工程技术领域的跨国公司雷尼绍联手两大创新技术公司力证:对于制造质量轻巧、接近人体骨骼机械特性的脊柱植入体,金属增材制造 (AM) 技术手到擒来。在该项目中,爱尔兰的一家制造工艺研究组织 — Irish Manufacturing Research (IMR) 公司 — 设计并制造了一系列具有代表性的脊柱植入体。IMR公司首先使用nTopology公司的软件设计植入体,然后在雷尼绍RenAM 500M金属增材制造系统上制造该植入体。
背景
IMR公司的总部位于都柏林,其宗旨是为爱尔兰众多制造企业提供全方位支持,帮助它们应对正在到来的数字制造时代。医疗产品制造业是爱尔兰的支柱产业,IMR公司一直在与众多合作伙伴研究如何应用3D打印医疗产品。
nTopology公司是一家行业领先的创成式设计公司,总部位于美国纽约。nTopology针对先进制造工艺开发了一款新一代设计工程软件。利用这款nTopology原创软件可以生成以性能为导向的复杂设计,以充分发挥增材制造工艺的优势。
利用nTopology的软件生成先进的设计只需短短几分钟。用户可以通过nTopology软件平台获取工程设计流程、制造工艺和专业知识,然后根据其具体要求创建自定义工作流程。
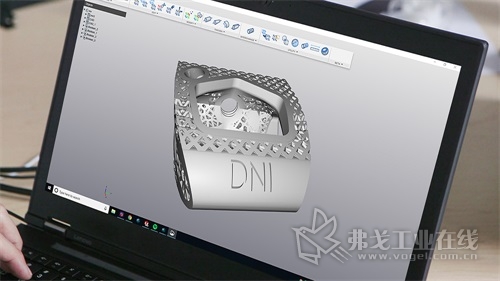
nTopology Element软件生成的网格设计
脊柱植入体用于为罹患退行性椎间盘疾病、椎间盘突出症、腰椎滑脱、椎管狭窄、骨质疏松症等多种疾病的患者恢复椎间盘高度。
网状结构可以增加植入体的表面面积,促进成骨细胞迁移到植入体中,并且能够优化多孔体的机械特性以满足所需的负载条件。但是传统的生产工艺无法制造具有网状结构的脊柱植入体。
IMR公司发现金属增材制造工艺适合制造网状结构,有助于优化骨整合。但是必须先确定最合适的设计软件和增材制造机器。

“增材制造技术的硬件能力发展迅速,现在已经甩开了传统设计工具一大截,”nTopology的业务开发与合作关系总监Duann Scott解释道,“几年前,市场上没有任何软件能够设计用于增材制造的复杂几何形状,于是我们瞄准这一市场空白,在2015年成立了nTopology公司。”
Scott继续说道:“要顺利完成从设计到制造的完整增材制造流程,硬件和设计软件必须有效协作。在制造脊柱植入体时,将设计文件从软件上简便地传输到增材制造机器上尤为重要,因为任何多余的中间环节和格式转换均有可能导致出现错误和误差。”
解决方案
雷尼绍、IMR公司、nTopology公司三方精诚合作,采用增材制造技术制造具有网状结构的颈椎植入体。该项目制造的植入体称为颈椎前路椎间盘器械 (ACID)。
首先,IMR公司提出了一个设计项目,研究如何利用增材制造技术帮助改善患者结局。然后,使用nTopology公司提供的设计软件为脊柱植入体设计复杂的网状结构。最后,使用雷尼绍RenAM 500M增材制造系统制造植入体。
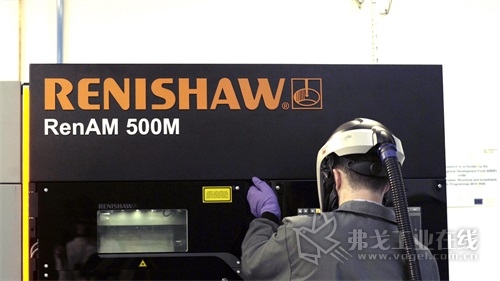
使用雷尼绍增材制造系统打印植入体
IMR公司通过广泛研究确定了特定病例最适合的植入体尺寸以及在日常生活中,甚至奔跑或跳跃等剧烈运动时,植入体必须承受的负载条件。此外还采集了需要接受脊柱植入体的患者的已知骨质特性。之后,三家公司联手设计了植入体的机械特性,也就是网状结构各个单元格的几何特征的函数,以尽可能接近人体骨骼的机械特性,优化多孔网状结构,从而改善骨整合。
植入体的设计参数确定之后,IMR公司使用nTop Platform软件生成了设计文件。然后,nTopology公司与雷尼绍紧密合作,实现软件与硬件互相兼容,从而将设计文件从nTop Platform上无缝传输到RenAM 500M上。
最后,IMR公司在RenAM 500M上利用Ti 6Al-4V ELI钛合金(等级23)制造出植入体原型。
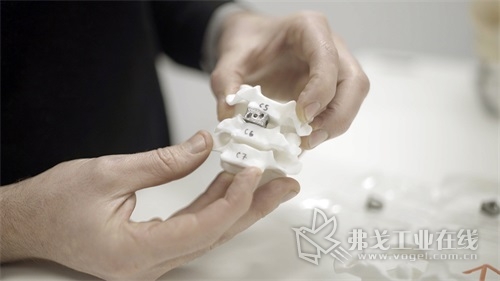
嵌入脊柱模型中的脊柱植入体
随后,IMR公司通过一系列测试证明了该植入体满足美国食品及药物管理局 (FDA) 规定的标准规格中的所有关键要求。首先测试了植入体的化学特性,确保其符合《ASTM F136外科植入体用等级23锻造钛合金的标准规格》以及《ASTM F3302通过粉末床熔融增材制造钛合金的标准规格》。然后根据ISO 13314测试了多孔结构的机械特性 — ISO 13314是一种测试方法,用于确定多孔金属材料的压缩性能和失效模式。最后通过ASTM 1104和ASTM 1147标准测试方法证明多孔结构不会从植入体本体上剥离。
IMR公司的高级研究工程师Sean McConnell解释道:“为了进行概念验证测试,我们在RenAM 500M的加工托盘上制造了一批参照品,并对这些参照品进行了破坏性测试,以确定植入体的化学、冶金和机械特性。”
结果
概念验证测试的结果表明:传统制造工艺无法制造的脊柱植入体特性可以利用增材制造技术实现。植入体原型和成品植入体均在RenAM 500M上制成,因此无需在不同的机器之间传输加工程序。简化的制程可帮助医疗产品制造商大幅节省成本和时间。
McConnell先生解释说:“两年前,IMR还没有增材制造部门。雷尼绍在脊柱植入体开发项目以及其他项目中给予我们大力支持,帮助我们的技术人员熟练掌握相关技能,令我们公司在增材制造领域赢得一席之地。”
他补充道:“如今,我们能够将雷尼绍传授给我们的增材制造专业知识提供给我们的客户。我们的许多合作伙伴之前都因为缺乏增材制造专业知识而对增材制造望而生畏,而现在却正在使用增材制造设备赢得竞争优势。
McConnell先生继续说道:“雷尼绍不辞辛劳地与我们一起改进脊柱植入体的增材制造工艺。在双方的共同努力下,我们通过一系列测试确定了一套最合适的产品参数设置,从而将实现植入体关键特征所需的后处理量减少了九成。”
雷尼绍医疗和口腔产品部市场经理Ed Littlewood解释道:“IMR公司能够极大地推动将先进的制造技术引入爱尔兰工业。它们凭借深厚的设计专业知识和严谨的研发精神成功制成了一批具有代表性的脊柱植入体,而这些植入体展示了增材制造技术变革医疗行业的潜力。”
除了证明增材制造技术在制造脊柱植入体方面极具优势外,该研究还表明:如果在早期阶段将增材制造设计 (DfAM) 纳入考量,则可以减少支撑的使用,从而减少精加工操作。
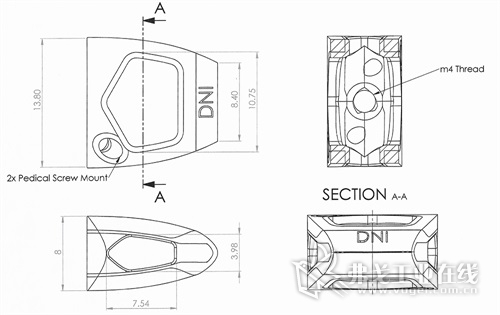
在早期概念开发阶段设想的多种产品设计和特征
Scott解释道:“通过此脊柱植入体项目,我们加深了对医疗产品生产和增材制造机器能力的了解,从而开发出我们的设计软件,为推广先进制造技术在医疗产品行业的应用添砖加瓦。”
他补充道:“为了实现这款软件与RenAM 500M互相兼容,我们进行了大量测试,解决了不计其数的问题。而且,在雷尼绍工程师的大力帮助下,整个过程得以顺利且高效地完成。这样的项目一般需要耗时多年,但是nTopology公司、雷尼绍、IMR公司三方精诚合作,在短短几个月内就顺利完成了这个项目。”
Scott总结道:“我们将继续与雷尼绍紧密合作,为行业提供增材制造技术。我们的目标是推动行业展开更广泛的先进制造合作。”
评论
加载更多