近年来,信息技术与制造业的融合带来了新的发展机遇,传统的制造业也在发生着重大的变革,工业发达国家为抢占先机,大力发展以人工智能、工业机器人、大数据和云计算为代表的先进技术,相继提出“工业互联网”、“工业4.0”等国家战略,力图巩固制造业发展优势,制造业的智能化升级已成为全球发展趋势。数控机床作为制造业的“母机”,其开放性和智能化水平,决定着智能制造的下限,而数控系统作为数控机床的“大脑”,是替代人操控指挥机床实现自动化加工的专用计算机,也是数控机床实现高效率和高精度自动化加工的核心关键部件,同时也决定着“母机”的聪明程度。本文以科德GNC61系列数控系统在智能制造生产线中的应用为例,简要讨论关于数控系统的智能化(图1)。
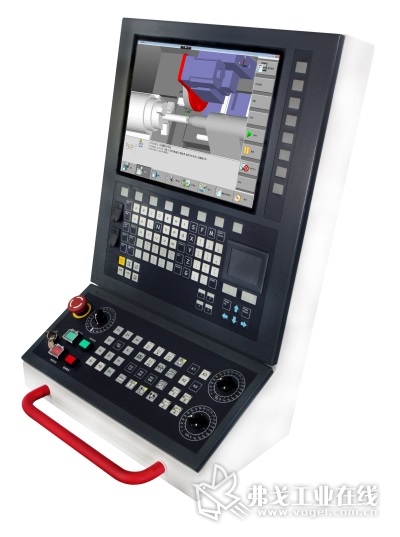
GNC61数控系统面板
科德GNC61数控系统的智能化功能
GNC61具备多轴多通道控制能力,重点提升了数控系统的五轴控制技术、伺服驱动的动态响应、几何误差补偿能力;增加了系统三维在线切削仿真和三维防碰撞功能,拓展了系统的人机交互能力;提供了更为方便的对刀方式和刀尖点坐标显示;提供了更便于数控程序调试运行的手轮速度功能,进一步增强了数控系统的开放性。
开放的数控系统:可面向用户多层次的开放,包括扩展的宏指令,并且支持自动程序运行中的手动干预。GNC61开发了内嵌于数控系统中工件测头标定功能、对刀仪标定功能、用户手动对刀功能,设定坐标系功能等;还支持用户开发各种不同的用于数控装置的人机操作接口软件,实现产品的差异化竞争。
操作的简单化和智能化:内置三维显示支持将轨迹和采集的数据绑定,通过不同颜色显示不同的物理量数据,便于将零件加工结果与采集的数据综合图形化进行分析,进一步提升表面加工质量。三维在线切削仿真和三维防碰撞功能,一方面方便用户在加工前进行程序检查,另一方面支持加工中的碰撞干涉检查,避免对操作者和设备的损坏。
加工过程的智能化:系统提供无线测头,可以自动进行坐标修正和工件检测,激光对刀仪可以进行刀具测量和补偿。同时功率自适应功能和各种参数优化功能都可以提高加工效率,延长设备寿命,保障加工精度。
管理维护的智能化:通过高速光纤运动控制现场总线,将数控系统的控制指令送达每个伺服驱动装置,并将包括机床各坐标位置、负载率和温度等物理量传回数控系统。同时还可以通过网络接口将系统中的各种数据(刀具信息、设备状态和加工程序等)传递给上位机进行建模分析和存储。
GNC61数控系统在智能化生产线中的应用
科德数控的一家客户使用GNC61数控系统,组建了一条生产机床零部件的生产线,该产线主要生产能力是由5台五轴立式车铣复合加工中心构成,集成了光洋自主研发的高度自动化的机器人系统,完备的仓储和装载系统,成熟的刀具及夹具等工装设备的管理系统,先进的机内外测量系统,通过先进的产线管控系统整合成一套自动化生产线(图2)。在该产线中,GNC61数控系统主要提供以下功能:
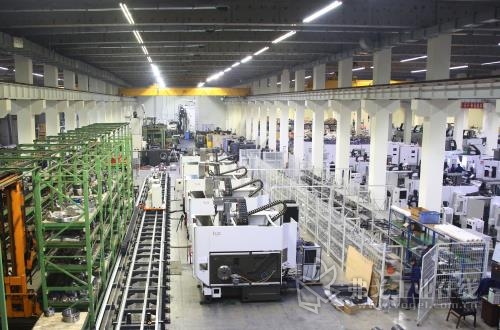
生产线布局
数据采集与分析。数控系统在机床运转过程中不断产生大量的实时数据,如运动轴状态:电流、位置、速度及温度等;机床运行状态数据:温度、振动、PLC、I/O、报警和故障信息;机床操作状态数据:开机、关机、断电及急停等;加工程序数据:程序名称、工件名称、刀具、加工时间、程序执行时间及程序行号等;感器数据:振动信号和声发射信号等,这些数据可以通过工业以太网传递给上位机系统,进行监视和分析处理。
机内自动检测。按照加工工艺要求,按照数控程序指令,通过无线测头自动获取零件实体位置的机械坐标。同时,还可以通过机内对刀仪,实时在线检测刀具磨损和破损情况,并实时的进行刀具补偿,保证加工质量。
加工误差补偿和测量再加工。将测量结果反馈到管控系统当中,管控系统调用几何误差分析算法根据测量数据进行实体状态与理论状态的差异性分析,根据产品理论要求制定差异性修订策略(除一次成形加工工序外);将差异结果反馈给数控系统并自动执行再加工,直到达到符合产品要求为止。处理过程分为3种情况:满足工艺要求结束此工序,准备进行下一道工序的加工;尺寸误差太大无法修正,确定为作废,结束任务;尺寸误差在可控范围内,可以进行修正。
功率自适应。数控系统自动根据主轴电流的变化实时优化进给倍率等工艺参数,实现对加工效率的提升和加工质量的明显改善。同时将实时采集的电流负载,编码器反馈,以及阈值,反馈到产线管控系统当中,进行优化学习,达到自动进化的目的。
扩展传感器的接入。丰富的传感器等智能工具被嵌入到机床装备之中,通过数控系统对所采集的、实时的传感数据进行网络上传,有效分析,提前预知设备状态及健康情况。
故障诊断和推理。当诊断信息传输给管控平台之后,平台故障诊断中心利用特征提取(将检测得到的数据进行分析处理,去除噪声和冗余信息,强化和提取故障特征信息)、模式识别(将待检测模式和标准模式进行比较,通过预设好的判别函数和判别规则明确所属类别),故障树法(采用逆向推理,分析给定时间可能导致的各种时间序列原因,定性定量的分析评估)、模糊控制等一种或多种诊断推理技术进行诊断,最终分析故障原因。
数控系统的智能化要求和发展
智能化数控系统是智能制造的核心,传统的数控系统相互间无法兼容也不开放,整体环境相对闭塞,不利于智能化的发展。对于数控系统的发展,科德数控认为应当更加开放化、集成化与模块化。智能化数控系统需要更多智能化软件、开放的数据采集及数据处理模块,这就需要打破现有数控系统的封闭,开放融合更多的功能,如在线检测、在线仿真、加工模拟、互联网大数据分析、远程指令加工、远程诊断维修及自适应排产加工等,一个开放性的设备控制平台才能支持组建功能更全面的生产制造系统,同时让数控系统成为智能制造的基本“神经元”,在制造系统中可以实现更多的信息采集与自主处理,以支持整个制造系统的自组织和学习进化。
随着控制技术、信息技术及人工智能的不断发展,数控系统的智能化将成为数控机床的必需功能,将逐步解决替代脑力劳动问题,包括自主工艺规划,自适应的加工管理和维护等,在不久的将来,数控机床将具备真正的“智慧”,实现真正的“智能制造”。
评论 0
没有更多评论了