DH参数校准模块
(Denavit-HartenbergModeling&Calibration)
(上接)
c). DH模型补偿的基本原理
在软件中模拟机器人控制器中的DH模型后,接下来选取一系列位姿进行校准测量,如果想要获得机器人全范围内精度优化,那么这些校准位姿的各关节角需要尽量在行程范围内均匀分布,各关节角之间尽量多任意组合;如果只关心机器人在特定工作区域内的精度优化,可以将校准位姿选取在常用工作区域内。在这一系列校准位姿下,机器人的理论末端位置可以由理论模型根据关节角正解求出,再用激光跟踪仪或其它测量仪器测量机器人末端实到位姿,理论和实测两组数据之间对照得到的偏差作为优化的目标函数(通常是选取所有位姿下的空间距离误差的均方和为目标函数),联立方程组,对DH参数模型中的全部或部分变量进行优化求解。测量数据可以是一维数据(如Dynalog系统采用的一维线轴测长的硬件),三维数据(激光跟踪仪球靶或者活动靶标),也可以是六维数据(包含位置和姿态角的六自由度传感器)。测量数据的维数越多,方程的个数意味着输入条件越多,越有利于解算出有效的信息。例如,在同一位姿下,采用API智能靶标STS得到六维测量数据,可以比较好的区分来源于J1-J3的位置误差和来源于J4-J5的姿态误差。同时,为了保证校准姿态的多样性,使用主动靶标或智能靶标的测量系统会大大优于使用标准球靶的测量系统,后者姿态会受限于靶球的入射角(虽然理论上在校准过程中可以转动球靶,但是在追求效率的流水线校准操作中这样做是不现实的)。
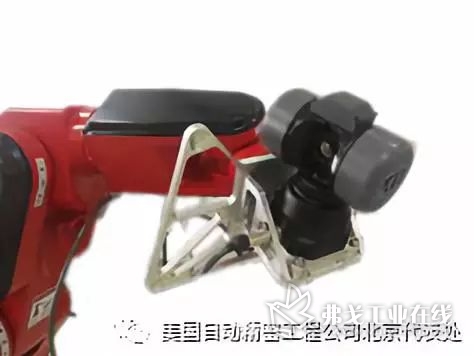
二、影响机器人位姿准确度的主要因素:
a). 关节角的旋转分度误差
机器人通过转动关节角来到达指定位置,所以旋转角度的准确度最为重要。导致旋转误差的因素又可以细化为减速比(传动比)误差、传动系统反向间隙、重力变形等。
减速机是工业机器人的一个重要机械部件,他的作用是将伺服马达的高速运动,精确转换为关节的低速运动,并放大驱动扭矩,类似汽车变速箱,一般说的减速比是指伺服电机码值和关节实际转角之间的比值,由于减速机机械制造和装配中存在误差,每台减速机的减速比值都会与设计值有一定出入(主要是齿轮加工和装配误差导致啮合节圆半径的变化),这将导致机器人关节角的执行精度变差,根据经验,通常关节角执行相对误差可在0.01%~0.1%。虽然看起来很小,但是如果发生在连杆长度较大的J1-J3关节,足以导致毫米级的位置偏差,在第四到第六关节上,则主要影响末端姿态角的准确度。目前市面上的其它机器人补偿软件大多将减速比和其它DH参数一并用同一组测量数据进行混合求解,在减速比误差本身较小时,这样做问题不大,但如果减速比本身偏离较大,实际求解效果会很差。其一是因为,某一关节上减速比和θ零位参数相当于一个线性补偿方程的斜率和截距,要想获得理想的补偿效果,对单个关节来说,用于计算求解的数据必须在其整个行程内均匀分布,在有限数量的校准位姿中往往无法做到这一点;其二是算法无法区分来源于减速比和其它连杆参数的误差,表现为,即使本组数据求解效果看似很好,但如果更换一组位姿去验证,结果仍不理想。API RMS系统推荐采用专门的校准测量来标定减速比误差,在减速比标定完成后用户可以选择立即更新控制器内部参数,也可以选择将减速比补偿离线应用到DH参数校准的测量数据上。
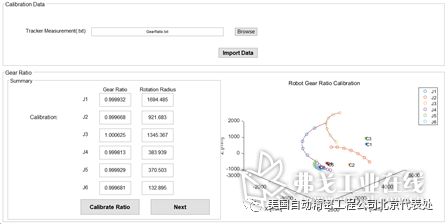
评论 0
正在获取数据......