在电控高压共轨领域,随着排放的升级以及为满足发动机节能的实际需求,燃油喷射压力变得越来越高。目前,主流喷射压力已达1600bar,更高压力的燃油喷射系统也将陆续推出,如2000bar、2500bar。
在电控高压共轨燃油喷射系统中,存在需要对微孔流量进行精密控制的零件,常见的有阀组件、油嘴偶件等。通常,需要将微孔流量散差控制在±1%以内。微孔加工一般采用电火花机床进行成型加工,然后采用液体挤压研磨机床对微孔流量进行精密控制。一般情况下,用进口电火花机床 (如posulax)加工的零件,其微孔流量散差在±2%左右,国产设备加工的零件,其微孔流量散差在±4%左右。
电火花加工完成后,在进行液体挤压研磨之前,要测量初始流量。为提升加工效率,通常采用按流量分组的方法,即将加工前流量相近的一批零件分入一组,然后再进行液体挤压研磨加工。液体挤压研磨加工完成后,采用中压清洗机对零件进行清洗,然后应用流量测量机床对最终流量进行复测。
传统的加工工艺路线较长,涉及到的设备也较多,而且为了保证加工精度,一般还需要对流量进行分组,导致整体效率较低,生产过程管理难度较大。
常用的微孔流量控制工艺及设备
在电控高压共轨领域,需要对微孔流量进行控制的零件包含阀套、油嘴等。为便于描述,以下以阀套零件的加工为例进行说明。
阀套零件存在两个微孔:进油孔和回油孔。通常,在测量压力10MPa、测量油温40℃的工况下,回油孔流量为350ml/min,进油孔流量为300ml/min。阀套零件微孔的流量控制工艺如图1所示。
在图1中,对阀套零件微孔的加工依次为进油孔研磨、清洗、进油孔测量、回油孔研磨、清洗、回油孔测量和数据记录。用于研磨和测量的进口设备有美国EXTRUDE HONE、德国Sonplas,国产设备有无锡宏申KYM研磨设备和ZGL测量设备,清洗工序可采用通用中压清洗机。

图1 阀套零件微孔流量控制工艺流程图
在此加工过程中,存在如下几个特点:
1. 工序间必须设置一定的在制品;
2. 数据记录以纸质为主,或者无记录;
3. 辅助工序较多,导致占用人工较多;
4. 工序间质量数据难以共享。
多工位微孔流量控制机床的研制
当前,以阀套为代表的微孔零件需要有更高的加工精度和效率,而传统的加工工艺难以在质量、效率和成本上同时达到良好的预期效果。为解决这一行业难题,提升工艺及制造水平,在“高档数控机床与基础制造装备”科技重大专项的支持下,开发了多工位微孔流量控制机床。机床集成了两组含研磨、清洗和测量在内的共计6道工序,同时集成了视觉读码、机器人上下料功能,研磨精度达到流量值的±1%,整机综合节拍为35s。
1. 多工序集成
传统加工工艺工序分散,工序间需要有定量的在制品,工序间的质量数据也难以共享,存在大量的重复、低效工作。如果能将图1中的工序集成在一台机床上全部加工完成,可有效解决上述痛点问题。
多工序集成的难点在于:
(1)不同工序间工装夹具的统一;
(2)多工位连续运转的准确定位;
(3)多工位的连续运转形式。
阀套微孔流量控制涉及进油孔研磨、进油孔测量、回油孔研磨、回油孔测量和清洗等5种不同的工装夹具。研磨工序和测量工序可以方便地得到统一,即新设计的工装夹具必须能够兼容进油孔研磨测量、回油孔研磨测量和清洗这3种工序。
在多工位连续运转的准确定位上,选择凸轮分割器解决这一问题。当运转到固定分度时,分割器存在一定的间隙周期,在这一周期内,即使因电机惯性有少量的旋转,也不会影响集成工位的运动。
在连续运转形式上,选择回转式工作台,这种结构能最大程度地节省空间,同时减少连续运转带来的累计误差。
如图2所示,采用回转式8工位工作台可实现含研磨、清洗和测量在内的全工序集成。工位依次是:机器人上下料、进油孔研磨、清洗、进油孔测量、预留、回油孔研磨、清洗和回油孔测量。
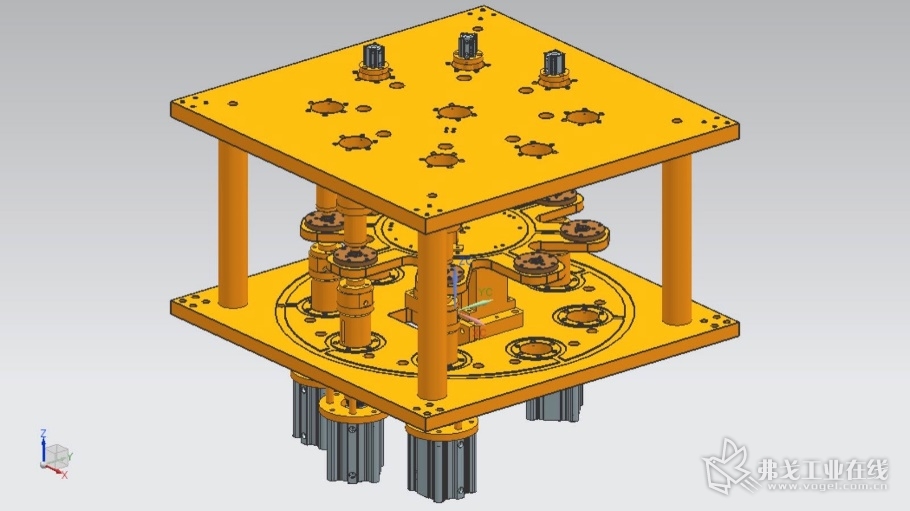
图2 回转式8工位工作台
多工位集成主要解决了两个问题:不再需要工序间的在制品,且工序间的质量数据得到了共享。
2.机器人上下料
随着机器人价格的不断降低,生产企业为减轻劳动强度、提升生产效率,将机器人广泛用于上下料。
多工位微孔流量控制机床工作台的工作半径是500mm,标准节拍35s,按照1h上下料一次计算,设计了100件/盘的标准料盘,同时,采用NACHI MZ04作为上下料机器人,机器人上下料单循环时间12s,如图3所示。
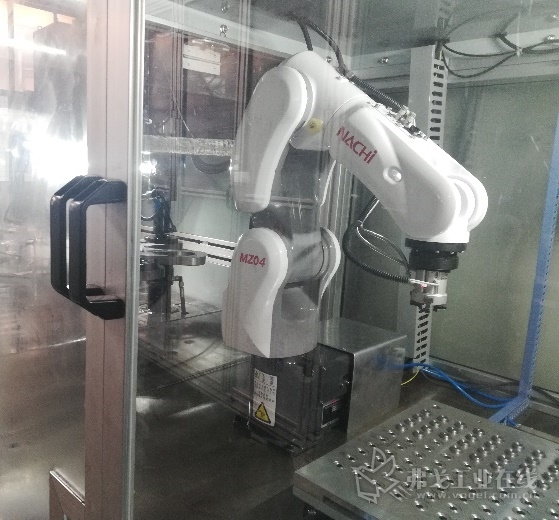
图3 机器人上下料
3. 视觉读码
在阀套零件的生产中,一般会在锥面上进行激光打码,以作质量追溯。多工位集成已经具备了微孔流量控制所有工序数据共享的基础,所有数据都可以记录在同一控制器中。利用视觉读码功能,可以方便地将所有的质量数据和阀套零件的身份码数据集成在一起。
多工位微孔流量控制机床采用康耐视Dataman 300读码器对阀套二维码进行识别,同时将信息集成到机床控制器中,如图4所示。
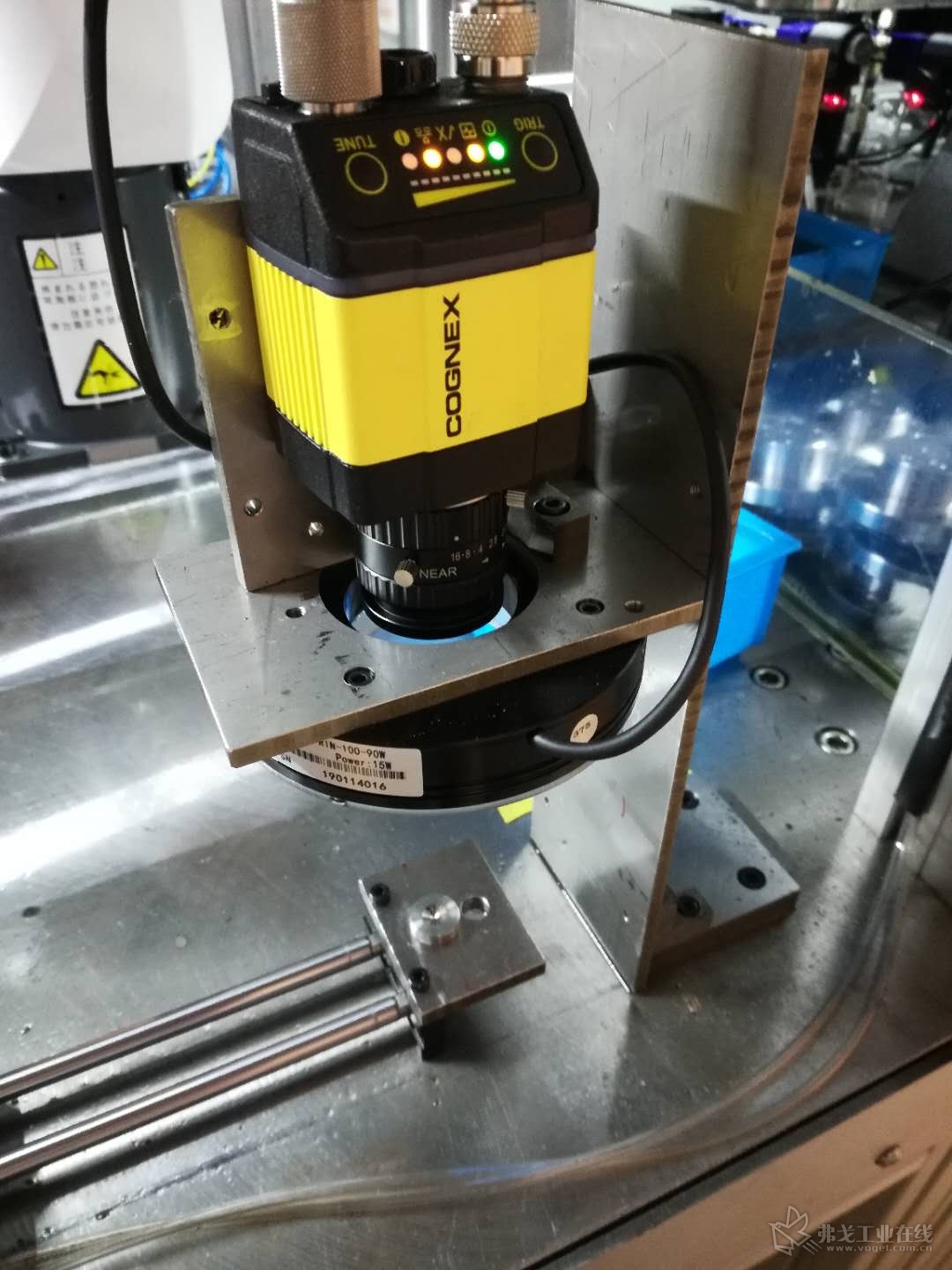
图4 视觉读码
在图4中,阀套二维码尺寸为1.5mm×1.5mm,采用Dataman 300视觉读码器,可以做到识别率不低于99%。读码成功后,将零件身份信息传至机床控制器,即可实现零件身份信息与质量数据的全关联。
4. 比例研磨
在某些特定的应用场合,要求阀套的进油孔流量与回油孔流量存在一定的比例关系,如图5所示。
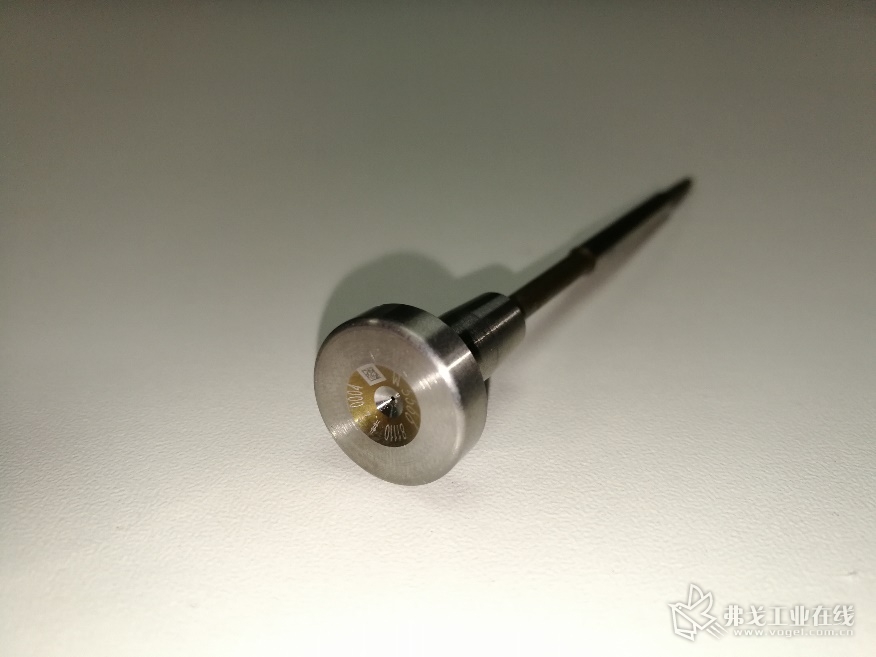
图5 比例研磨
在多工位微孔流量控制机床中,零件身份信息、各工位的质量信息都集成在同一控制器中,从而可以方便地实现比例研磨功能。比例研磨可作为一个工艺选项,按照工艺需求,决定是否使用。
机床精度与效率分析
1. 精度验证
多工位微孔流量控制机床的加工精度主要体现在研磨精度和测量精度两个方面,现以阀套回油孔加工为例予以说明。如表1所示,多工位微孔流量控制机床的研磨精度散差可控制在±0.8%以内。
表1 研磨精度

2. 效率验证
多工位微孔流量控制机床的综合节拍为所有加工工位的最长节拍与回转台旋转节拍之和。机器人上下料为单独的一个工位,当其他工位进行加工时,机器人也同时执行上下料动作,不额外占用工作节拍。对机床所有工位的加工节拍统计数据见表2。
表2 机床综合节拍统计表

由表2可见,多工位流量控制机床的综合节拍约为33s,按照100件/料盘计算,换料周期约为1h,即产能为100件/h。
3. 整机效果
如图6所示,多工位微孔流量控制机床整体分为4个部分:
(1)主机部分,含研磨系统、清洗系统和测量系统;
(2)工作区,含8个工作工位;
(3)机器人上下料区,含机器人上下料系统和视觉读码系统;
(4)主控柜,含电气控制相关设备。
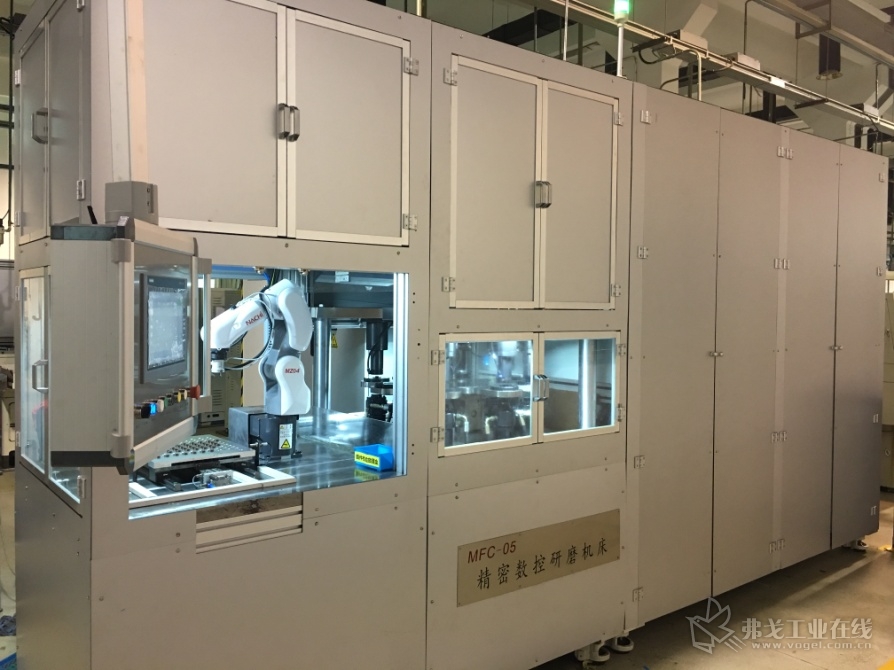
图6 多工位微孔流量控制机床
结论
多工位微孔流量控制机床的研制成功,有效地提升了电控高压共轨领域微孔加工的工艺水平,提升了加工效率和加工质量。其主要特点是:
1. 8工位同时加工,综合节拍35s;
2. 微孔流量控制工艺集成在一台设备上完成,无需工序间在制品;
3. 应用视觉读码技术,可将零件身份数据与质量数据完美结合起来,储存在数据库中,供后道工序或质量追溯使用;
4. 应用机器人上下料技术,可大幅降低工人的劳动强度,同时保证产量。
评论 0
没有更多评论了