在工业生产的每个角落里,合适的工具是让工作事半功倍的关键之一。令人困扰的问题是,有一些工具无法通过传统的加工手段制备。增材制造在这个时候就展现了它的优势,这些工具通过简单的设计优化后即可用增材制造实现生产。
Any-Shape是通过增材制造技术为具有特殊需求的客户提供专用工具的专家,其工程部门借助增材制造技术实现了航空航天专用铝制工具的制造。受之前制造工艺的限制,旧版铝制工具内表面只能实现简易的压花。而新的工具设计需要复杂的内部表面,显然这一要求无法通过传统方式进行机加工。因此,Any-Shape决定利用EOS M 290来制造该工具。
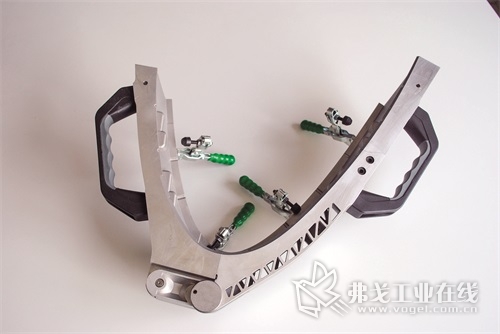
图1 精密铝制工具不但要具有复杂的压花内表面,同时还要满足对表面粗糙度和精度的严苛要求
面临的挑战
在整个制造过程中,Any-Shape面临的挑战包括以下几点:首先,客户需要能在工具内表面实现非常复杂的压花设计,而这种设计无法通过传统机加工方法来实现,因为刀具无法到达这些内表面。此外,在技术要求内,新的铝制工具对精度和表面粗糙度要求很高,非加工内表面的表面粗糙度为Ra 3.7±0.5 μm ,最终装配时的高尺寸精度为控制点位置0.05 mm,内表面公差为±0.1 mm。另外的两个挑战分别是,第一,工具必须尽可能轻,以让操作人员在使用时更加方便。第二,由于EOS M 290的构造尺寸限制,在增材制造后必须进行连接部件的组装集成。
凭借多年的增材制造经验,Any-Shape有信心满足这些苛刻的要求。该公司对增材制造设计、生产及后处理有着非常深入的了解,能够轻松地将需求转化为生产功能。使用EOS M 290系统以及独特的EOS铝合金材料和工艺,Any-Shape具备满足这种复杂工具的设计和技术要求、生产和后处理能力的所有技能,并且能按时交付最终产品。
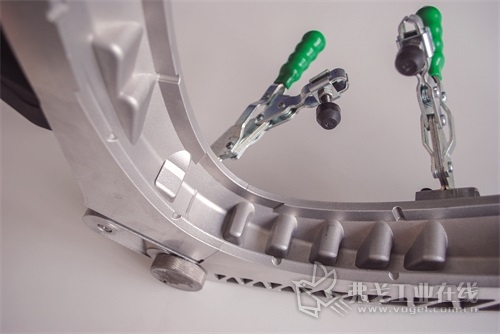
图2 打印的内表面压花平均粗糙度为Ra 4 μm
完整的解决方案
Any-Shape制定了完整的增材制造方案,以便同时应对所有挑战,他们必须考虑增材制造本身的所有参数,以及后续进行的装配操作。
在这套方案中,首先要采取的行动是把内表面定位在正确合适的角度以优化表面粗糙度,此定位位置决定了后续如何在零部件下方摆放支撑部件。由于上述位置的约束,还必须密切监测收缩线。靠近铰接区域的设计要进行略微修改,以允许更平滑的区域过渡,消除收缩线。
另外,还需要规划切割和组装方案。在方案设计时,保留一个平移自由度以实现装配。由于对表面精度的严格要求,该装配必须完全吻合。同时,粘合区域应该满足需要的剪切强度。由于制造设计中集成了垫片,粘合线厚度要确保在0.2 mm。最后,设计中还需要考虑一些参考位置,以便之后的装夹和机加工。
令人满意的成果
凭借Any-Shape的3D打印专业知识及其制造策略,新工具的不同零部件成功完成了打印、后加工、重新组装并成功通过质量控制。零部件主体通过喷砂进行表面处理,内表面粗糙度达到了Ra 4 μm,满足了客户要求。质量控制基于零部件的初始设计。尺寸也满足了公差要求。经过后处理的零部件表面精度在每个铰接臂内表面上达到±0.1 mm,在最终工具上达到±0.2 mm。最后一步组装时,在关节处切割和重新组装的接触面处都没有观察到偏差跳跃。
利用增材制造的独特优势,Any-Shape能够跨越传统制造和加工的极限创造出独特的工具。结合Any-Shape的专业技能和EOS成熟的增材制造技术,团队可以在很短时间内快速交付一个非常复杂的项目。
评论 0
没有更多评论了