增材制造技术,俗称3D打印,是一种依据零部件的三维数字化图形,自下而上、逐层累加的材料添加制造过程。与传统的车、铣、刨、磨等“减材制造”工艺,以及铸、锻、焊等“等材制造”相比,增材制造是一个非常典型的数字化制造过程。
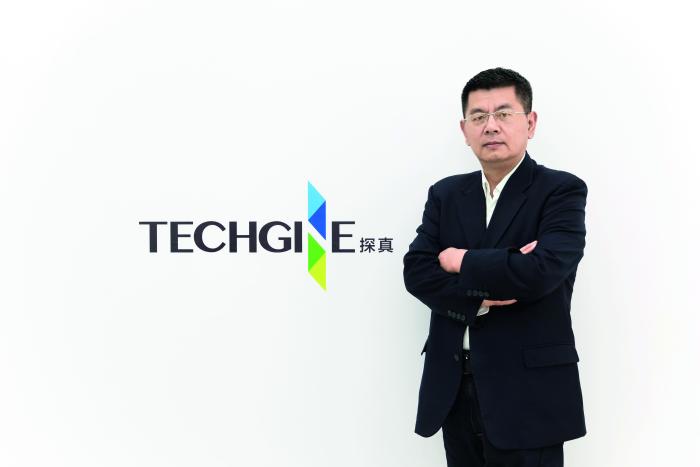
曾晓雁 华中科技大学 武汉光电国家研究中心
增材制造工艺的基本技术特点
按照工程材料种类不同,可以将增材制造技术分为塑料增材制造,陶瓷和玻璃增材制造,以及金属增材制造技术等。金属增材制造技术按照所成形零件的致密度不同,又可分为非全致密的金属零部件增材制造技术和全致密金属零部件增材制造技术。按照所采用的热源种类不同,又可分为激光增材制造、电弧熔丝增材制造、电子束(熔丝或者粉末床)增材制造和离子束增材制造等。其中,激光增材制造技术是当前各种增材制造工艺中发展最快、应用最广的全致密金属零部件增材制造工艺。
按照材料添加的方式不同,可以将金属零部件激光增材制造技术分为两类:一种是基于同轴送粉的激光熔化沉积技术(Laser Metal Deposition),简称LMD技术。它采用高功率激光(例如输出功率达到15 kW的光纤激光器),结合5轴联动机床,在保护气氛环境下进行增材制造,主要技术特点包括:可成形零部件的尺寸大,设备相对简单。例如,LMD设备成形零部件的最大尺寸投影面积可达10 m2以上,能够满足超大尺寸零部件成形要求,成形效率较高。主要不足在于成形精度偏低,需要通过后续机械加工才能达到零件的成形精度要求。
另外一种金属零部件激光增材制造技术是基于粉末床铺粉的激光选区熔化成形技术(Selective Laser Melting),简称SLM技术。该技术采用独特的铺粉装置将粉末层均匀预置在成形缸表面,然后采用聚焦激光束按照金属零部件的切片图形轨迹进行逐点、逐道、逐层扫描加工,从而实现金属零部件的高精度制造。SLM技术的主要优点包括:成形精度高:最高成形精度可达±50μm,非装配面可免后续加工,可以适合制造结构非常复杂的零部件,往往具有不可替代性;构件性能好:由于SLM成形过程中熔池的冷却速度极高,使得所成形金属零部件的晶粒尺寸很小,因此力学性能相当优异。例如,316L不锈钢的SLM成形构件屈服强度几乎是同成分锻件的3倍,延伸率还能够保持较高水平。
SLM技术的主要不足在于两点:一是成形效率低,一般只有5~20 cm³/h;二是单光束激光成形尺寸偏小(常用SLM设备的成形尺寸250×250×300 mm³),因此在应用中受到很大限制。近年来,采用多光束激光进行成形,成形效率有数倍提高,最大零件尺寸达米级,能够满足中型尺寸金属零部件的精密成形要求。但是,对于大尺寸金属构件而言,成形效率仍然偏低,导致成本居高不小,迄今为止仍然主要局限于航空航天等高端制造领域。
通过比较SLM技术与LMD技术的特点,不难看出,SLM技术可成形精密复杂结构,精度更高,能够实现复杂构件的结构功能一体化制造,在许多技术领域具有不可替代性,应用前景更广。因此,下面重点讨论SLM技术的发展现状与趋势。
发展现状与趋势
SLM技术从小零件、高精度成形起步,成形尺寸不断扩大,成形效率不断提高,从航空航天领域逐步向各个领域渗透。在航天领域,SLM技术早期主要用于火箭发动机微型喷射器与燃烧室铜合金衬套,以及卫星连接用钛合金插入件等复杂结构件的制造,近年来逐渐向航天发动机各种复杂金属零部件拓展,甚至包括运载火箭箭体中复杂结构的制造;在汽车制造领域,SLM技术也开始应用于各种复杂金属构件的制造,比如热交换器等;在模具制造领域,SLM技术主要用于带有内流道的复杂随形冷却的模具,可以使模具性能大幅度提高等。
随着人们对SLM技术的认识不断加深,在市场的牵引与驱动下,SLM技术与装备正向着大尺寸成形缸、多光束同时成形方向快速发展。实际上,早期大尺寸SLM成形技术主要采用两种技术,一是采用单激光头,运用长焦距f-θ场镜进行成形,采用的激光器功率和效率有所提高,但是不足之处是激光光斑较大,导致成形精度显著下降,但是成形效率提升幅度有限。二是单台激光振镜在运动机构驱动下沿着不同加工区域移动,这样可以保证光斑尺寸不变、成形精度不变,但是成形效率过低。自华中科技大学2015年在国际上首次研制出4光束SLM成形设备以来,目前,多振镜拼接并行扫描成为大尺寸SLM成形技术装备的主流方向,它能够在保证成形精度的前提下,成形效率进一步提升。
无论SLM成形技术的成形精度有多高,还是无法和车削、铣削之后的制造精度相提并论的。为了充分发挥SLM成形技术结构功能一体化的特征,同时进一步提升所成形金属零部件的成形精度,SLM技术的一个发展方向是SLM增材/减材复合制造。换言之,就是让SLM增材制造过程与减材制造加工过程交替进行,从而实现复杂零部件的高精度加工。其最大特点是,可以使得SLM成形的金属构件得到铣削加工的表面粗糙度与尺寸精度。
前景预测
通过对典型金属增材制造技术特征对比发现,成形效率和成形精度是两大关键参数。本人认为,SLM技术是未来最有发展前景的增材制造技术之一,但是必须先克服SLM技术存在的一些重大技术瓶颈,其中最关键的还是成形效率低、成形周期长以及制造成本较高等。其实最核心的还是成形效率问题。因此,下一步激光选区熔化增材制造技术领域需要重点突破的方向是:如何在确保成形构件性能、不明显降低构件尺寸精度的前提下,尽可能提升SLM成形效率,降低制造成本,让企业用得起,用的好。
综上所述,基于粉末床的激光选区熔化成形(SLM)技术将逐渐成为主流制造技术,在未来十年的高端制造领域中大放异彩,并成为金属增材制造领域的关键技术与装备。如何在确保零件性能、尺寸精度不明显降低的前提下,进一步显著提升零件成形效率,是决定该技术能否尽早突破技术瓶颈,成为真正颠覆性、主流制造技术的关键所在。
评论 0
正在获取数据......