为了减轻汽车的重量,汽车生产厂家必须使用非常耐用的材料制造尽可能轻、结构尽可能紧凑的变速器。Sandvik Coromant公司介绍了为什么强力刮齿技术对成功地生产轻便、紧凑的变速器是至关重要的。
对汽车制造商和OEM原始设备制造商来说,电动汽车领域的快速发展呈现了未来的汽车将会摆脱传统内燃机的大趋势。电动汽车的市场是一个多样化的、竞争非常激烈的市场。这里也是大型公司、小公司和全球扩张的制造商们众星汇聚的地方。然而,电动汽车的生产也带来了一些挑战和风险;面对这些挑战和风险,手握传统制造工艺技术的企业可能会落伍。
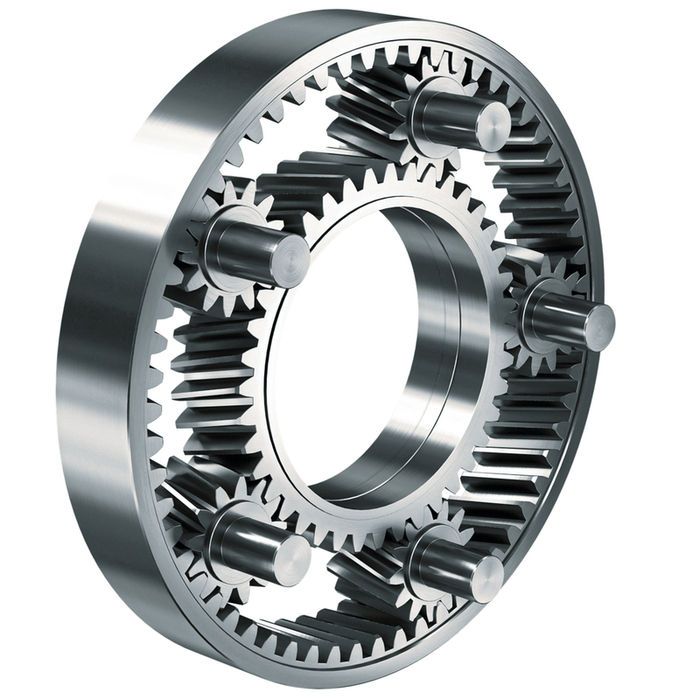
图1 电动汽车中的减速装置一般都设计为行星齿轮减速器,其中的行星轮和太阳轮都在一个结构紧凑而且轻便的内齿圈中
电动汽车的变速器是一个可以降低车辆行驶速度、经济地控制和驾驶车辆的减速装置。由于电动汽车没有发动机运转时产生的噪音,所以驾驶员可以轻松的感知到变速器产生的任何噪音。因此,电动汽车变速器生产制造过程中的一项重要任务就是降低噪音。电动汽车变速器是否结构紧凑、重量轻且低噪音,这一切都取决于它的加工质量。
电动汽车中的减速装置一般都设计为行星齿轮减速器,其中的行星轮和太阳轮都在一个结构紧凑而且轻便的内齿圈中。由于内齿圈的壁厚非常薄、对其圆度有着非常高的要求,因此内齿圈也是整个减速装置中最难制造的零件之一。传统的切削加工工艺技术是很难满足这些要求,更重要的是:它的加工时间和加工成本都不占优势。
通常情况下,内齿圈传统的切削加工都是在专用设备上完成的,而每台专用设备都有自己特定的加工范围。因此,随着切削加工内容的变化被加工零件就要在多台不同的设备上依次加工, 按照一定的“工艺路线”在多台切削加工机床组成的“生产线”上完成全部生产制造。这样的生产线缺乏灵活性,尤其是在被加工产品的设计略有改变时。另外,由于工件在不同加工设备上多次装夹,因此工件的同轴度和偏心公差也会受到影响。此外,后续的热处理也更难控制、热处理前的内齿圈齿面加工和后续的磨齿加工的生产成本也非常高。另外,这些切削加工工艺过程通常需要使用冷却润滑液以支持切削加工和排屑。
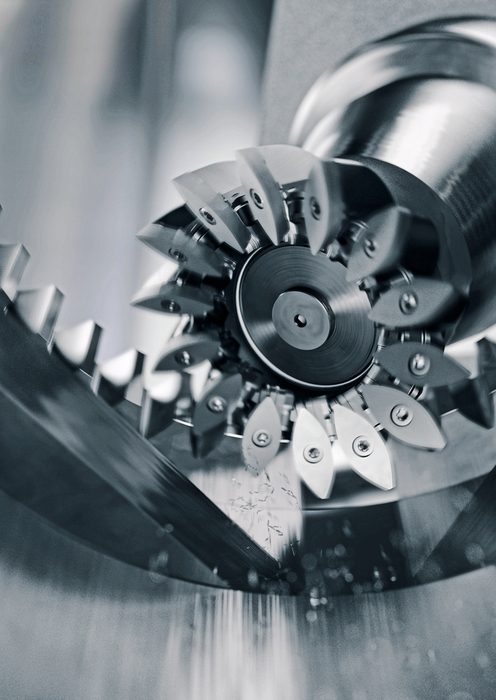
图2 Sandvik Coromant公司研发的高品质Coro Mill 180强力刮齿刀具;并针对电动汽车变速系统的精密加工而优化
鉴于电动汽车越来越普及,上面讲到的这些缺点和不足越来越变成传统汽车发展的障碍和阻力。因此,新型变速装置的研发速度必须更快、生产加工效率必须更高并且生产设备也必须更加灵活。另外,投在新型变速系统中的资金也必须更快的回收;这也是为什么使用灵活性差的专用设备会变得越来越不利的原因。
在这一背景条件下,制造商们应该对自己的生产制造过程进行现代化技术改造。例如,常规的磨齿机价格非常昂贵,因此投资能够完成多种加工工艺的“复合型”加工设备是一种很好的替代解决方案。在这类设备的帮助下,变速系统的切削加工可以分为“软加工”和“硬加工”两道工序,而且是能够在一台复合型设备中完成的。
在多功能复合型加工设备的帮助下可以减少许多不同的加工工序、缩短切削加工工时、降低产品的生产成本并提高产品质量。除了提高产品质量之外,与现有的常规加工工艺技术相比较它还有更短的生产周期或者至少是相同的生产周期的好处。因此,在实践中Sandvik Coromant公司能够为最终客户降低至少30%的成本费用。
由于采用强力刮齿工艺不仅可以减小变速装置的体积而且还可以减轻它们的重量,因此可以使未来电动汽车生产设备能够实现更大的使用灵活性。这一技术不仅可以用于内齿轮的生产而且也可以用来加工外齿轮。它在内齿圈加工和大批量生产时特别有效,因此在缩短生产时间方面有着至关重要的作用和意义。
一个多世纪前就研发成功的强力刮齿技术是生产内齿圈的有效方法,而行星齿轮变速器中的内齿圈也是最难加工的零件之一。它将滚齿和插齿两种不同的齿轮加工工艺结合到一个连续的切削加工过程中。
多功能复合型加工设备与传统齿轮加工技术相比有许多优点:可以提高整个工件的生产效率、提高了机床设备的使用灵活性。由于不再需要加工齿轮的专用设备,因此不会因多台设备中多次装夹而影响工件质量。与传统的拉削、滚齿和插齿工艺技术相比较,强力刮齿技术工艺技术明显的缩短了总工时,有利于实现可管理的和可预测的零部件加工。
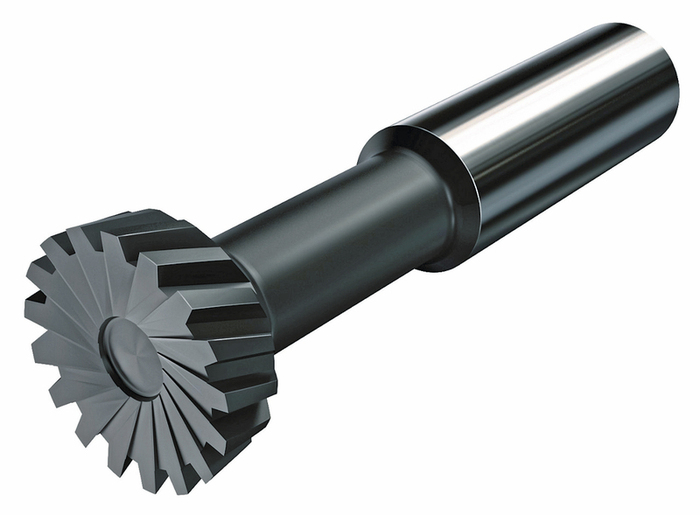
图3 Coro Mill178强力刮齿刀具有两种:一种是PM-HSS粉末冶金高速钢材料的刀具,另一种是全硬质合金材料制成的刀具;可以用于加工传动齿轮、齿形花键等等
自2014年以来,已经有700多台强力刮齿设备在用户那里投产使用;这表明强力刮齿技术越来越受到人们的喜爱。其中,60%的强力刮齿设备都是在一次装夹中完成全部切削加工的。这不仅提高了工件的加工质量而且也实现了高效的切削加工。
Sandvik Coromant公司开发了专门用于电动汽车变速装置精加工用的高精度强力刮齿设备。这其中就包括了Coro Mill178强力刮齿刀具,一种有着两种不同的强力刮齿刀:一种是PM-HSS粉末冶金高速钢材料的刀具,另一种是全硬质合金材料制成的刀具。Coro Mill180可转为刀片安装在棱柱形的刀体上,确保了可以实现最高的、有着很好重复精度的强力刮齿加工。在刀具的刚度、悬伸性能和冷却液供给等方面都进一步得到了优化,大大延长了刀具的使用寿命。凭借这种有利的性能组合,使新型的强力刮齿刀具有着更高的可靠性,可以完成连续性的切削加工。
一家低合金钢主变速箱的制造商正在寻找一种替代耗时费力插齿加工的工艺方案。在Sandvik Coromant公司新型强力刮齿刀具的帮助下,使该公司能够用强力刮齿替代现有的齿轮加工技术了,并用两台多功能复合设备完成原来四台专用设备才能完成的任务。它使内齿圈切削加工的时间减少90%,并显著的延长了刀具的使用寿命。在常规情况下,强力刮齿比传统的齿轮加工方法快2~3倍。
强力刮齿是齿轮加工领域中增长最快的一种工艺技术,具有显著的时间和成本优势。但“漏洞”总是有的:一些小型制造商可以更好的参与齿轮加工的市场竞争,对于大型的齿轮制造企业来讲,正如约翰·麦基先生所说:“强力刮齿工艺技术有助于找到‘摆脱自满的方法’。”
评论
加载更多