厂址位于Neidlingen市Festool有限公司模具和工具制造部门的领导人Jürgen Kopsieker先生说:“我们部门共有大约25名职工,主要负责为Festool集团公司生产压铸模具、注塑模具和热固性塑料件的生产模具。”该部门是按照“利润中心”设计思路运营的;也就是说,该部门的人员、技术和成本都应能够满足市场提出的所有要求。它不是从Festool集团公司收到订单的,而是从母公司委托新产品开发和生产的系统供应商那里接收订单的。在与这些企业打交道时,模具制造部门必须能够提出比市场上更具吸引力的性价比才能赢得合同。另一方面,模具制造部门也可以从市场中获取订单;但这仅仅是为了提升自身的生产能力。除了生产各种不同的模具之外,各部门的业务还包括模具设计和工程技术领域的技术咨询与技术服务等内容。在这些业务领域中使用了现代化的CAD-CAM工具,例如Creo-Parametrics或者Hypermill。
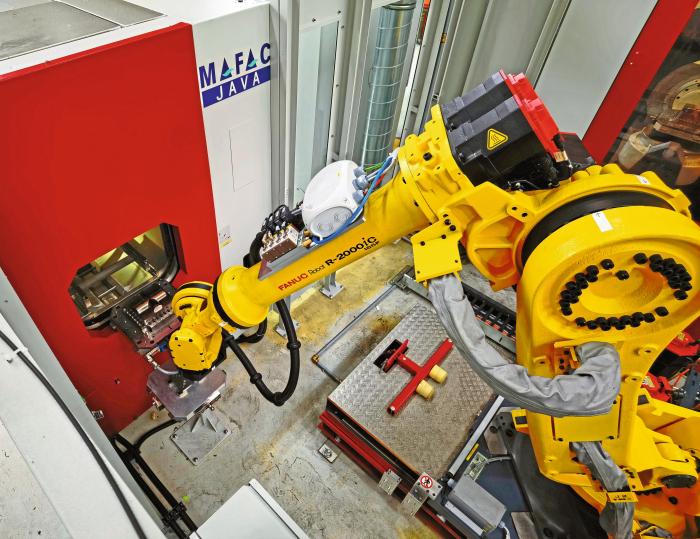
图1 托盘上的模具零件被送入Mafac清洗机中进行清洗
设备利用率并不令人满意
“大约三年半前我们还是一个老式的模具生产部门,共有5台绿色加工设备。”负责模具生产的计划员Tomislav Juria先生补充说道。这5台设备中有1台线切割机、1台电火花加工设备和3台铣削加工中心,其中1台是五轴铣削加工中心。按照传统的生产工作方式,这些加工设备都由设备操作人员负责观察设备的切削加工过程、装夹工件、上下料、调整设备和更换刀具等。除此之外他们还负责质量保证。
这时的设备利用率并不令人满意。出于企业发展战略的考虑,公司决定对模具制造部门进行投资,将模具生产技术提升到较高水平。“我们想要一个自动化的生产单元。这一生产单元中应充分集成各种先进技术,例如五轴铣削加工、电火花加工、三坐标测量和专业的湿式清洗设备,以便能将我们所有关键的模具生产技术自动连接起来。”Jürgen Kopsieker先生说道。
另外,还新增了刀具库和电火花加工的电极库,以及装夹在Erowa托盘上的“零件库”等。所有的物料运输和搬运任务都由安装在线性导轨上的搬运机器人来完成。这一生产单元内的所有加工过程都是在无人值守的情况下完成的。模具生产工人的任务就是向加工单元供应待加工毛坯,必要时更换新的刀具。另外,他还负责编写加工单元所有的加工程序。利用Röders公司研发设计的RMS Main任务管理器对这一加工单元进行控制管理。而这一管理控制与企业IT系统中的ERP企业资源管理系统IK Office相互连接。
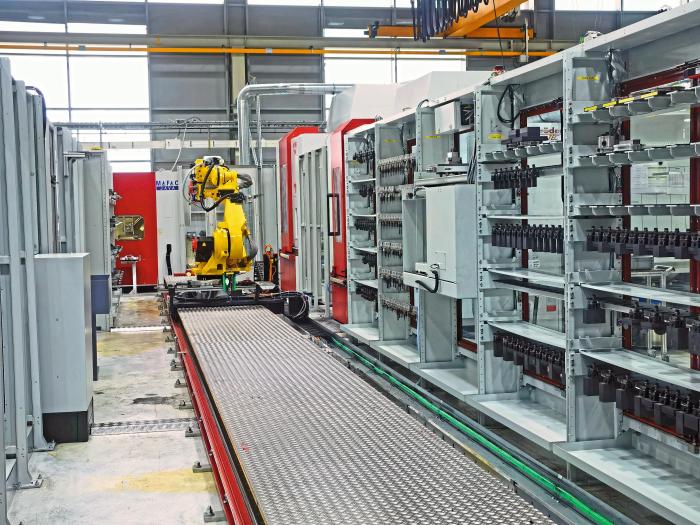
图2 在线性导轨上行驶的机器人为3台切削加工机床、1台三坐标测量仪和清洗机运送模具零件。原材料、刀具和托盘都保存在各自的仓库货架中
全面负责的合作伙伴
“基于两大原因我们选择了Röders公司作为对加工单元全面负责的合作伙伴。” Tomislav Juria先生说。首先是Festool集团公司其他部门使用的Röders铣削加工中心也是由Röders公司承担全部维护保养工作;而Röders公司的技术服务在保证设备性能、设备可靠性和加工精度等方面有着多年的丰富经验,给Festool公司留下了很好的印象。另一方面,多年来Röders公司在全自动生产单元的安装、调试和技术服务方面积累了丰富的经验,其中也包括为第三方设备生产厂家提供技术服务方面的经验。设备安装调试之后,整个生产单元包括4个Röders系统:2台RXP系列的五轴铣削加工中心、装卸机器人和RMS Main任务管理器系统。这一加工单元构成了Festool公司模具生产的骨干。另外,还有一个存储110件毛坯的托盘库和258支刀具的刀具库。铣削加工中心本身还带有自动换刀的换刀机器人。
RXP 601 DSH五轴加工中心主要用于石墨电极的生产加工;较大的RXP 950 DSH则用于硬加工,最常加工的金属材料是1.2343号模具钢,有时也可用于加工1.2379号冷作模具钢。这些材料的模具毛坯已经在前面的生产制造过程中经过了热处理淬火,硬度达到洛氏硬度HRC 54-60。与技术升级前的工艺过程相比较,也就是说在未淬火状态下粗加工、热处理淬火和最后精加工相比较,能够进行硬加工切削的工艺技术明显减少了生产时间和加工成本;因为新工艺大大减少了手工操作的工作量。
除了2台五轴加工中心之外,属于加工单元的还有1台Hexagon公司生产的三坐标测量仪、1台Exeron公司生产的电火花加工设备以及1台Mafac公司生产的自动清洗机。加工单元中的原材料进出、刀具和工具更换都是通过隔离防护门完成的。装夹在托盘上的模具毛坯经隔离防护门进入到加工单元内部,完成切削加工的模具零件也从隔离防护门中送出。加工单元内一切工作都是在RMS Main任务管理器的协调下自动化完成的,根本不需要操作人员人工干预。
“我对加工单元内各系统之间的协调工作非常满意。” Kopsieker先生说。RMS Main任务管理器是按照开放式系统设计的,带有与自身系统和第三方系统一相互通信、交换数据所需的所有接口。Röders公司的专家和来自Hexagon公司、Exeron公司以及Mafac公司专家之间的合作也非常好,确保了加工单元中各系统从一开始就能实现协同工作,并可靠地实现了预期的生产效率和加工质量。从2019年中期开始这一加工单元就一直在生产运行中,没有出现任何重大问题。现在,每周7天、每天24 h的全天候生产运行使其设备利用率大大高于原来的预期。Jürgen Kopsieker先生表示:“我们对目前的设备利用率和生产能力非常满意。”
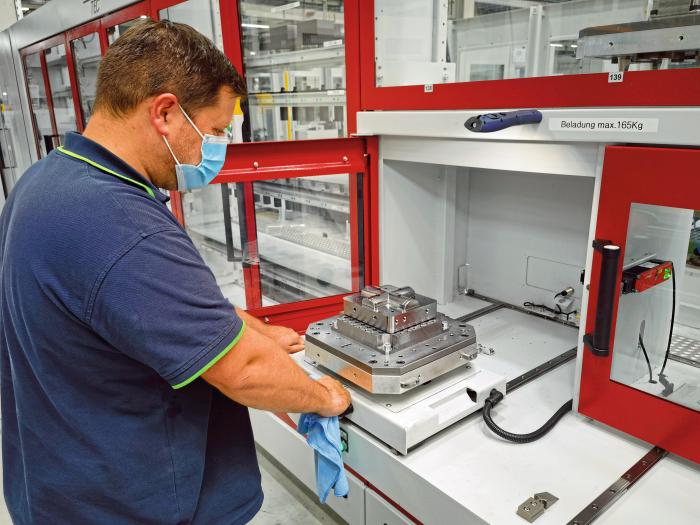
图3 托盘上的模具零件经隔离防护门进入加工单元
要想成功就必须让操作人员认可
“在相对较短的时间内在一个生产部门实行如此深刻的技术改造,得到员工的支持是至关重要的。”Tomislav Juria先生解释说道。
高素质且有责任心的员工是像Festool公司这样高新技术企业的决定性要素。如果企业没有一支这样的团队,无法让他们认识到高新技术的优点,那么即使购入的是技术最先进的设备,也不会在成功的道路中走的太远。毕竟这是用一套全新的工作流程取代企业员工早已熟悉的老一套了。
幸运的是,公司大多数员工都属于脚踏实地的、精通技术的员工。他们不仅接受了技术升级的必要性,而且也亲身感受到了技术升级带来的好处,并积极参与其中。因此,即使在模具生产和技术改造双重压力下也保持了不间断的模具生产。
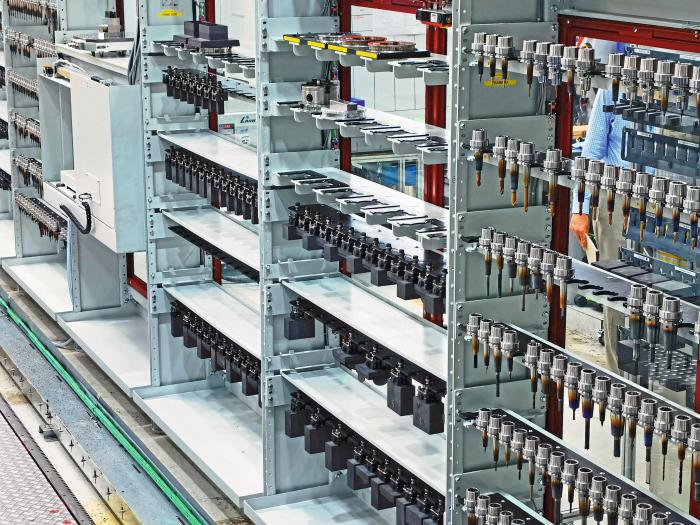
图4 加工单元的两侧排列着各种刀具和加工电极的石墨毛坯;它们后方是装卸用的隔离防护门
Röders公司开发的控制软件是一款以Windows操作系统为基础的应用软件,其有着非常明显的优势:更容易学习使用。加工单元控制程序的结构和编程使用,以及利用任务管理器对加工单元进行控制也都很好地满足了典型操作过程的要求。加工单元操作人员共需经过两次技术培训:第一次是为期一周的加工单元使用操作的技术培训,第二次是为期三天的任务管理器操作使用培训。如果在项目实施的启动阶段遇到问题就会快速地得到技术支持和帮助;这些技术支持和技术保障有时是从Röders公司Soltau市的总部给予的远程技术支持和帮助,有时则是Röders公司直接派人员进行现场帮助。
评论 0
没有更多评论了