅无法进行二次开发,而且配套的刀具磨削软件总是以高额或捆绑或限制的形式销售,导致刀具的制造成本较高。基于此,西工基于包络原理建立了成套整体刀具磨削路径数学模型,开发了自主磨削软件和刀具三维设计软件,并研制出与之匹配的五轴联动工具磨床,力求具备“自主磨床-自主材料-自主刀具-自主涂层”的全流程机匣加工自主化的能力,彻底解决我国航空发动机机匣的加工难点,并为公司的后续发展及服务化转型奠定基础。
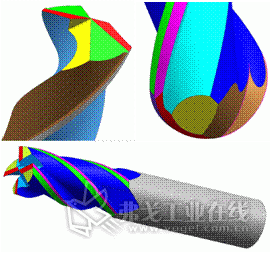
参数化设计的钻头、球头铣刀和立铣刀三维模型
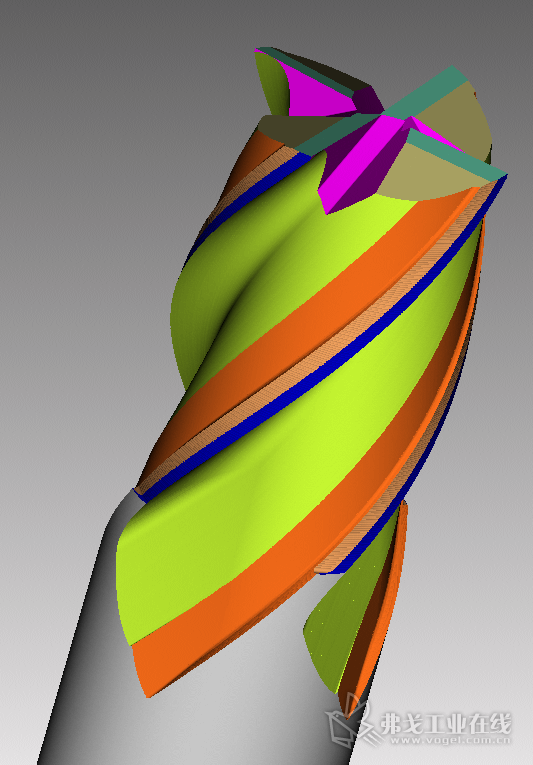
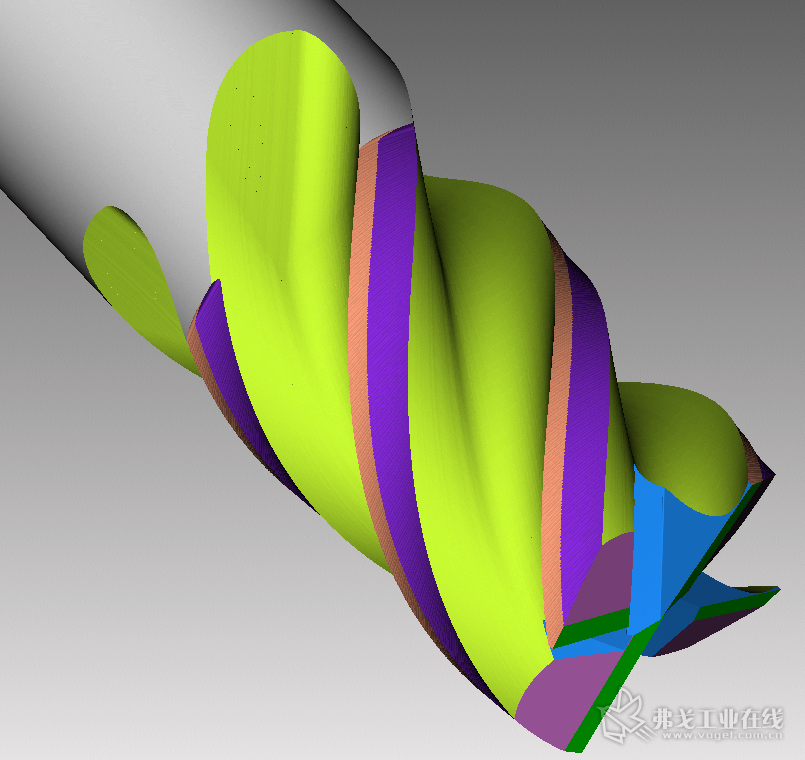
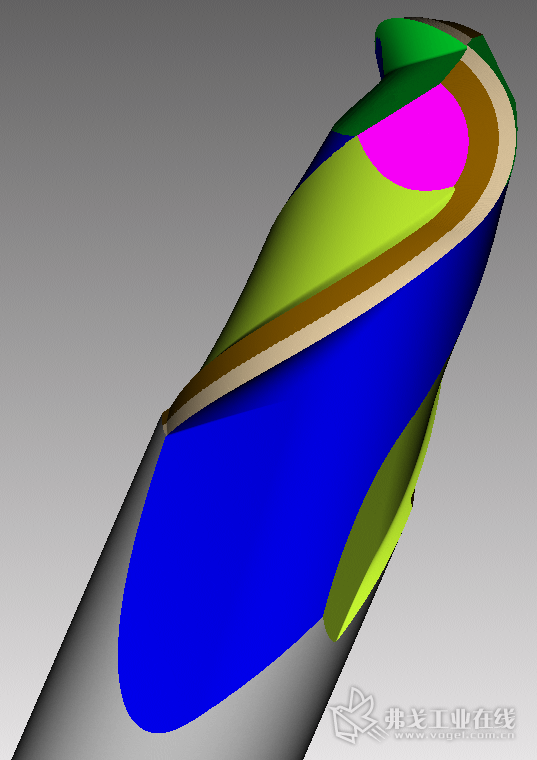
NC程序磨削仿真的立铣刀、成型槽立铣刀和球头铣刀
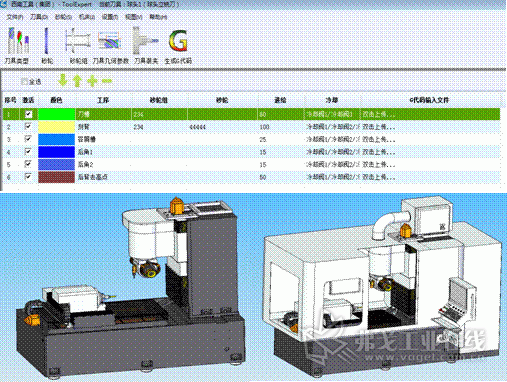
自主研发的磨削软件和五轴联动工具磨床
实际应用情况
由于课题所研制刀具的加工对象是航空发动机机匣零件,此类零件属涉密产品,因此在课题研究时,一方面要确保完成研制任务,另一方面还要确保不泄密,由此而给研制工作带来了诸多不便。
在航空发动机机匣的研发中,对工艺作出改变需要非常谨慎,首要的是要确保产品质量的可靠性和稳定性。因此,在项目开发过程中,完成了技术开发并不意味着就能大规模的推广应用,还需要大量的、长期的技术验证和试验过程,最终才能推广应用。
目前,西工为机匣研制的刀具以及衍生的刀具已在黎阳、中航湖南通用航空发动机有限公司、沈阳航空制造有限公司和南方动力有限公司得到实际应用,不但用于加工机匣零件,还用于加工小型发动机的叶片、叶盘和叶轮等零件,部分取代了瓦尔特和山特维克等进口高端刀具,从而推进了航空发动机机匣刀具的国产化和自主化进程,为国家重大工程航空发动机制造技术的全面进步助了一臂之力。
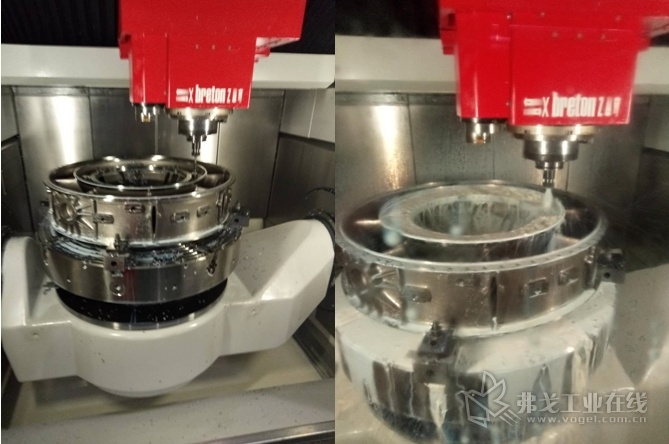
课题研制的刀具在生产现场实际加工机匣
整体研发能力、人才队伍建设和管理的提升
自课题实施以来,西工着力打造了现代刀具事业部,专门组建了高效刀具技术研究所,成立了贵州省高效切削技术工程研究中心,构建了一支高素质的专职研发队伍,显著提升了公司的研发能力和技术保障能力。
同时,引进了德国瓦尔特、萨克工具磨,德国磁粉钝化机、砂轮修整机,奥地利刀具三维测量仪等设备,组建了一条高质量的现代刀具生产线。
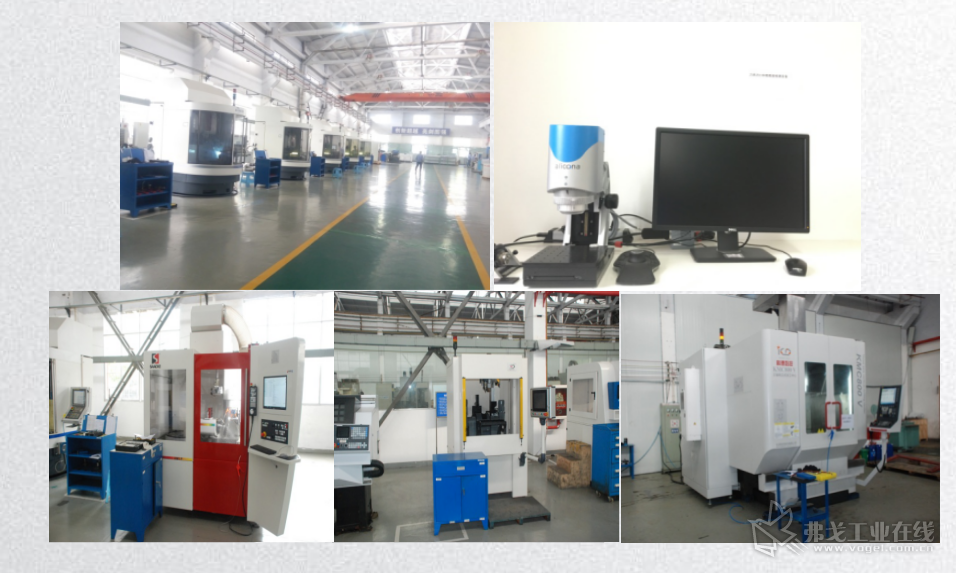
西工建立的刀具生产线及部分设备
通过课题研究,西工规范了自身管理,加强了与各成员单位的合作和交流,并获得了大量宝贵的试验数据和研究基础资料。为妥善保存这些原始技术资料,西工还借助信息化手段,建立了档案数据库。
取得的经济效益和社会效益
2014~2017年,西工成功地开发了81款镍基高温合金及钛合金系列刀具,实现了此类刀具产品的国产化和自主化,目前产能已达50000件/年,产值超过2000万元,税收超过100万元。
通过课题实施,西工掌握了设计、制造现代高效刀具的关键技术,完善了高温合金、钛合金等难加工刀具的制造工艺,形成了相关技术和工艺标准,逐年提升了所生产刀具产品的稳定性和可靠性,产品品质和为客户提供的服务获得了广泛好评。
尚存在的差距和尚待突破的技术
目前国内整体刀具的设计和制造系统基本依赖于国外,国内尚未研发出成熟稳定的刀具设计制造系统。
第一、刀具模型种类不完善,与国外相比尚存差距。目前西工已开发出应用最为广泛的立铣刀、钻头和球头铣刀,其他种类的刀具尚处在研发之中。
第二、磨削系统更多处于研发阶段,与国外成熟的商业磨削软件相比,功能单一,仅局限于简单刀具,离商业化目标存在一定距离。
第三、缺少高端数控工具磨床,高端复杂刀具依赖国外进口工具磨床。西工2019年4月,自主设计开发的五轴联动工具磨床样机已组装完毕,目标是首台样机的精度达到国外成熟机床的90%以上。
因此,目前尚待突破的技术包括:
1. 锥度铣刀、成型铣刀等磨削路径数学模型。
2. 磨削软件中需要嵌入刀具加工碰撞检测及实时仿真画面。
3. 高端复杂刀具的生产制造。
2019年5月中旬,将完成机床的调试、试加工工作。刀具模型的继续开发、磨削软件的迭代以及机床的后续优化工作已在同步进行,预计2020年第一季度将推出拥有自主知识产权的国产商用五轴联动数控工具磨床。
一些建议
一方面,五轴数控工具磨床是加工整体硬质合金刀具的必备装备,由于我国尚未开发出成熟的刀具磨削软件,因此在此技术领域长期受制于人,希望国家能够重点支持这项技术的开发,突破国外技术封锁,提升我国刀具的制造工艺水平。
另一方面,航空发动机的切削加工技术是一项复杂的系统工程,需要多年的技术沉淀,希望国家持续支持高性能数控刀具、切削机理、工艺应用软件和切削数据库等方面的研究工作。
评论 0
没有更多评论了