“载人航天器结构关键制造装备及柔性化生产线”课题(编号:2014ZX04001-171)自2014年1月开始实施,至2017年12月结束,历时3年。通过对航天器结构关键制造装备及成套技术与集成制造系统进行开发,建设了一条载人航天器结构单元化柔性生产线,满足了我国航天器结构高精度、高可靠、长寿命和高效率的制造需求,形成了适应航天单件、小批量和小子样研制的具有航天特色的生产模式,具备了年产3~5套、同时在研5~6套载人航天器结构的生产能力,满足了我国未来10~15年载人航天器的研制需求。
关键技术突破
依托“高档数控机床与基础制造装备”科技重大专项(以下简称“04专项”)课题“载人航天器结构关键制造装备及柔性化生产线”,以载人飞船平台、目标飞行器平台和空间站平台等3类产品族的结构特点和研制技术流程为基础,针对制造过程存在的蒙皮类零件成形尺寸精度低和大尺寸蒙皮成形困难、空间站平台研制过程中关键结构的寿命要求等问题,研发了精密冷/热成形、焊接和装配等4台/套关键制造装备,重点突破了大型铝合金蒙皮类零件精密成形、宇航弱刚性壳体产品精密焊接以及航天器管路柔性制造等关键技术。同时,对电火花线切割成形/加工机床、高功率三维激光焊接/切割机床这两类专项成果进行了示范应;开发了一套集成制造系统,并将其示范应用于载人航天器柔性高效生产线中,最终建成了一条适应载人航天器三大类结构产品的单元化柔性生产线。
在对数控超塑胀形装备及技术的研究中,开发了具有加热、气体胀形配套系统的大尺寸精密数控液压超塑成形设备,以及超大尺寸液压平台系统和高精度滑块调平控制技术,突破了大平台多区控温及温度均匀性协调控制技术,设计并制造出适应加载曲线的自动气压加载系统,形成了压力、温度与气压的协同集成控制及优化方法;掌握了多维度启闭式加热保温系统(与液压机联动)的设计与制造技术,形成了滑块运动模式下加热装置高温密闭性的综合实现方法,开发出大台面、高精度平台及温度均匀性良好的成套超塑成形设备。
数控超塑胀形装备
在对弱刚性壳体-法兰预置应力对称热源自动化焊接装备的研究中,从焊接过程机理出发,深入研究了铝合金复杂薄壁壳体在预应力作用下,柔弧等离子焊接应力的变形规律,开发出柔弧等离子焊接电源、控制系统和工艺技术,在此基础上,研制出复杂壳体结构柔弧等离子焊接预应力工装,对模拟件进行了验证,最终形成了集成自动化设备、工装与相关焊接工艺的规范,并获得自主知识产权。
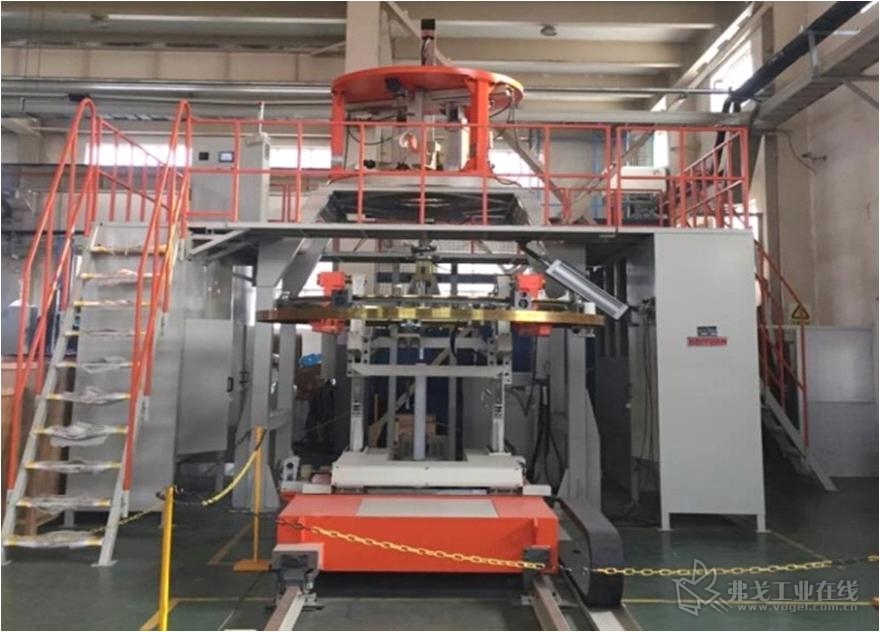
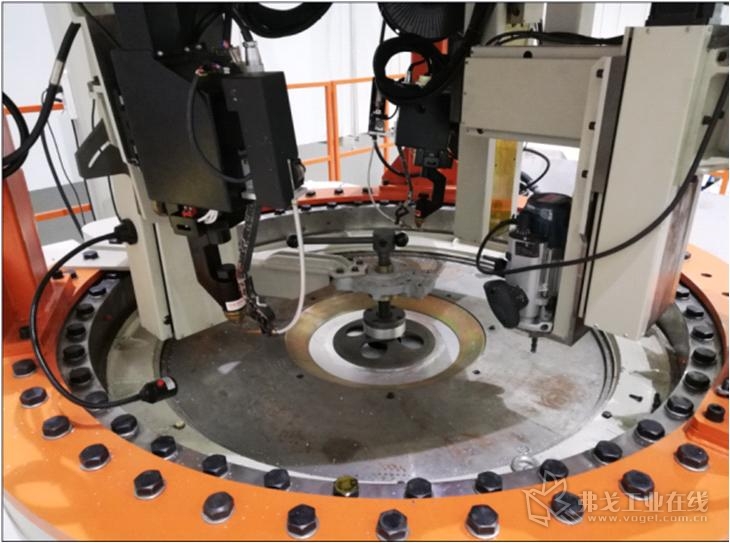
预置应力对称热源自动化焊接装备
在航天器管路数字化柔性集成制造装备研究方面,实现了完全以航天器管路模型为依据的管路模型管接头空间位姿数据的快速提取、相对坐标转换和工艺信息流传递;突破了高精度数控弯管机滚轮弯曲和滚转弯曲及其集成技术,实现了导管的高精度制作,并建成一套虚拟装配仿真系统,优化了装配过程和工艺参数,实现了管路系统快速、高效焊装的闭环控制。
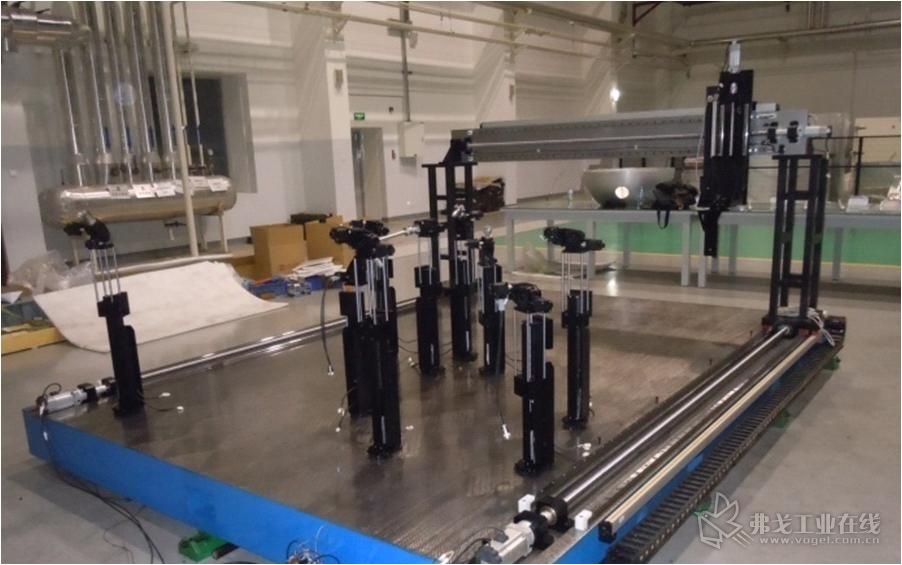
管路自动化柔性装配平台
在航天器高强度复杂零件铣削/挤压数控复合加工装备与工艺方面,开发的大跨度铣削/挤压数控复合加工机床,融合了高速精密切削加工与重载挤压成形,具有大跨度轻量化龙门、随动工装平台、高速铣削和重载挤压等功能,以及加工轮廓反求、加工质量在线检测与控制的特点。研究过程中,突破了大跨度轻量化龙门机床的精度控制技术、随动工装结构设计与控制技术、高速铣削和重载挤压成形技术、加工轮廓反求与加工质量在线检测与控制技术等。
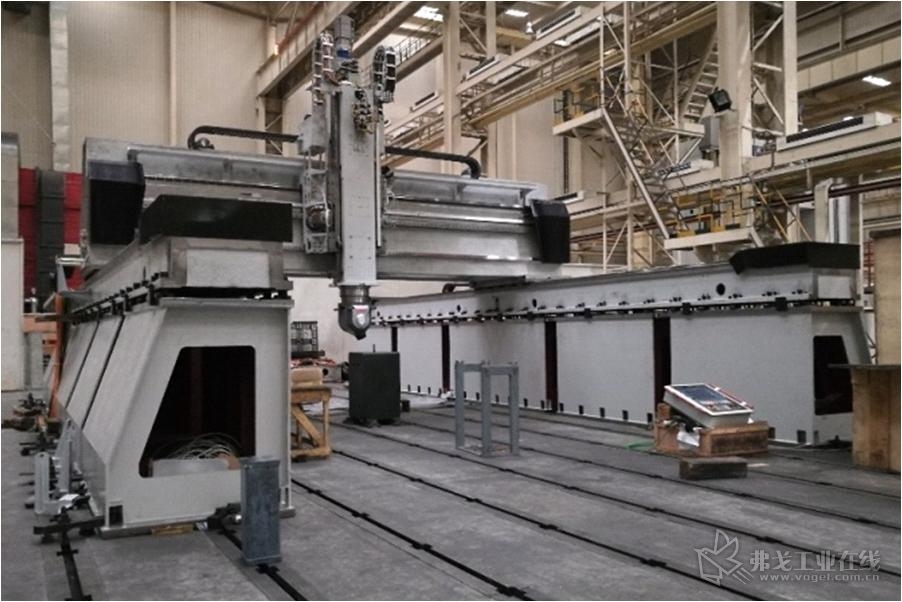
航天器高强度复杂零件铣削/挤压数控复合加工装备
依托04专项,北京卫星制造厂有限公司完成了对“精密、高效、数控单向走丝电火花线切割机床”和“五轴联动精密数控电火花成形加工机床”这两类专项成果的示范应用。通过工艺技术研究,令装备在航天器机构用小模数精密齿轮和空间相机准直器的加工中得到示范应用,完成了对航天器热控结构、探月取样薄壁结构的激光精密焊接,以及对蒙皮壳体的激光三维切割,形成了精密线切割工艺规范和航天器结构精密激光焊接与三维激光切割工艺规范。
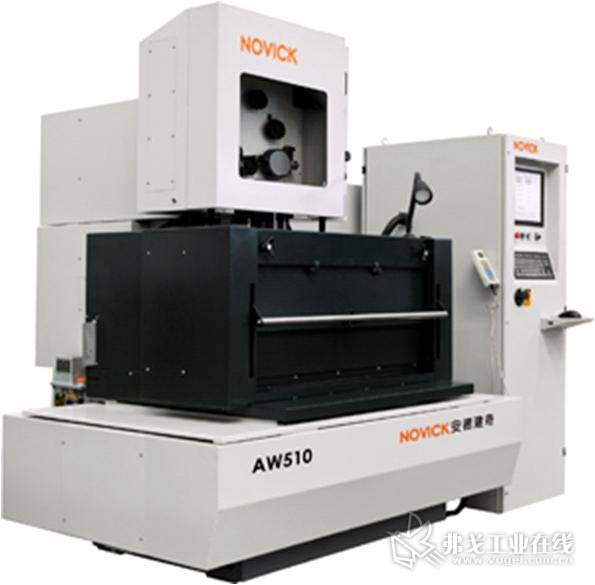
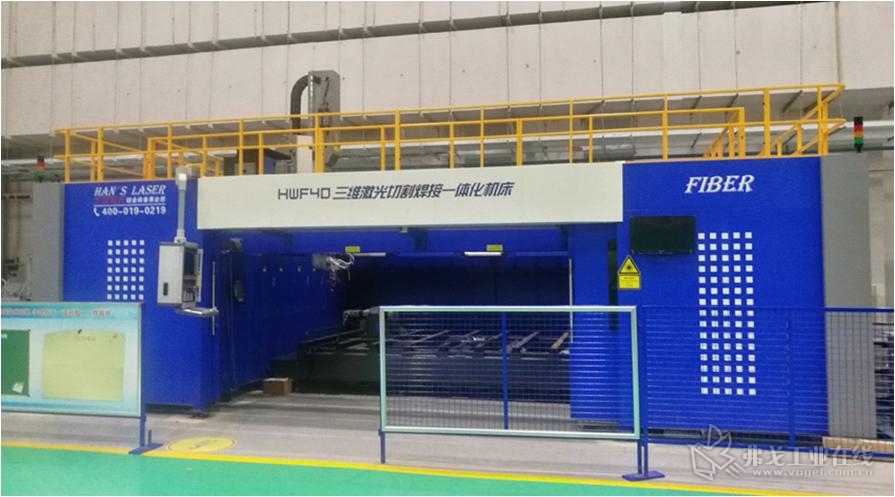
安装于北京卫星制造厂的电火花线切割机床和三维激光焊接切割一体机
在课题实施期间,形成了一系列具有自主知识产权的涉及载人航天器关键成形、焊接和装配的成套软硬件技术,申请专利13项(含一项软件著作权),发表论文10篇,形成企业技术标准10项(含2项五院院标)。
典型应用
依托本课题建成的载人航天器结构关键制造装备,以及柔性化生产线中的精密冷/热成形、焊接和装配等关键设备,均已服务于神舟飞船、空间站、货运飞船和嫦娥系列等多型号、多类结构产品的高精度、高质量和高效率研制。其中,数控超塑胀形装备及技术已用于载人航天某型号球底蒙皮的研制;航天器高强度复杂零件铣削/挤压数控复合加工装备与工艺已应用于空间站多舱段防护结构的精密成形;薄壁壳体与法兰预应力自动焊接相关工艺装备和工艺技术,同时在探月工程嫦娥五号返回器金属大底的研制中获得应用;航天器管路数字化柔性集成制造装备已用于QS-3、TT-1、GF-2、JB-11、BD-2A(MEO)和CE-5等重要型号的推进系统管路研制,使空间飞行器的管路制造从传统的手工模式以及依赖于舱体仪器设备的实物取样,改变为独立完成的全过程数字化制造模式,从根本上提高了管路系统制造的响应速度,为后续日益增长的型号任务提供了必要的技术保障。

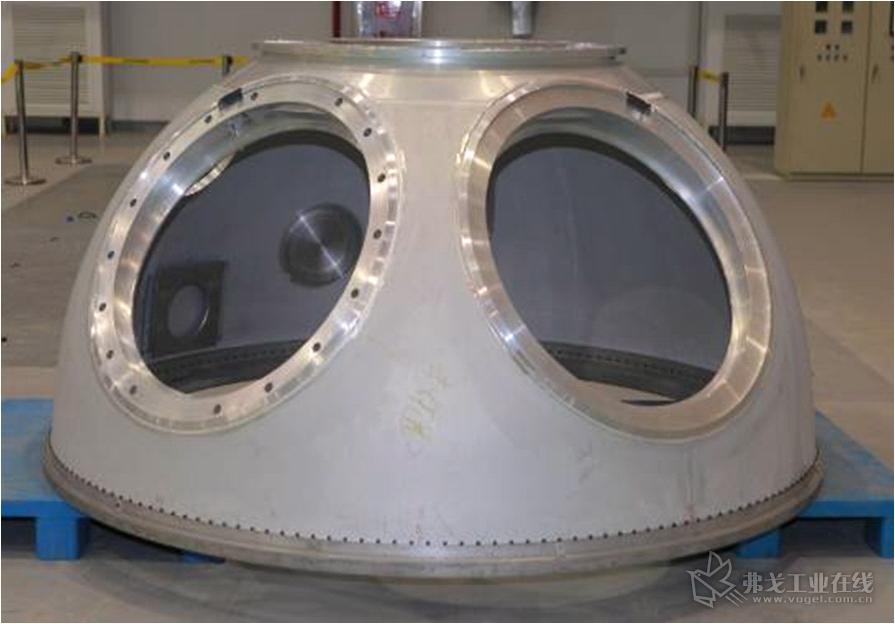
球底蒙皮零件超塑成形应用和返回舱球段法兰预应力焊接应用
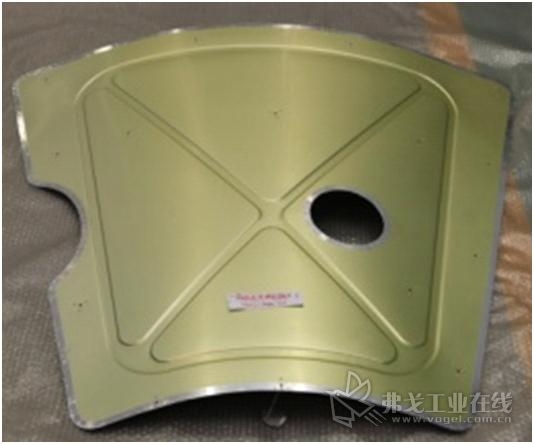
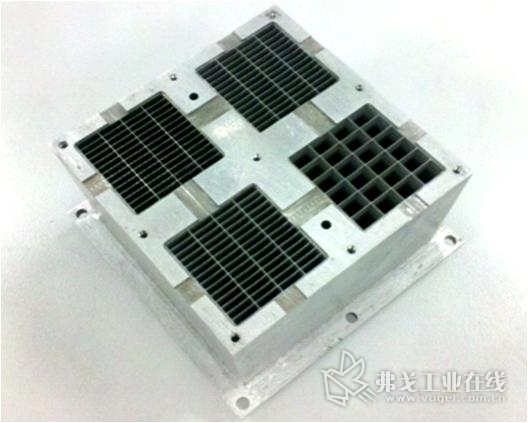
空间站某舱段防护结构复合成形和栅格类准直器电加工实物
研发能力的提升
载人航天器结构关键制造装备及柔性化生产线采用硬件装备与软件装备的建设方式,全面考虑了系统柔性、设备柔性和工艺的适应性,在总体建设模式和生产模式上均实现了创新和升级。柔性生产线的建设同时适应了航天器产品的要求、材料的特性、工艺的特点和管理模式,显著提高了载人航天器研制的技术水平,大幅提升了企业服务于航天建设的能力,有利地推动了航天关键装备制造领域及相关行业的技术进步。
本课题所研制的载人航天器关键成形、焊接、装配装备及成套技术指标处于国内领先水平。其中,数控超塑胀形装备为亚洲最大,铣削/挤压数控复合加工装备打破了国外封锁,预置应力对称热源自动化焊接装备填补了国内空白。通过本课题的研制,显著提升了北京卫星制造厂有限公司和参研单位在关键装备研发与集成方面的开发能力和市场竞争力,打破了国外在先进航天制造装备方面对我国的封锁和限制,建立了高端装备制造的研发平台和人才培养基地,促进了我国高端制造装备的跨越式发展,提升了我国航天装备的制造水平和加工能力,实现了我国高端制造装备、特别是高端自动化设备的国产化。
课题研究成果还为装备制造业的高效生产提供了装备、技术和工艺基础,通过成果转化和示范应用,使示范企业有效提升了对引进技术的消化吸收和再创新能力,促进了装备制造业的技术进步。
课题成果的应用直接面向航天器结构制造业,大幅提升了我国航天器结构制造的技术水平,以及航天产业的研发水平和应对危机的能力。在北京卫星制造厂有限公司形成的航天器关键制造装备及柔性化生产示范线,对于航空、船舶等铝合金结构制造带来了示范效应,引领了我国高端装备的未来发展,社会效益十分显著。
评论 0
没有更多评论了