高档数控机床及装备是制造业的基础,代表了国家的核心竞争力,决定了国家在经济全球化进程中国际分工地位的关键因素。而数控系统是机床装备的“大脑”,决定了高档数控机床的功能、性能。特别是五轴联动等数控系统和数控机床,高档五轴联动加工中心是实现异形复杂零件高效、高质量加工,是一种科技含量高、精密度高,专门用于加工复杂曲面的机床。五轴联动机床在航空航天工业、科研、精密器械、高精医疗设备和模具制造行业等都有特别广泛的应用。近些年来,在国内各界的共同支持努力下,我国的五轴联动数控机床技术有了很大的提高,武汉华中数控股份有限公司掌握了五轴联动的许多关键技术,拥有了自主知识产权的五轴数控系统。而国内几大数控机床厂家正先后努力研制五轴联动关键技术,而五轴RTCP功能也是被国内数控系统厂商攻克的五轴联动关键技术之一。
华中8型五轴数控装置软硬件体系结构采用开放式、全数字、总线式数控系统体系结构,以及“硬件可置换,软件跨平台”的技术方案,在总线拓扑结构方面,采用环形或线形结构,连接具有标准总线接口的伺服驱动、I/O单元或数据采集模块,使得五轴系统与不同的转台数控机床灵活的组合在一起。华中8型五轴数控系统现已应用在AC摆头五轴龙门加工中心、BC摆头五轴立式加工中心、动梁龙门式五轴加工中心等五轴高档数控机床。
华中8型五轴数控系统关键技术包含高速高精运动控制技术、多通道控制技术、纳米插补与平滑技术、高级误差补偿技术、双轴同步控制技术、五轴联动关键技术、数控加工三维仿真与机床防碰撞技术、G代码质量评价与优化、会话式编程技术等,而五轴联动关键技术中的五轴联动RTCP控制是高性能五轴数控系统最为核心的基础功能。
五轴联动RTCP控制功能(Rotated Tool Center Point)即刀尖点跟随功能,在五轴加工中,追求刀尖点轨迹及刀具与工件间的姿态时,由于回转运动,产生刀尖点的附加运动。为了保持刀具中心点和刀具与工件表面的实际接触点不变,RTCP功能常用在双摆头结构上,应用摆头旋转中心点来进行补偿。
五轴联动RTCP功能能够加大提高加工效率、缩短加工周期、提高加工精度。具备RTCP功能的五轴数控机床可直接输入刀位点坐标和刀轴矢量数据,经过数控系统的RTCP预处理模块、运动控制模块、RTCP实时补偿模块、插补模块处理后驱动机床运动,其中RTCP预处理模块实现“后置处理”功能,RTCP实时补偿模块用来对非线性运行误差进行实时补偿。实际加工中,当刀具长度或工件位置改变后,只需将测量改变值输入数控系统,数控系统会自动进行坐标更换处理;无需重新用CAM软件进行后置处理;RTCP功能会对每个插补周期或者每行程序进行非线性误差补偿,而不具备有RTCP功能的数控系统则不能进行非线性误差补偿,从而证明五轴数控系统是否支持RTCP功能会对CAM“后置处理”编程过程产生复杂影响。
华中8型五轴数控系统可通过参数设置开启或关闭RTCP功能,现通过常规加工试验论述开启和关闭RTCP时CAM程序编辑和对刀操作的差异性,展现应用RTCP与非RTCP功能的区别及RTCP功能的优势。一台BC双转台配华中8型五轴数控系统的机床,机床夹具安装直径100 mm×高度150 mm圆柱棒料,并选取圆弧为半径5 mm的球刀。
选择国际标准五轴加工测试案例中圆弧曲面加工测试,应用CAM中的UG软件编辑数控加工程序,加工工艺采用五轴加工中较为代表的平行轨迹加工程序,以小直线段拟合圆环圆周截面圆弧曲线,在各个小直线段端点给出该点处的圆环面法向。在数控加工程序中设定刀具轴线与圆环面法向的倾斜角度和方向,刀尖沿小直线段运动。运动过程中刀具轴线由小直线段起点方向插补运动到小直线段终点方向,在端点处保持与圆环面法向的倾斜角度和方向。
以特定编程方式指定刀具姿态,实现连续路径加工。刀具由原点运动到P1,姿态为T1’。T1’为P1点处圆环的法线方向;V1为P1处圆环的切线方向;A1为10°,在V1-T1’平面上;B1=30°,刀具以行切方式运动到程序终点P3,程序段长度为0.2~0.5 mm(任选),行距为2~6 mm(任选),刀具轴线在各程序段端点处与该点的圆环面法线保持前倾角、后倾、左倾、右倾A1角度(如图)。
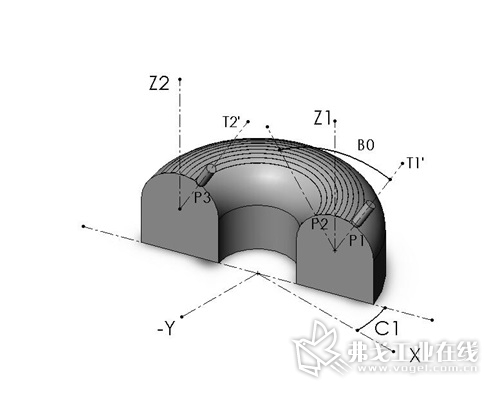
平切测试示意图
应用BC双转台配华中8型五轴数控系统的机床进行典型零件加工试验,通过关闭和开启RTCP功能时加工同一类型的圆弧曲面零件时,关闭RTCP功能后的整个实验过中CAM程序编辑和对刀操作相对复杂,如更换工件或刀具时,需要重新测量旋转中心到摆动中心偏置距离与零件编程零点到C轴中心偏置距离,其程序要重新编写,而开启RTCP功能时不需要。从上述试验的编程与操作过程可知关闭RTCP功能时,操作者需要测量更多的值,操作非常繁琐,还需要考虑测量误差及机床结构误差等。而开启RTCP功能时编程加工操作更为简单,降低五轴加工操作人员的门槛;五轴数控系统支持RTCP功能优势:编程变得简单、高效;提高加工精度;多台同结构的机床加工时程序均可通用,程序通用性强。
评论 0
没有更多评论了