随着机床和刀具技术水平的不断提升,尤其是五轴数控加工中心的问世,以往几乎无法处理的钛合金、高温合金等难加工的材料,现如今已经可以实现更高加工效率、更高质量和更高精度。而五轴数控加工中心作为航空航天领域的核心加工设备,更是发挥了不可替代的作用,是解决叶轮叶片等零部件加工难题,提高生产力和缩短生产周期为数不多的手段之一。其中,来自德国格劳博集团的五轴联动通用加工中心G150/G350/G550/G750所独具的高精度、高稳定性、高动态性以及强大的综合性能,使其毋庸置疑地成为了航空航天领域难加工材料优秀的技术攻坚者。
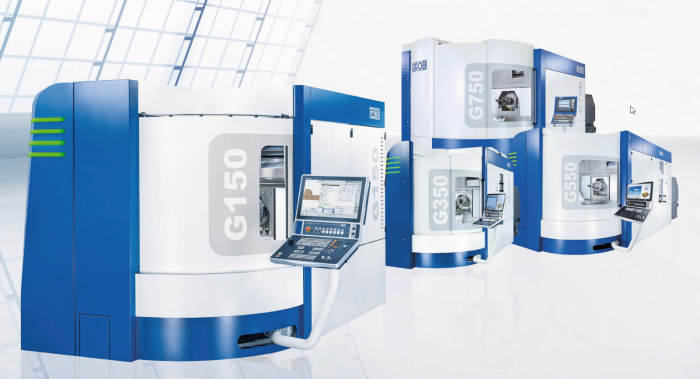
格劳博五轴联动通用加工中心G150G350G550G750
格劳博五轴联动通用加工中心G150/G350/G550/G750,为航空航天领域的每一位客户提供了最大的施展空间,帮助其在铣削各种材料制成的零件时,几乎不受任何限制。五轴联动通用加工中心G150/G350/G550/G750具有独一无二的设计理念,如卧式主轴可达到同类机床中最长Z轴行程和最佳排屑效果;轴的独特布局,将导轨与工作点(TCP)之间的距离降至最小,使机床具有最佳稳定性,非常适合加工钛合金等硬金属。同时,五轴联动通用加工中心G150/G350/G550/G750的“隧道” 概念保证了在使用最长刀具时机床各旋转轴都不受任何限制,仍然能够实现最大工件的加工;三个直线轴和两个旋转轴,可通过一次装夹便实现五面加工和五轴联动加工,从而能够消除重复装夹对工件精度产生的影响,降低夹具成本并显著缩短加工时间,带给航空航天领域客户所需的高性价比和高加工效率;A’轴 与 B’轴的倾角范围分别为 230°和360°,最大程度的提供了加工自由度,能够进行符合航空航天领域要求的更高可靠性的加工。
“空间至简,技术至臻”是格劳博专为第二代五轴联动通用加工中心G350和G550提出的。得益于集成式刀库的智能化全新布局,机床宽度减小了18.5%,全新开发的换刀臂显著提高了动态性能;扩大的刀库容量不仅使机床的准备和切对切时间缩短了30%,智能化的刀具管理和刀库技术的极佳可操作性还使机床具备了更加出色的加工灵活性,以应对航空航天领域工件批量小、种类多、工艺流程复杂的特征。这些都促使第二代G350和G550具备更加出众的加工性能和效率,在保证技术领先的同时能够完美满足航空航天领域对于加工的苛刻要求,为客户提供极具竞争力的解决方案。
同时,格劳博五轴联动通用加工中心G150/G350/G550/G750还可以配备多样化的软件选件。航空航天领域的客户可选择使用Siemens、Heidenhain、Fanuc等三种数控系统,配合GROB4Pilot机床控制面板,能够进行简单直观且功能强大的机床操作;格劳博主轴碎屑检测系统(SiS)、刀具激光测量系统和测量探头等智能化故障监控诊断选项,能够时刻保障机床加工的高效、高可靠运行。据了解,在航空航天领域中,加工类似钛合金,高温合金等难加工材料是一项高难度高成本的工作,如果能在加工过程中严格控制误差,降低各种风险所带来的干扰,才能有效降低零部件加工成本,以保证所期望的利润回报率。
除此之外,格劳博五轴联动通用加工中心G150/G350/G550/G750不仅可以作为独立机床单独运行,还可以配合丰富的自动化解决方案——格劳博一站式自主研发设计的托盘存储系统和托盘交换系统,以及个性化的工业机器人上下料解决方案,来进行几乎无人值守的自动化生产,无论生产批量大小,都能够实现最大的生产灵活性。根据客户特定的要求,格劳博还可以提供三种尺寸的通用车铣复合加工中心G350T/G550T/G750T,除了通过三个直线轴和两个旋转轴实现的五面加工和五轴联动加工之外,独有的GROB-TRAORI车削使得刀刃能够按照工件轮廓动态对齐,因而能够显著延长刀具寿命并使用较短的刀具来进行一次装夹完整加工,为航空航天领域的创新性应用开拓高效灵活的无限可能。
评论 0
没有更多评论了